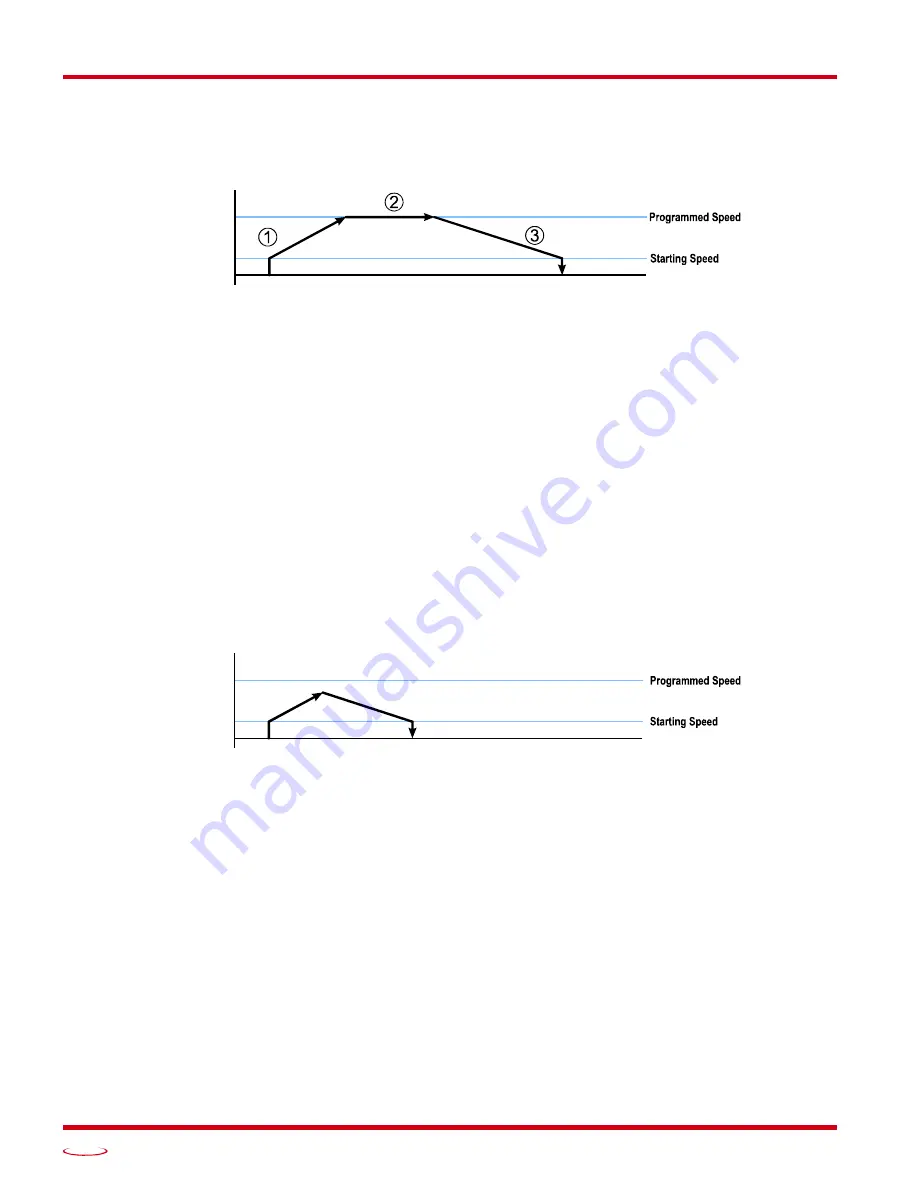
M
OTION
C
ONTROL
Networked Indexer/Driver User Manual
ADVANCED MICRO CONTROLS INC.
26
A Simple Move
As shown in the figure below, a move from A (Current Position) to B (Target Position) consists of several
parts.
Figure R3.4 A Trapezoidal Profile
1)The move begins at point A, where the motor jumps from rest to the configured
Starting Speed
. The
motor then accelerates at the programmed
Acceleration Value
until the speed of the motor reaches the
Programmed Speed
. Both the Acceleration Value and the Programmed Speed are programmed when
the move command is sent to the Networked Driver.
2)The motor continues to run at the Programmed Speed until it reaches the point where it must
decelerate before reaching point B.
3)The motor decelerates at the
Deceleration Value
, which is also programmed by the move command,
until the speed reaches the Starting Speed, which occurs at the Target Position (B). The motor stops at
this point. Note that the acceleration and deceleration values can be different in the move.
Figure R3.4 above shows a Trapezoidal Profile. A Trapezoidal Profile occurs when the Programmed Speed is
reached during the move. This occurs when the number of steps needed to accelerate and decelerate are less
than the total number of steps in the move.
Figure R3.5 below shows a Triangular Profile. A Triangular Profile occurs when the number of steps needed
to accelerate to the Programmed Speed and decelerate from the Programmed Speed are greater than the total
number of steps in the move. In this case, the profile will accelerate as far as it can before it has to decelerate
to reach the Starting Speed at the Target Position. The Programmed Speed is never reached.
Figure R3.5 A Triangular Profile
SP
E
E
D
POSITION
A
B
SP
E
E
D
POSITION
A
B
Содержание SD17060E2
Страница 1: ...MICRO CONTROLS INC ADVANCED U s e r M anual Manual 940 0S172 E2 Technology E2 Technology...
Страница 10: ...ABOUT THIS MANUAL Networked Indexer Driver User Manual ADVANCED MICRO CONTROLS INC 10 Notes...
Страница 22: ...UL CUL RECOGNIZED INSTALLATIONS Networked Indexer Driver User Manual ADVANCED MICRO CONTROLS INC 22 Notes...
Страница 54: ...CALCULATING MOVE PROFILES Networked Indexer Driver User Manual ADVANCED MICRO CONTROLS INC 54 Notes...
Страница 88: ...COMMAND MODE DATA FORMAT Networked Indexer Driver User Manual ADVANCED MICRO CONTROLS INC 88 Notes...
Страница 106: ...INSTALLING AN AMCI NETWORKED DRIVER Networked Indexer Driver User Manual ADVANCED MICRO CONTROLS INC 106 Notes...
Страница 130: ...ETHERNET IP EXPLICIT MESSAGING Networked Indexer Driver User Manual ADVANCED MICRO CONTROLS INC 130 Notes...
Страница 134: ...MODBUS TCP CONFIGURATION Networked Indexer Driver User Manual ADVANCED MICRO CONTROLS INC 134 Notes...
Страница 144: ...LEADERS IN ADVANCED CONTROL PRODUCTS ADVANCED MICRO CONTROLS INC...