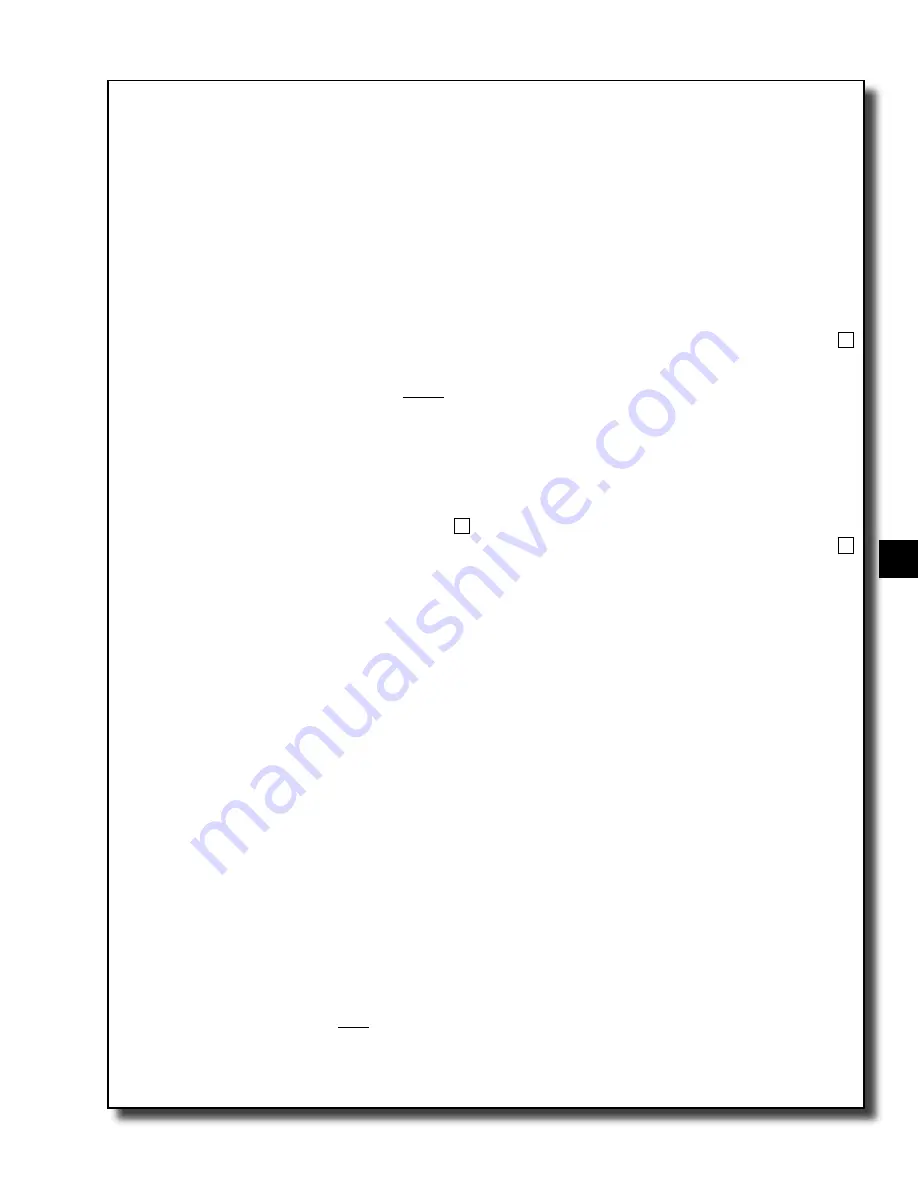
JOHNSON CONTROLS
107
SECTION 6 – COMMISSIONING
Form 150.63-NM9
Issue date: 5/20/2021
6
FORM 150.63-CL2
ISSUE DATE: 03/12/2019
5000 Renaissance Drive, New Freedom, Pennsylvania USA 17349
1-800-524-1330
Subject to change without notice. Printed in USA
Copyright © by Johnson Controls 2019
www.johnsoncontrols.com
ALL RIGHTS RESERVED
Form 150.63-CL2 (319)
Issue Date: March 12, 2019
Supersedes: 150.63-CL2 (1013)
D. CHECKING SUPERHEAT AND SUBCOOLING
The subcooling temperature of each system can
be calculated by recording the temperature of the
liquid line at the outlet of the condenser and sub-
tracting it from the liquid line saturation tempera-
ture at the liquid stop valve (liquid line saturation
temp. is converted from a temperature/pressure chart).
Example:
Liquid line pressure =
202 PSIG converted to temp.
_
102°F
minus liquid line temp.
______
- 84°F
Subcooling =
____________
18°F
The subcooling should be adjusted to 18°F at design condi-
tions.
1. Record the liquid line pressure and its correspond-
ing temperature, liquid line temperature, and
subcooling below: ....................................................
SYS 1 SYS 2
Liq Line Press = _______ _______ PSIG
Saturated Temp = _______ _______ °F
Liq Line Temp = _______ _______ °F
Subcooling = _______ _______ °F
After the subcooling is verified, the suction superheat
should be checked. The superheat should be checked
only after steady state operation of the condensing
unit has been established, the leaving water tempera-
ture has been pulled down to the required leaving wa-
ter temperature, and the unit is running in a fully loaded
condition. Correct superheat setting for a system is 10°F
to 15°F (5.56°C to 8.33°C) 18” (46 cm) from the cooler.
Superheat should typically be set for no less than
10°F with only a single compressor running on a
circuit.
The superheat is calculated as the difference
between the actual temperature of the returned refrig-
erant gas in the suction line entering the compressor
and the temperature corresponding to the suction pres-
sure as shown in a standard pressure/temperature chart.
Example:
Suction Temp = 46°F
minus Suction Press
60 PSIG converted to Temp - 34°F
Superheat = 12°F
When adjusting the expansion valve (TXV only), the
adjusting screw should be turned not more than one
turn at a time, allowing sufficient time (approximately
15 minutes) between adjustments for the system and
the thermal expansion valve to respond and stabilize.
Ensure that superheat is set at a minimum of 10°F
(5.56°C) with a single compressor running on each circuit.
2. Record the suction temperature, suction pressure,
suction saturation temperature, and superheat of
each system below: ................................................
SYS 1 SYS 2
Suction Temp = _______ _______ °F
Suction Pressure = _______ _______ PSIG
Saturation Temp = _______ _______ °F
Superheat = _______ _______ °F
E. LEAK CHECKING
Leak check compressors, fittings, and piping to en
-
sure no leaks. ..............................................................
If the unit is functioning satisfactorily during the ini-
tial operating period, no safeties trip and the com-
pressors cycle to control water temperature to
setpoint, the chiller is ready to be placed into operation.
Owner's operating personnel:
Name:
___________________________________________________
Phone Number:
__________________________________________
Name:
___________________________________________________
Phone Number:
__________________________________________
Name:
___________________________________________________
Phone Number:
__________________________________________
Summary of Contents for YCUL0020
Page 4: ...JOHNSON CONTROLS 4 Form 150 63 NM9 Issue date 5 20 2021 THIS PAGE IS INTENTIONALLY LEFT BLANK...
Page 10: ...JOHNSON CONTROLS 10 Form 150 63 NM9 Issue date 5 20 2021 THIS PAGE IS INTENTIONALLY LEFT BLANK...
Page 14: ...JOHNSON CONTROLS 14 Form 150 63 NM9 Issue date 5 20 2021 THIS PAGE IS INTENTIONALLY LEFT BLANK...
Page 40: ...JOHNSON CONTROLS 40 Form 150 63 NM9 Issue date 5 20 2021 THIS PAGE IS INTENTIONALLY LEFT BLANK...
Page 53: ...JOHNSON CONTROLS 53 Section 5 Technical data Form 150 63 NM9 Issue date 5 20 2021 5...
Page 55: ...JOHNSON CONTROLS 55 Section 5 Technical data Form 150 63 NM9 Issue date 5 20 2021 5...
Page 57: ...JOHNSON CONTROLS 57 Section 5 Technical data Form 150 63 NM9 Issue date 5 20 2021 5...
Page 59: ...JOHNSON CONTROLS 59 Section 5 Technical data Form 150 63 NM9 Issue date 5 20 2021 5...
Page 61: ...JOHNSON CONTROLS 61 Section 5 Technical data Form 150 63 NM9 Issue date 5 20 2021 5...
Page 63: ...JOHNSON CONTROLS 63 Section 5 Technical data Form 150 63 NM9 Issue date 5 20 2021 5...
Page 65: ...JOHNSON CONTROLS 65 Section 5 Technical data Form 150 63 NM9 Issue date 5 20 2021 5...
Page 67: ...JOHNSON CONTROLS 67 Section 5 Technical data Form 150 63 NM9 Issue date 5 20 2021 5...
Page 69: ...JOHNSON CONTROLS 69 Section 5 Technical data Form 150 63 NM9 Issue date 5 20 2021 5...
Page 71: ...JOHNSON CONTROLS 71 Section 5 Technical data Form 150 63 NM9 Issue date 5 20 2021 5...
Page 73: ...JOHNSON CONTROLS 73 Section 5 Technical data Form 150 63 NM9 Issue date 5 20 2021 5...
Page 75: ...JOHNSON CONTROLS 75 Section 5 Technical data Form 150 63 NM9 Issue date 5 20 2021 5...
Page 77: ...JOHNSON CONTROLS 77 Section 5 Technical data Form 150 63 NM9 Issue date 5 20 2021 5...
Page 79: ...JOHNSON CONTROLS 79 Section 5 Technical data Form 150 63 NM9 Issue date 5 20 2021 5...
Page 81: ...JOHNSON CONTROLS 81 Section 5 Technical data Form 150 63 NM9 Issue date 5 20 2021 5...
Page 83: ...JOHNSON CONTROLS 83 Section 5 Technical data Form 150 63 NM9 Issue date 5 20 2021 5...
Page 85: ...JOHNSON CONTROLS 85 Section 5 Technical data Form 150 63 NM9 Issue date 5 20 2021 5...
Page 87: ...JOHNSON CONTROLS 87 Section 5 Technical data Form 150 63 NM9 Issue date 5 20 2021 5...
Page 177: ...JOHNSON CONTROLS 177 Form 150 63 NM9 Issue date 5 20 2021 Notes...