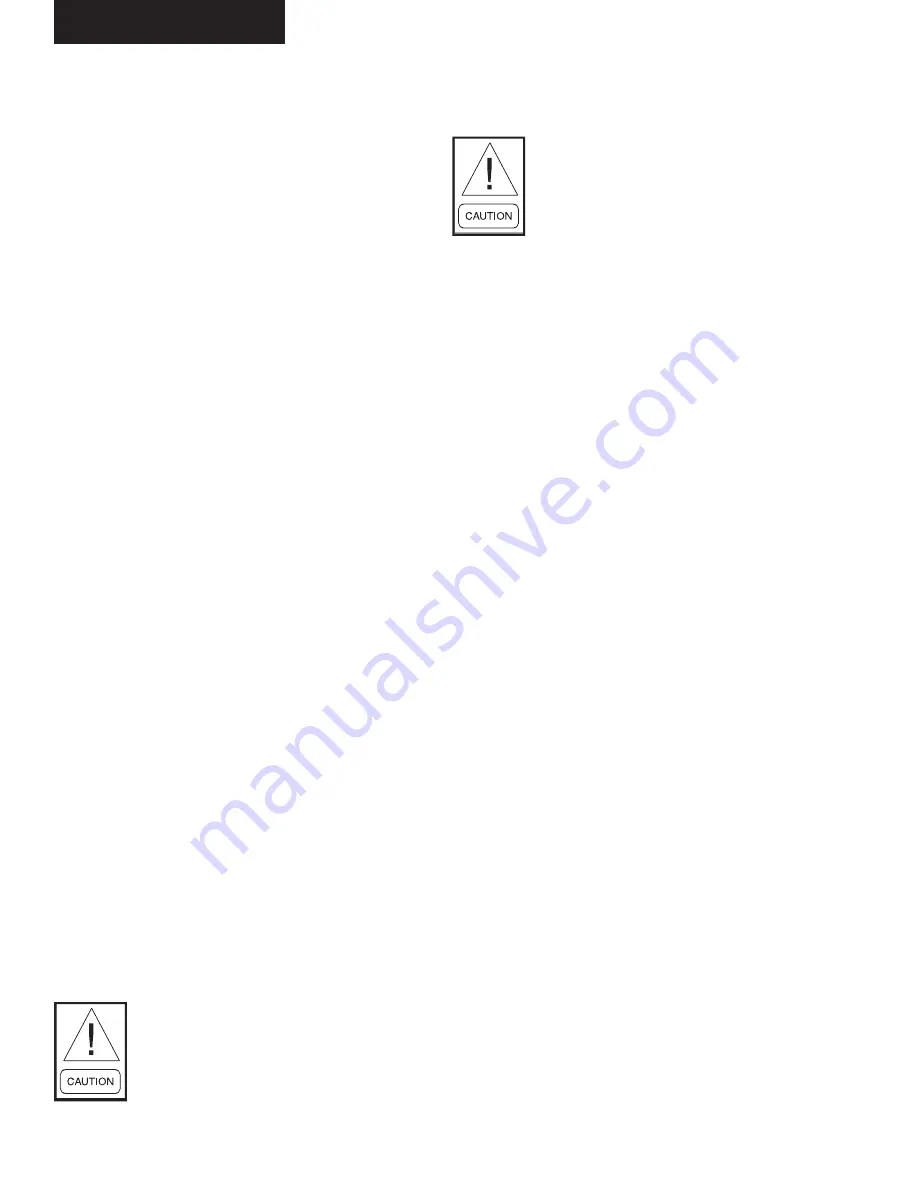
40
JOHNSON CONTROLS
FORM 145.05-NOM2 (807)
VAV Fan Operation
Two minutes after the unit is placed in the
“ON MODE”
the control will close a contact at DO-2 terminals 3 and
4 on the controller. The closure of this contact energizes
the RSF1 relay. The RSF1-1 contact closes and makes
a circuit between terminals 10 and 13 of the VFD. This
is the start command to the VFD. The RSF1-2 relay
contact also closes and energizes the MSF1 contactor
which closes and supplies line voltage to the VFD.
The control derives a
“Calc Duct Stati”
based on the
duct static sensor input 1 at IN-3 terminals 5 and 6 and
duct static sensor input 2 at IN-4 terminals 7 and 8 of the
control and the selected
“Static Value”
(High, Avg, or
Low). The control then compares the
“Calc Duct Stati”
to the
“Fan- S/A Pres SP”
and generates an analog 0
to 10 volt output from AO-3 - terminals 5 and 6 of the
control to the VFD. The control varies this 0 to 10 volt
output to maintain the
“Fan- S/A Pres SP”.
The unit has an airfl ow switch to verify blower operation.
If the switch is not closed within two minutes from the
time the blower binary output is energized the control
will initiate a
“Fan Failure Alarm”
. The Air Flow
Switch input enters the control at the IN7 – terminals
13 and 14.
When the binary output to the supply fan closes, the
control will close contact DO-5 – terminals 9 and 10.
This contact can be connected to an external device that
can be used to identify supply fan operation.
When the control receives the close signal from the
airflow switch, the control waits ten seconds and
switches from the
“START MODE”
to the
“ON
MODE”
. Cooling and heating operation cannot occur
until the unit is in the
“ON MODE”.
If the unit is equipped with a VFD, an optional VFD by-
pass package can also be purchased. With the switch in
the AUTO position, the VFD will function as indicated
above. If the switch is placed in the
“BY-PASS”
position
the blower will function in a constant volume mode
and the supply fan will be energized anytime power is
applied to the unit.
When the unit is placed in the “BY-
PASS” mode, the VFD is by-passed
and there is no static pressure con-
trol. If the VAV boxes are closed, the
ductwork could be damaged.
The third position is
“VFD”
. In this mode, the supply
fan motor can be operated through the VFD keypad.
When the unit is placed in the “VFD”
mode, the VFD is controlled by hand
and there is no static pressure con-
trol. If the VAV boxes are closed, the
ductwork could be damaged.
Communicated VFD Speed Input
If two or more units supply air to the same supply duct
or under fl oor space in a VAV or FlexSys system it may
be desirable to monitor one of the systems output to its
VFD and then send this same signal to the other units.
This allows all the units to operate the VFD at the same
speed. Otherwise if the units start at different times the
fi rst unit will ramp up and maintain the duct static but
the second unit will operate at minimum speed.
In order to use this feature
“Fan Sp BAS En”
must be
turned ON using the
“Setpoints”
section of the Keypad
/ Display or by a communicated input. The BACnet
object name is VFD Sp by BAS En and is instance
number BV15013.
The speed input would be communicated to the other
Unit Controllers through BACnet object name VFD Sp
% By BAS and instance number AI16024.
If this feature is desired, the unit must be ordered
from the factory with the feature programmed into the
control.
FLEXSYS DEW POINT CONTROL
The unit can be confi gured to use Dew Point Control in
both economizer and mechanical cooling mode. This
feature will prevent the supply air temperature dewpoint
entering the under fl oor space from falling above the
Slab Temperature of the under fl oor space.
The following parameters must be programmed through
the
“Setpoints”
section of the Keypad / Display or by
a communicated input.
“AC-S/A DEW EN”
– This value must be turned on in
order to use Dew Point Control. The default value is
ON
“AC-S/A DEW MIN”
– This establishes the minimum
allowable derived Dew Point Control set point. The
default value is 48.0° F.
Sequence of Operation
Summary of Contents for YSCD
Page 10: ...10 JOHNSON CONTROLS FORM 145 05 NOM2 807 THIS PAGE INTENTIONALLY LEFT BLANK ...
Page 12: ...12 JOHNSON CONTROLS FORM 145 05 NOM2 807 THIS PAGE INTENTIONALLY LEFT BLANK ...
Page 38: ...38 JOHNSON CONTROLS FORM 145 05 NOM2 807 THIS PAGE INTENTIONALLY LEFT BLANK ...
Page 46: ...46 JOHNSON CONTROLS FORM 145 05 NOM2 807 THIS PAGE INTENTIONALLY LEFT BLANK ...
Page 105: ...105 JOHNSON CONTROLS FORM 145 05 NOM2 807 LD13009 8 FIG 11 WIRING DIAGRAM POWER CIRCUIT ...