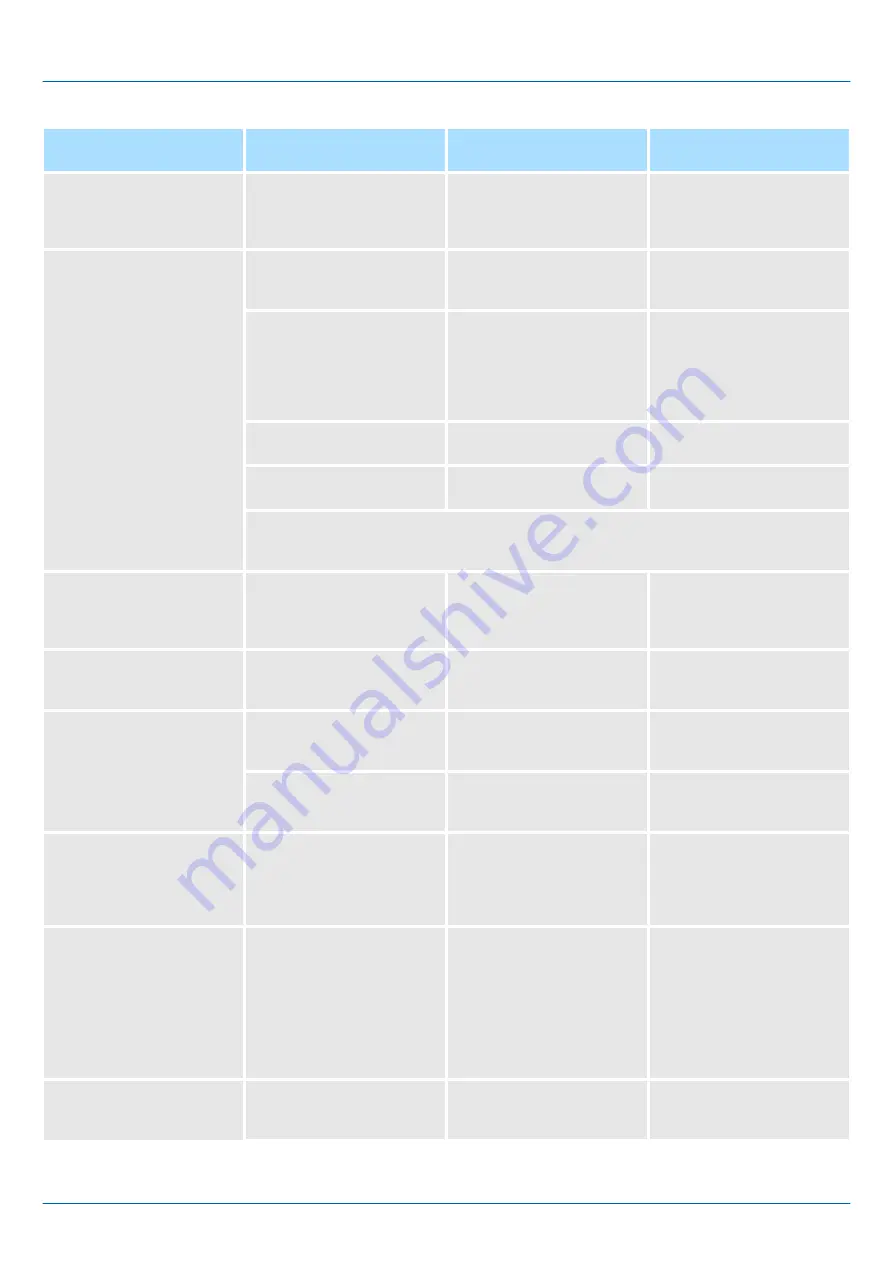
Alarm Number: Alarm
Name (Alarm Description)
Cause
Investigative Actions
Corrective Actions
A.830: Encoder Battery
Alarm
The battery voltage was
lower than the specified
level after the control power
supply was turned ON.
Measure the battery voltage. Replace the battery.
A.840:Encoder Data Alarm
An encoder fault occurred
Turn the power supply OFF
and then ON again.
If the alarm still occurs, the
servomotor may be faulty.
Replace the servomotor.
Malfunction of encoder
because of noise interfer-
ence, etc.
-
Correct the wiring around
the encoder by separating
the encoder cable from the
servomotor main circuit
cable or by checking the
grounding and other wiring.
Wiring incorrect or one
signal is missing.
-
Recheck the wiring.
Noise
-
Connect shield properly as
recommended.
Note: If the scale file is configured for Hall sensor connectivity, a Hall sensor must be con-
nected. Disabling Hall sensor connectivity (Pn080.0 = 1) and trying to work without the
sensor will cause error A.840.
A.850: Encoder Overspeed
The encoder was operating
at high speed when the
power was turned ON.
Check the speed monitor
(Un000) to confirm the ser-
vomotor speed when the
power is turned ON
Reduce the servomotor
speed to a value less than
200 min
-1
, and turn ON the
control power supply.
A.860: Encoder Overheated The internal temperature of
the encoder is too high.
Measure the ambient oper-
ating temperature around
the servomotor.
The ambient operating tem-
perature of the servomotor
must be 40 °C or less.
A.C80: Encoder Clear Error
or Multiturn Limit Setting
Error
The multiturn data for the
absolute encoder was not
correctly cleared or set.
Turn the power supply OFF
and then ON again.
If the alarm still occurs, the
servomotor may be faulty.
Replace the servomotor
The absolute encoder reset
was not completed or not
supported.
Turn the power supply OFF
and then ON again.
If the alarm still occurs, the
SERVOPACK may be faulty.
Replace the SERVOPACK.
A.C90: Encoder Communi-
cations Error
Communications between
the encoder and SERVO-
PACK is not possible.
Check the encoder con-
nector contact status. Check
the encoder cable.
Re-insert the encoder con-
nector and confirm that the
encoder is correctly wired.
Use the encoder cable with
the specified rating.
A.C91: Encoder Communi-
cations Position Data Accel-
eration Rate Error
The noise interference
occurred on the input/output
signal line because the
encoder cable is bent and
the sheath is damaged.
The encoder cable is bun-
dled with a high-current line
or near a high-current line.
Check the encoder cable,
the connector and the
encoder cable layout.
Confirm that there is no
problem with the encoder
cable layout.
Confirm that there is no
surge voltage on the
encoder cable.
A.C92: Encoder Communi-
cations Timer Error
Noise interference occurred
on the input/output signal
line from the encoder.
Check the operating envi-
ronment.
Take countermeasures
against noise.
Sigma-5 and Sigma-7 Series SERVOPACKs
Error Lists
Errors in Semi-closed Loop Control with Rotary Motors
| | Feedback Option Module Type 3 - Manual version C - Revision 0 | en |
99