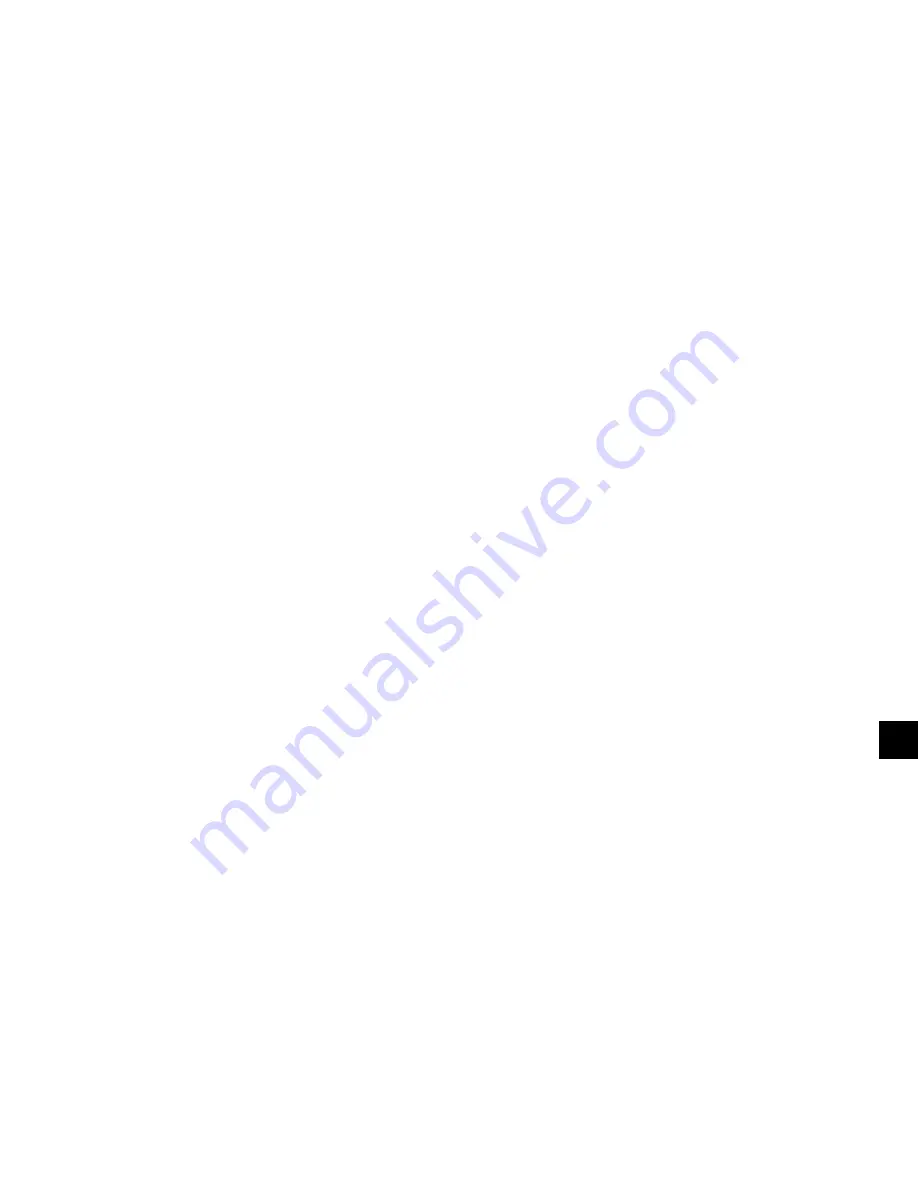
JOHNSON CONTROLS
139
Form 150.63-NM9
Issue date: 5/20/2021
8
Capacity control
To initiate the start sequence of the unit, all run permis-
sive inputs must be satisfied (air proving/remote start/
stop switch), and no unit or system faults exist.
The first phase of the start sequence is initiated by the
Daily Schedule Start or a Remote Cycling Device. If
the unit is shut down on the daily schedule, the evapo-
rator blower contacts (Terminals 23 and 24 of TB1)
will close when the daily schedule start time has been
reached. Once the air proving switch closes, capacity
control functions are initiated.
If unit cycling is accomplished with a remote cycling
device wired in series with the air proving switch, the
evaporator contacts will always be energized as long
as the unit switch is turned ON. When the air proving
switch and remote cycling contacts are closed, the ca-
pacity control functions will be initiated.
It should be noted that the evaporator contacts (Termi-
nals 23 and 24 of TB1) are not required to be used to
cycle the evaporator blower. However, in all cases the
air proving switch must be closed to allow unit opera-
tion.
The control system will evaluate the need for cooling
by comparing the actual discharge air temperature or
suction pressure(s) to the desired setpoint, and regu-
late the discharge air temperature or suction pressure
to meet that desired setpoint.
Suction pressure limit controls
The anticipatory controls are intended to prevent the
unit from ever actually reaching a low-pressure cut-
out. Loading is prevented, if the suction pressure drops
below 1.15 x suction pressure cutout (15% below the
cutout). Loading may reoccur after suction pressure
rises above the unload point and a period of one min-
ute elapses. This control is only operable if the optional
suction pressure transducers are installed.
Discharge pressure limit controls
The discharge pressure limit controls unload a system
before it reaches a safety limit due to high load or dirty
condenser coils. The microboard monitors discharge
pressure and unloads a system, if fully loaded, by one
compressor when discharge pressure exceeds the pro-
grammed cutout minus 10 psig (0.69 barg). Reloading
will occur when the discharge pressure on the affected
system drops to 85% of the unload pressure and 10
minutes have elapsed.
This control is only applicable if optional discharge
pressure transducers are installed.
Discharge air temperature control
The setpoint in Discharge Air Temperature Control
is the temperature the condensing unit will control to
within plus or minus the control range. The setpoint
High Limit is the Setpoint plus the Cooling Range. The
Setpoint Low Limit is the Setpoint minus the Cooling
If the Discharge Air Temperature is above the Setpoint
High Limit, the lead compressor on the lead system
will be energized along with the liquid line solenoid.
Upon energizing any compressor, the 60 second Anti-
Coincidence timer will be initiated.
If after 180 seconds of run time the discharge air tem-
perature is still above the Setpoint High Limit, the next
compressor in sequence will be energized. Additional
loading stages are energized at a rate of once every 180
seconds if the discharge air temperature remains above
the Setpoint High Limit.
If the discharge air temperature falls below the Set-
point High Limit but is greater than the Setpoint Low
Limit, loading and unloading do not occur. This area of
control is called the control range.
If the discharge air temperature drops below the Set-
point Low Limit, unloading occurs at a rate of 60 sec-
onds.
The sequences of Capacity Control (compressor staging)
for loading and unloading are shown in
Section 8 – Unit operation
Summary of Contents for YCUL0020
Page 4: ...JOHNSON CONTROLS 4 Form 150 63 NM9 Issue date 5 20 2021 THIS PAGE IS INTENTIONALLY LEFT BLANK...
Page 10: ...JOHNSON CONTROLS 10 Form 150 63 NM9 Issue date 5 20 2021 THIS PAGE IS INTENTIONALLY LEFT BLANK...
Page 14: ...JOHNSON CONTROLS 14 Form 150 63 NM9 Issue date 5 20 2021 THIS PAGE IS INTENTIONALLY LEFT BLANK...
Page 40: ...JOHNSON CONTROLS 40 Form 150 63 NM9 Issue date 5 20 2021 THIS PAGE IS INTENTIONALLY LEFT BLANK...
Page 53: ...JOHNSON CONTROLS 53 Section 5 Technical data Form 150 63 NM9 Issue date 5 20 2021 5...
Page 55: ...JOHNSON CONTROLS 55 Section 5 Technical data Form 150 63 NM9 Issue date 5 20 2021 5...
Page 57: ...JOHNSON CONTROLS 57 Section 5 Technical data Form 150 63 NM9 Issue date 5 20 2021 5...
Page 59: ...JOHNSON CONTROLS 59 Section 5 Technical data Form 150 63 NM9 Issue date 5 20 2021 5...
Page 61: ...JOHNSON CONTROLS 61 Section 5 Technical data Form 150 63 NM9 Issue date 5 20 2021 5...
Page 63: ...JOHNSON CONTROLS 63 Section 5 Technical data Form 150 63 NM9 Issue date 5 20 2021 5...
Page 65: ...JOHNSON CONTROLS 65 Section 5 Technical data Form 150 63 NM9 Issue date 5 20 2021 5...
Page 67: ...JOHNSON CONTROLS 67 Section 5 Technical data Form 150 63 NM9 Issue date 5 20 2021 5...
Page 69: ...JOHNSON CONTROLS 69 Section 5 Technical data Form 150 63 NM9 Issue date 5 20 2021 5...
Page 71: ...JOHNSON CONTROLS 71 Section 5 Technical data Form 150 63 NM9 Issue date 5 20 2021 5...
Page 73: ...JOHNSON CONTROLS 73 Section 5 Technical data Form 150 63 NM9 Issue date 5 20 2021 5...
Page 75: ...JOHNSON CONTROLS 75 Section 5 Technical data Form 150 63 NM9 Issue date 5 20 2021 5...
Page 77: ...JOHNSON CONTROLS 77 Section 5 Technical data Form 150 63 NM9 Issue date 5 20 2021 5...
Page 79: ...JOHNSON CONTROLS 79 Section 5 Technical data Form 150 63 NM9 Issue date 5 20 2021 5...
Page 81: ...JOHNSON CONTROLS 81 Section 5 Technical data Form 150 63 NM9 Issue date 5 20 2021 5...
Page 83: ...JOHNSON CONTROLS 83 Section 5 Technical data Form 150 63 NM9 Issue date 5 20 2021 5...
Page 85: ...JOHNSON CONTROLS 85 Section 5 Technical data Form 150 63 NM9 Issue date 5 20 2021 5...
Page 87: ...JOHNSON CONTROLS 87 Section 5 Technical data Form 150 63 NM9 Issue date 5 20 2021 5...
Page 177: ...JOHNSON CONTROLS 177 Form 150 63 NM9 Issue date 5 20 2021 Notes...