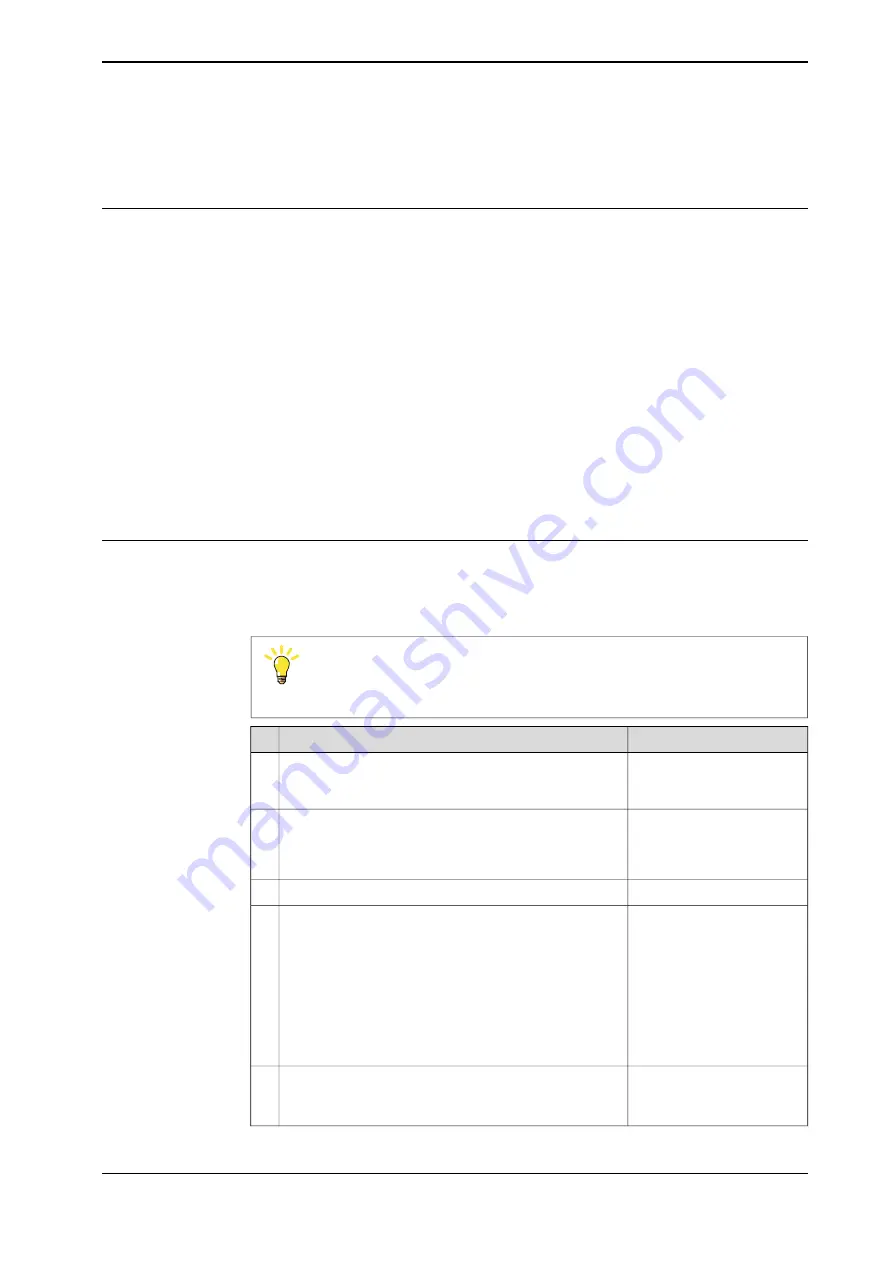
•
The system is in manual mode.
Note that LoadIdentify cannot be used for
tool0
.
Prerequisites for payloads
Before running the LoadIdentify service routine for a payload, make sure that:
•
The tool and payload are correctly mounted.
•
Axis 6 is close to horizontal.
•
The tool load is known (run LoadIdentify for the tool first).
•
The upper arm load is defined, if the payload mass is to be identified.
•
When using a moving TCP, the tool must be calibrated (TCP).
•
When using a stationary TCP, the corresponding work object must be
calibrated (user frame and object frame).
•
The axes 3, 5, and 6 are not close to their corresponding working range limits.
•
The speed is set to 100%.
•
The system is in manual mode.
Note that LoadIdentify cannot be used for
load0
.
Running LoadIdentify
To start the load identification service routine you must have an active program in
manual mode and the tool and payload that you want to identify must be defined
and active in the
Jogging
window.
Tip
Always run load identification with cold motors (no warm-up).
Information
Action
How to start service routines
is described in
Start LoadIdentify from the
Program Editor
. Press the
three-position enabling device and then press the
Start
button on the FlexPendant.
1
Tap
Cancel
and then
Cancel
Call Rout
to quit the service
routine without loosing the
program pointer.
Tap
OK
to confirm that current path will be cleared and
that the program pointer will be lost.
2
Tap
Tool
or
Payload
.
3
If it is not correct, release the
three-position enabling
device and select the correct
tool/payload in the
Jogging
menu. Then return to Load-
Identify, press the three-pos-
ition enabling device, and
press Start. Tap
Retry
and
confirm that the new
tool/payload is correct.
Tap
OK
to confirm that the correct tool and/or payload
is active in the jogging menu and that the tool load/pay-
load is correctly mounted.
4
See
When identifying tool loads, confirm that the tool is active.
5
When identifying payloads, confirm that the payload’s
tool is active and calibrated.
Continues on next page
Operating manual - IRC5 with FlexPendant
227
3HAC050941-001 Revision: G
© Copyright 2018 ABB. All rights reserved.
5 Programming and testing
5.9.5 LoadIdentify, load identification service routine
Continued
Содержание IRC5 with FlexPendant
Страница 1: ...ROBOTICS Operating manual IRC5 with FlexPendant ...
Страница 2: ...Trace back information Workspace R18 2 version a9 Checked in 2018 10 09 Skribenta version 5 3 008 ...
Страница 14: ...This page is intentionally left blank ...
Страница 120: ...This page is intentionally left blank ...
Страница 146: ...This page is intentionally left blank ...
Страница 240: ...This page is intentionally left blank ...
Страница 286: ...This page is intentionally left blank ...
Страница 294: ...This page is intentionally left blank ...
Страница 298: ...This page is intentionally left blank ...
Страница 304: ......
Страница 305: ......