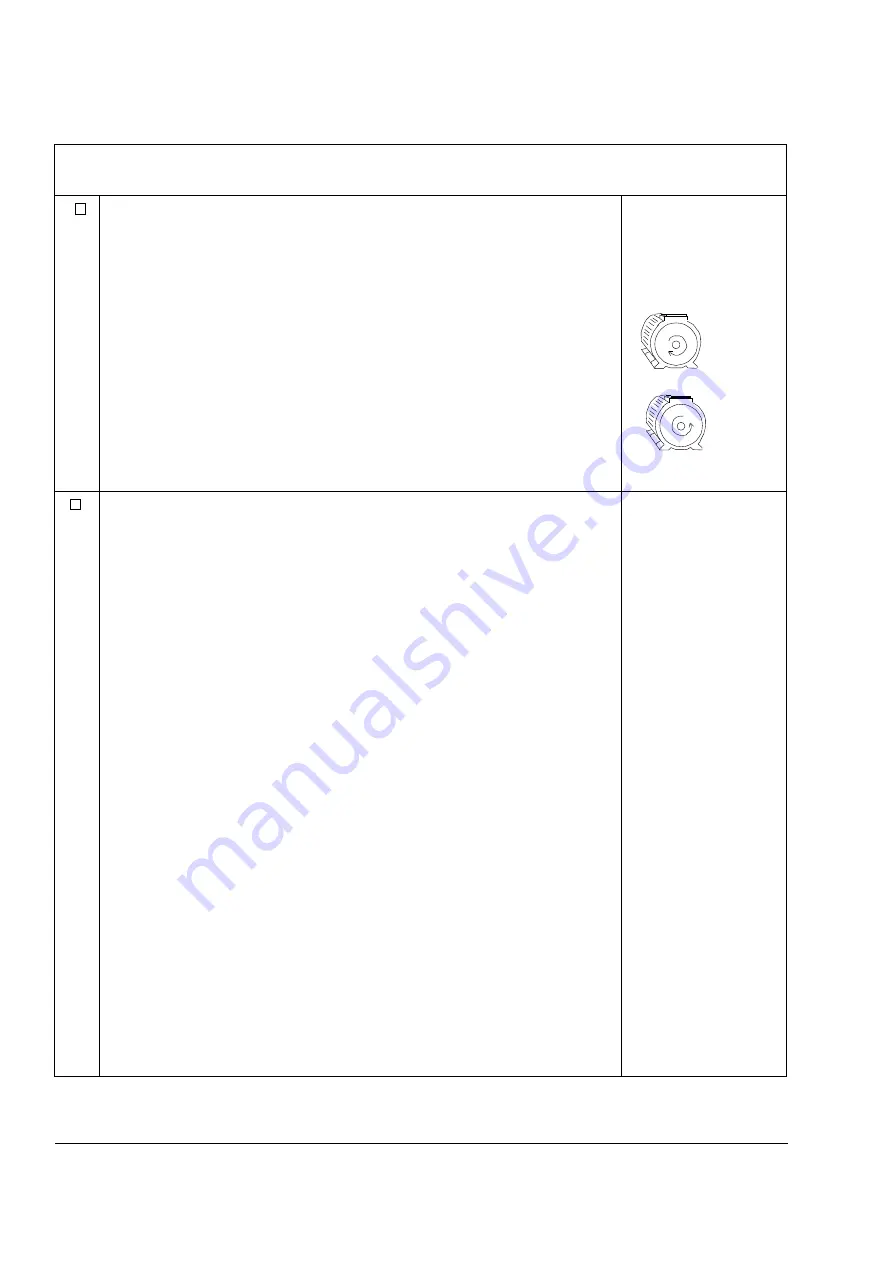
Start-up
20
Note:
Ensure that possible Safe Torque Off and emergency stop circuits are closed during the ID
run.
Check the direction of rotation of the motor before starting the ID run.
During the run (Normal or Reduced), the motor will rotate in the
forward direction.
Select the motor identification method by parameter
. During the Motor ID run, the drive will identify the
characteristics of the motor for optimum motor control. The ID run is
performed at the next start of the drive.
Note:
The motor shaft must NOT be locked and the load torque must be < 10% during
Normal or Reduced ID run. With permanent magnet motor this restriction applies also
when Standstill ID run is selected.
Note:
Mechanical brake (if present) is not opened during the ID run.
Note:
The ID run cannot be performed if par.
NORMAL ID run should be selected whenever possible.
Note:
The driven machinery must be de-coupled from the motor with Normal ID run if
• the load torque is higher than 20%, or
• the machinery is not able to withstand the nominal torque transient during the ID run.
The REDUCED ID run should be selected instead of the Normal ID
run if the mechanical losses are higher than 20%, i.e. the motor
cannot be de-coupled from the driven equipment, or full flux is
required to keep the motor brake open (conical motor).
The STANDSTILL ID run should be selected only if the Normal or
Reduced ID run is not possible due to the restrictions caused by the
connected mechanics (e.g. with lift or crane applications).
AUTOPHASING can only be selected after the Normal/Reduced/
Standstill ID run has been performed once. Autophasing is used when
an absolute encoder has been added/changed to a permanent
magnet motor, but there is no need to perform the Normal/Reduced/
Standstill ID run again. See parameter
on page
for information on autophasing modes, and section
.
forward
direction
reverse
direction
When drive output
phases U2, V2 and
W2 are connected to
the corresponding
motor terminals:
Содержание ACSM1 Series
Страница 1: ...ACSM1 Firmware Manual ACSM1 Speed and Torque Control Program...
Страница 2: ......
Страница 4: ......
Страница 12: ...Table of contents 12...
Страница 49: ...Drive control and features 49...
Страница 282: ...Standard function blocks 282...
Страница 306: ...Application program template 306...
Страница 312: ...Control chain block diagrams 312...
Страница 331: ...331...
Страница 332: ...332...
Страница 333: ......