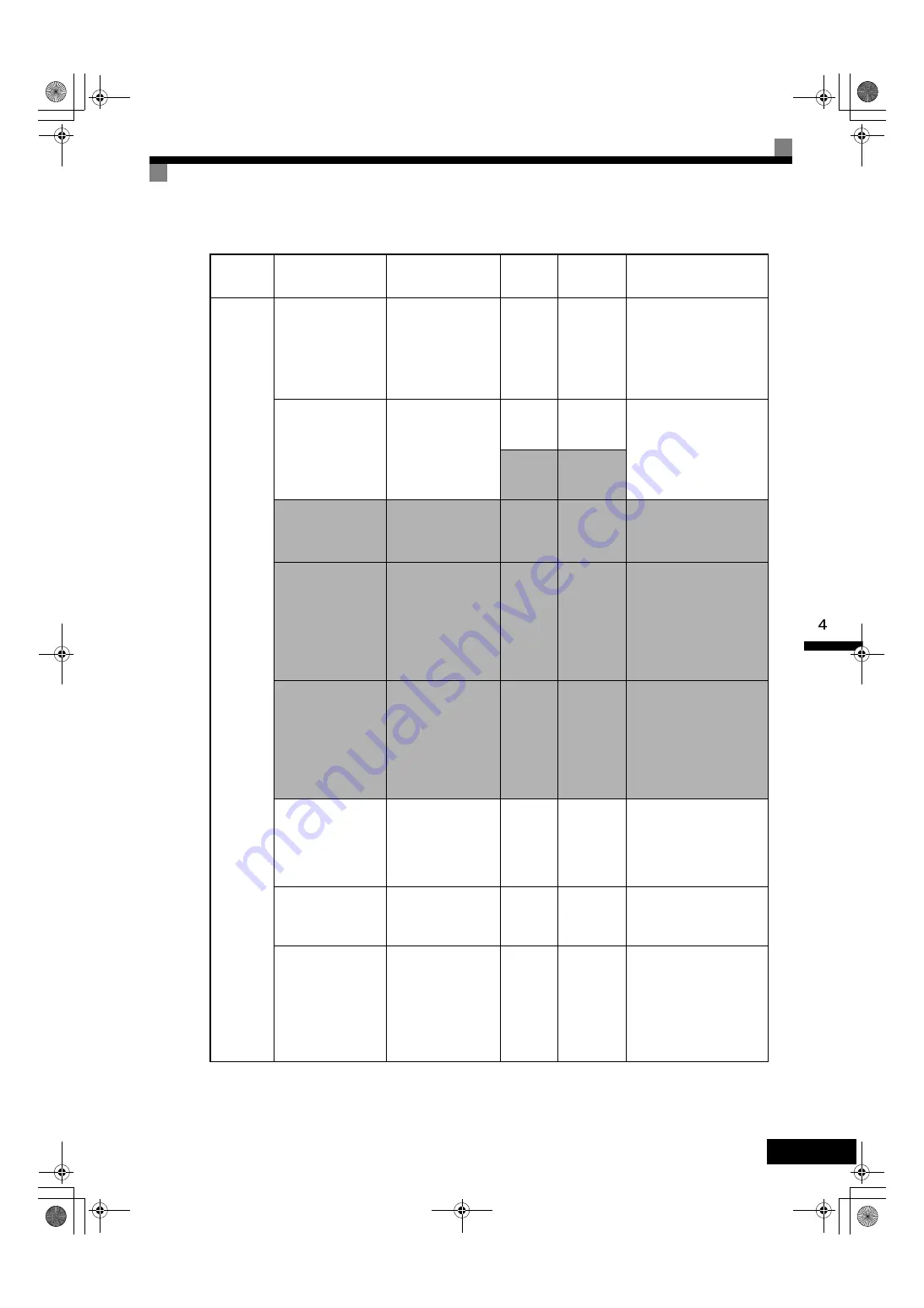
Adjustment Suggestions
4-
31
Open-loop
vector 2
control
(A1-02 = 4)
(Continued)
ASR switching
frequency (C5-07)
Switching the ASR
proportional gain and
integral time accord-
ing to the output fre-
quency
0.0 Hz
0.0 to max.
output fre-
quency
Set the output frequency at
which to change the ASR
proportional gain and inte-
gral time when the same val-
ues cannot be used for both
high-speed and low-speed
operation.
ASR primary delay
time (C5-06)
Controlling hunting
and vibration
0.010 s
0.04 to
0.020 s
(Enabled in the range 0 to
35 Hz.)
Increase the setting if
machine rigidity is low and
the system vibrates easily.
*2
0.035 s
0.010 to
0.035 s
ASR primary delay
time 2 (C5-10)
Controlling hunting
and vibration
0.010 s
0.010 to
0.035 s
(Enabled above the 35 Hz.)
Increase the setting if
machine rigidity is low and
the system vibrates easily.
*2
Integral time of speed
estimator (N4-07)
• Torque and speed
response
• Controlling hunting
and vibration
0.030 ms
0.015 to
0.060 ms
(Enabled below the N4-11
setting.)
• Reduce the setting if speed
response is slow.
*2
(Typi-
cally, reduce in intervals of
0.005.)
• Increase the setting if hunt-
ing or vibration occurs.
High-speed propor-
tional gain of speed
estimator (N4-10)
• Torque and speed
response
• Controlling hunting
and vibration
15
10 to 60
(Enabled above the N4-11
setting.)
• Increase the setting if
speed response is slow.
*2
(Typically, increase in
intervals of 5.)
• Reduce the setting if hunt-
ing or vibration occurs.
Carrier frequency
selection (C6-11)
• Reducing motor
magnetic noise
• Controlling hunting
and vibration at low
speeds (3 Hz or less)
1
*6
Default
value
• Increase the setting if
motor magnetic noise is
high.
• Reduce the setting if hunt-
ing or vibration occurs at
low speeds.
Mode selection for
zero-speed (b1-10)
*5
Improving CF fault
detection around zero-
speed during speed
control
0
Depends on
machine
characteris-
tics.
Set b1-10 to 1 to move in the
same direction as the sign of
the speed reference value.
Rotation direction
limit operation
selection (d5-07)
*5
Improving CF fault
detection around zero-
speed during torque
control
1
Depends on
machine
characteris-
tics.
• Confirm that the d5-07 is
set to 1 to move in the
same direction as the sign
of the speed limit value.
• Start the motor with speed
control and change to
torque control after reach-
ing 3 Hz or higher.
Table 4.3 Adjusted User Constants (Continued)
Control
Method
Name (Constant
Number)
Performance
Factory
Setting
Recom-
mended
Setting
Adjustment Method
TOE-S616-60.1.book 31 ページ 2017年8月4日 金曜日 午後3時41分