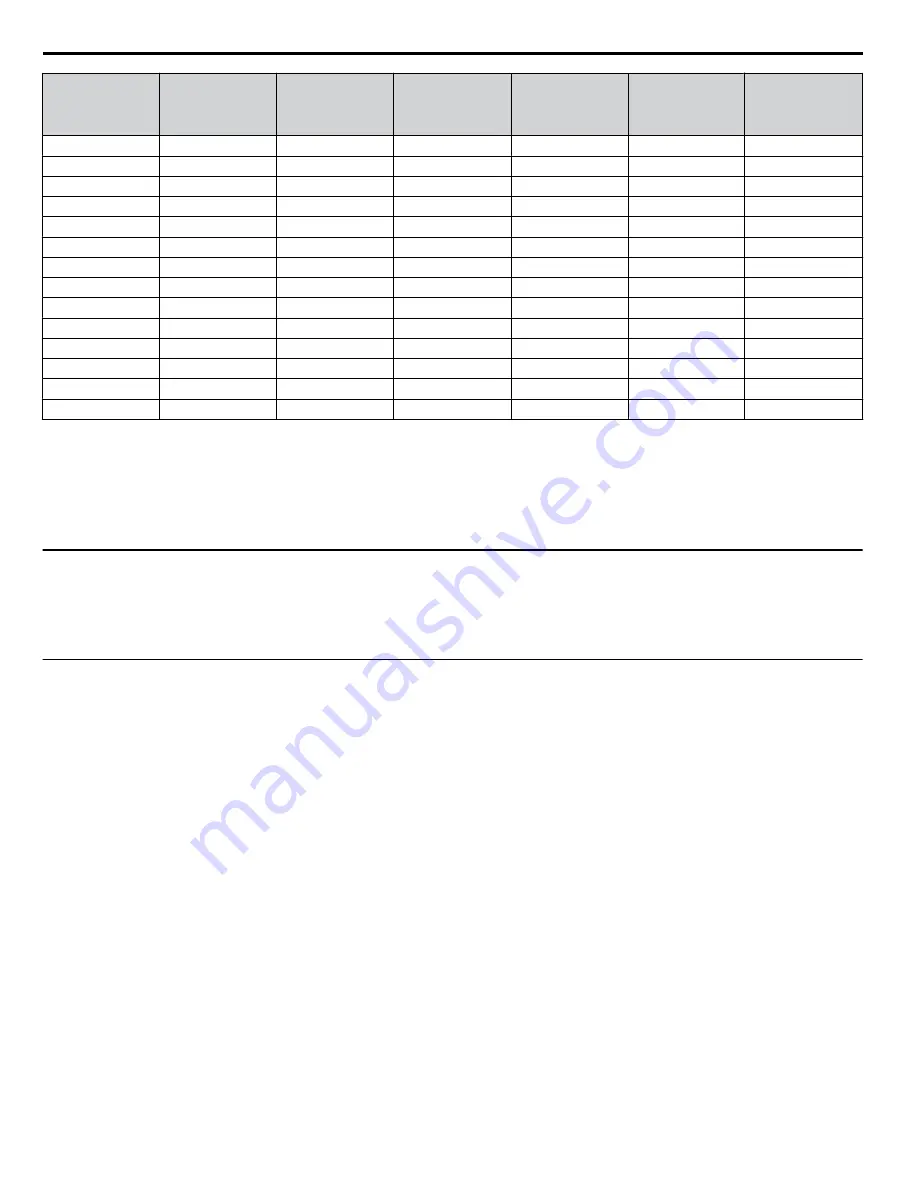
Drive Model
Nominal
Output Power
HP
AC Drive Input
Amps
MCCB Rating
Amps
Time Delay Fuse
Non-time Delay
Fuse Rating
Amps
Bussman Semi-
conductor Fuse
Rating (Fuse
5A0011
10
16
30
25
45
FWP-70B (70)
5A0017
15
23
40
40
60
FWP-100B (100)
5A0022
20
31
60
50
90
FWP-100B (100)
5A0027
25
38
75
60
110
FWP-125A (125)
5A0032
30
45
75
75
125
FWP-125A (125)
5A0041
40
44
75
75
125
FWP-175A (175)
5A0052
50
54
100
90
150
FWP-175A (175)
5A0062
60
66
125
110
175
FWP-250A (250)
5A0077
75
80
150
125
225
FWP-250A (250)
5A0099
100
108
175
175
300
FWP-250A (250)
5A0125
125
129
225
225
350
FWP-350A (350)
5A0145
150
158
300
275
450
FWP-350A (350)
5A0192
200
228
400
350
600
FWP-600A (600)
5A0242
250
263
500
450
700
FWP-600A (600)
<1> Maximum MCCB Rating is 15 A, or 200 % of drive input current rating, whichever is larger. MCCB voltage rating must be 600 VAC or greater.
<2> Maximum Time Delay fuse is 175% of drive input current rating. This covers any Class CC, J or T class fuse.
<3> Maximum Non-time Delay fuse is 300% of drive input current rating. This covers any CC, J or T class fuse.
<4> When using semiconductor fuses, Bussman FWH and FWP are required for UL compliance. Select FWH for 200 V Class and 400 V Class models
and FWP fuses for 600 V models.
<5> Class L fuse is also approved for this rating.
u
Attachment for External Heatsink Mounting (IP00 Enclosure)
An external attachment can be used to project the heatsink outside of an enclosure to ensure that there is sufficient air circulation
around the heatsink.
Contact a Yaskawa sales representative or Yaskawa directly for more information on this attachment.
u
Installing a Motor Thermal Overload (oL) Relay on the Drive Output
Motor thermal overload relays protect the motor by disconnecting power lines to the motor due to a motor overload condition.
Install a motor thermal overload relay between the drive and motor:
• When operating multiple motors on a single AC drive.
• When using a power line bypass to operate the motor directly from the power line.
It is not necessary to install a motor thermal overload relay when operating a single motor from a single AC drive. The AC
drive has UL recognized electronic motor overload protection built into the drive software.
Note:
1.
Disable the motor protection function (L1-01 = 0) when using an external motor thermal overload relay.
2.
Create a sequence to produce an external fault (coast to a stop) when triggered.
n
General Precautions when Using Thermal Overload Relays
Consider the following application precautions when using motor thermal overload relays on the output of AC drives to prevent
nuisance trips or overheat of the motor at low speeds:
• Low speed motor operation
• Use of multiple motors on a single AC drive
• Motor cable length
• Nuisance tripping resulting from high AC drive carrier frequency
Low Speed Operation and Motor Thermal oL Relays
Generally, thermal relays are applied on general-purpose motors. When general-purpose motors are driven by AC drives, the
motor current is approximately 5% to 10% greater than if driven by a commercial power supply. In addition, the cooling
capacity of a motor with a shaft-driven fan decreases when operating at low speeds. Motor overheating may occur even when
8.5 Installing Peripheral Devices
390
YASKAWA SIEP YAIP1U 01C AC Drive - P1000 Technical Manual