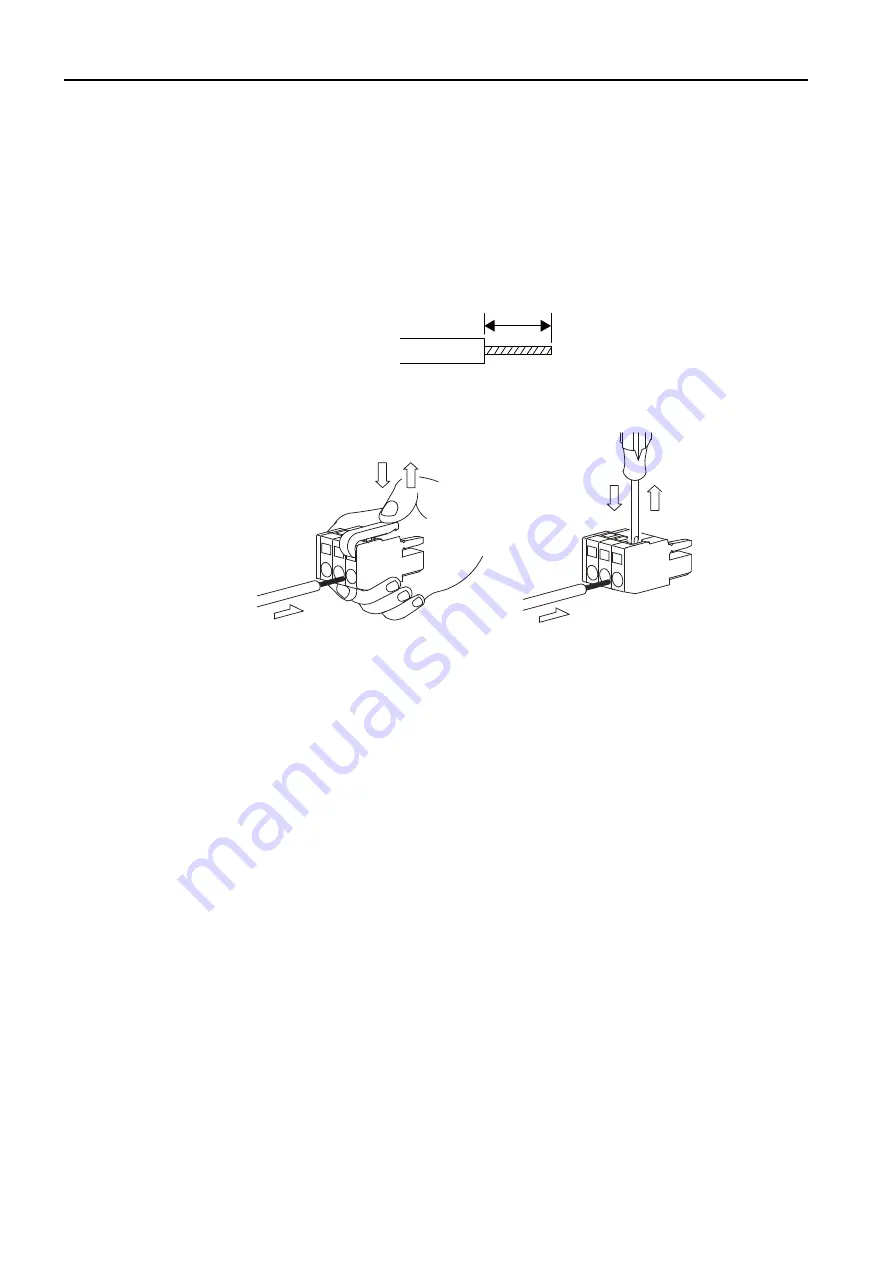
2.3 Connecting Devices
2.3.2 Connecting the Power Supply Connector
2-42
Procedure to Make a 100/200-VAC Power Cable
The power supply pins are contained in a removable connector. Use the following procedure to
wire the power supply connector. Use a twisted-pair cable with a wire size of AWG28 to
AWG13 (0.08 to 2.6 mm
2
) to connect the 100/200-VAC power supply to the power supply
connector on the Controller.
Use the following procedure to make the cable.
1.
Strip the wires.
Strip the wires for a length of 8 to 9 mm from the end to expose the conductors.
2.
Clamp the wires.
Insert the conductors into the back of the plug and clamp them securely.
8 to 9 mm