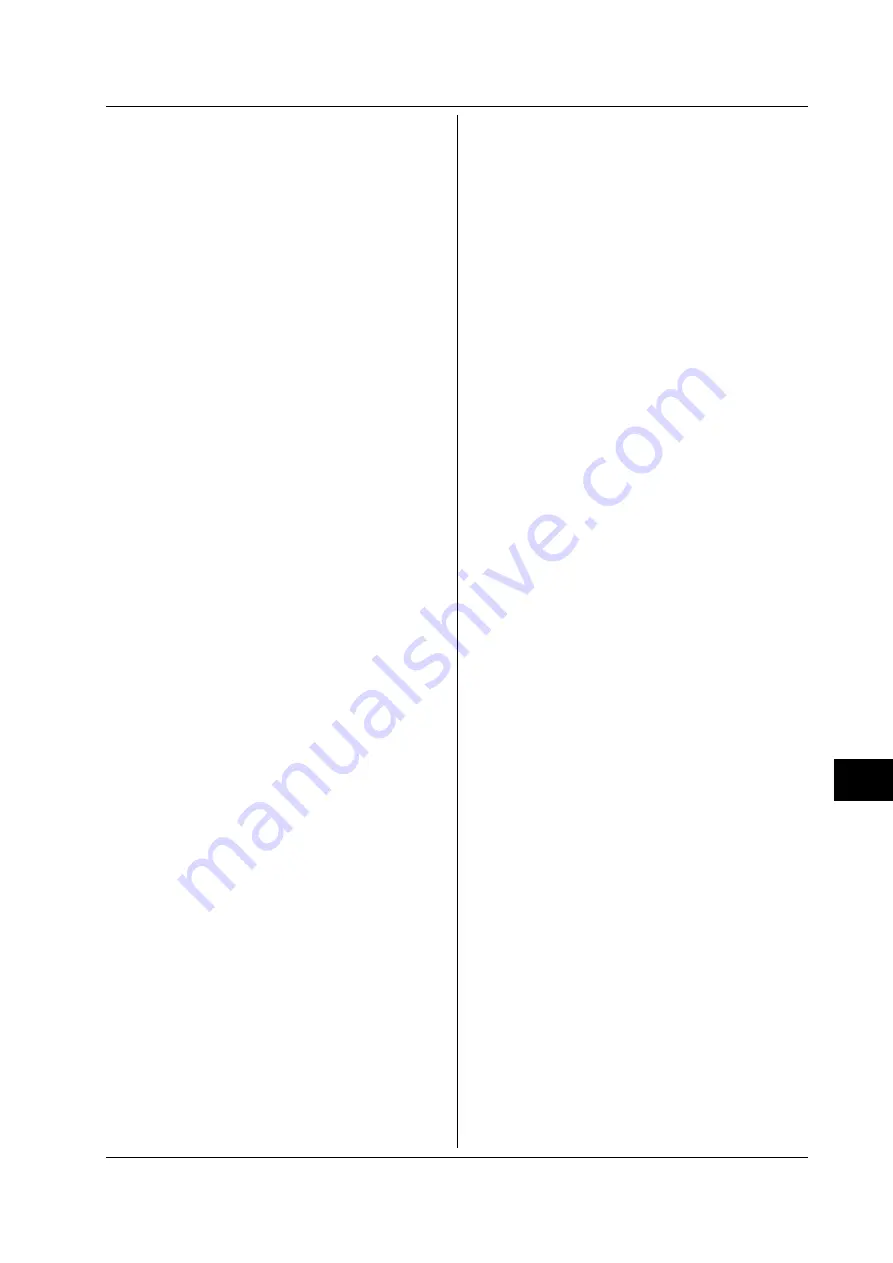
10-21
IM 755601-01E
Communication
Commands
10
:LIMit:PCNT?
Function
Queries all settings when the limit mode is set
to deviation mode (%).
Syntax
:LIMit:PCNT?
Example
:LIMIT:PCNT?
→
:LIMIT:PCNT:
REFERENCE 1.0000E+05;PLIMIT 9.99;DATA
5.00, —5.00
:LIMit:PCNT[:DATA]
Function
Sets the limit values (deviation (%)) or queries
the current setting.
Syntax
:LIMit:PCNT[:DATA] {<NRf(HI)>[,<NRf(LO)>]}
:LIMit:PCNT:DATA?
When the “
:LIMit:PCNT:PLIMit
” is set to
9.99
<NRf> = —9.99 to 9.99% (Resolution 0.01%)
When the “
:LIMit:PCNT:PLIMit
” is set to
99.9
<NRf> = —99.9 to 99.9% (Resolution 0.1%)
Response
<NR2>, <NR2> (Outputs in the order HI
and LO.)
Example
:LIMIT:PCNT:DATA —5,5
:LIMIT:PCNT:DATA?
→
:LIMIT:PCNT:DATA
5.00,—5.00
Description • The range and resolution of the limit values vary
depending on the “
:LIMit:PCNT:PLIMit
” setting.
• If the LO parameter is omitted, the value
equal to (0 – HI) is set to LO.
• If HI is less than LO, an error (815) occurs.
• When the “
:LIMit[:MODE]
” is set to OHM,
the “
:LIMit:PCNT[:DATA]
” setting cannot be
changed or queried. Doing so will result in
an error (813).
:LIMit:PCNT:PLIMit
Function
Sets the percent limit when the limit mode is set
to deviation (%) or queries the current setting.
Syntax
:LIMit:PCNT:PLIMit {<NRf>}
:LIMit:PCNT:PLIMit?
<NRf> = 9.99 or 99.9
Response
{9.99|99.90}(<NR2> form)
Example
:LIMIT:PCNT:PLIMit 9.99
:LIMIT:PCNT:PLIMIT?
→
:LIMIT:PCNT:PLIMIT
9.99
Description • When the “
:LIMit:PCNT:PLIMit
” is changed,
the following settings are also automatically
changed.
When the percent limit is changed from
9.99 to 99.9
Limit values HI = 0.0%, LO = 0.0%
(
:LIMit:PCNT[:DATA]
)
When the percent limit is changed from
99.9 to 9.99
Limit values HI = 0.00%, LO = 0.00%
(
:LIMit:PCNT[:DATA]
)
• When the “
:LIMit[:MODE]
” is set to OHM,
the “
:LIMit:PCNT:PLIMit
” setting cannot be
changed or queried. Doing so will result in
an error (813).
:LIMit:PCNT:REFerence
Function
Sets the reference value when the limit mode is
set to deviation (%) or queries the current
setting.
Syntax
:LIMit:PCNT:REFerence {<Resistance>}
:LIMit:PCNT:REFerence?
<Resistance> = 0.0000
Ω
to 120.00 M
Ω
Response
<NR3> form
Example
:LIMIT:PCNT:REFERENCE 100KOHM
:LIMIT:PCNT:REFERENCE?
→
:LIMIT:PCNT:
REFERENCE 1.0000E+05
Description • The measurement range is determined by
the “
:LIMit:PCNT:REFerence
” setting.
• When the “
:LIMit[:MODE]
” is set to OHM,
the “
:LIMit:PCNT:REFerence
” setting cannot
be changed or queried. Doing so will result
in an error (813).
10.2 Commands