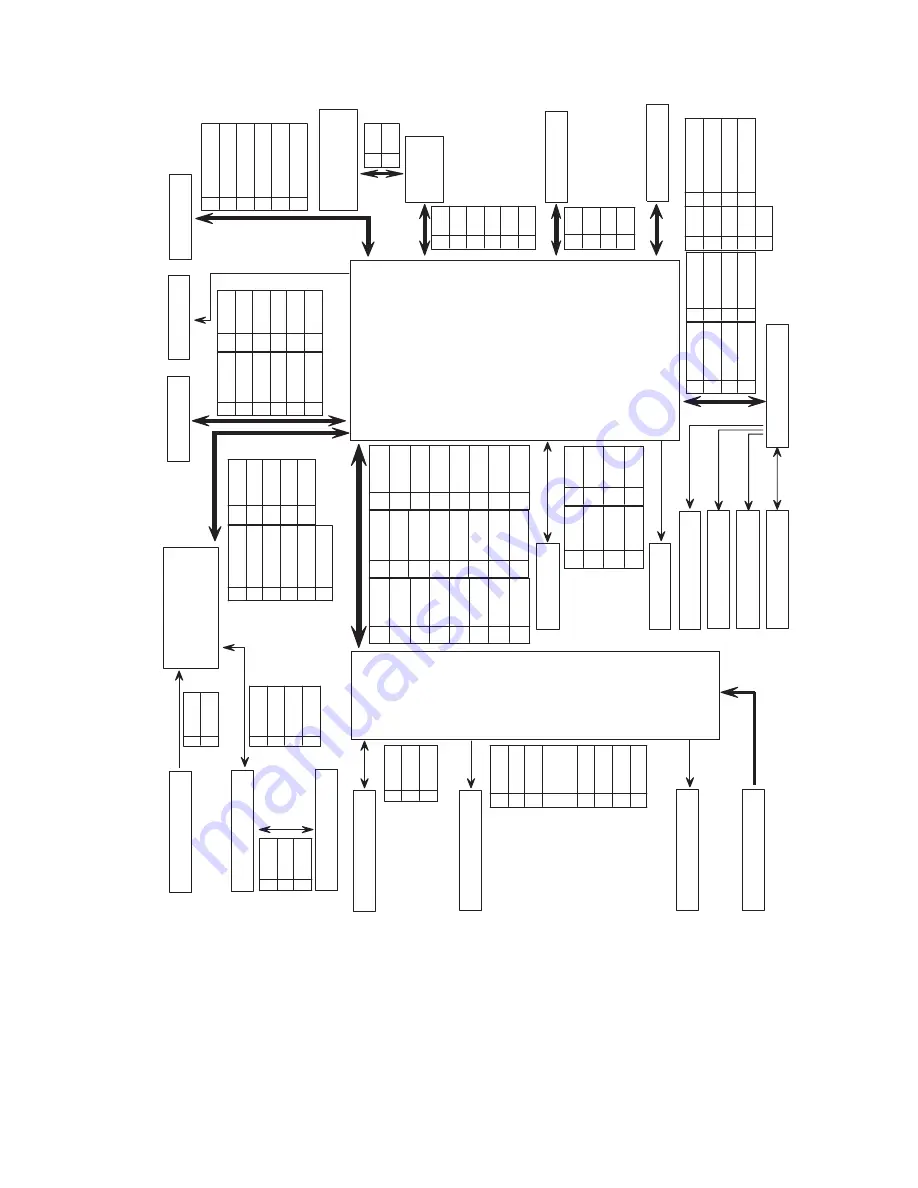
10-5
Connection Diagram
LASER
CO
VE
R
OP
EN
B’
D
PA
NEL
CO
VE
R
JO
IN
T
CO
NNE
CT
OR
B’
D
PT
L
MA
IN
-C
LU
TC
H
EXIT
M
OT
OR
LA
MP
RE
GI
-CLUT
CH
3P
2P
EXI
T
SEN
SO
R
1
VC
C
2
SI
GN
AL
3
GN
D
3P
PRINT CAR
TRIDGE
4P
1
MH
V
2
NC
3
NC
4
OP
C
GN
D
5
NC
6
SU
PP
LY
7
NC
8
DE
V
24
P
SE
NS
OR
B’
D
TH
ER
M
IS
TO
R
2P
1
TH
ER
M
1
2
TH
ER
M
2
1
GN
D
2
P_
REG
I
3
P_
EM
PT
Y
4
VC
C
4P
11
P
1
LS
UC
LK
2
LR
EA
DY
*
3
PM
OT
O
R*
4
GN
D
5
24
V
6
3.
3V
7
VD
O-
8
VD
O+
9
LD
_O
N*
10
GN
D
11
5V
S
12
nH
SY
NC
1
GN
D
2
CA
RT
_CL
K
3
CA
RT
_DA
TA
4
3.
3V
5
P_
EM
PT
Y
6
P_
REG
I
7
TH
ER
M
1
8
TH
ER
M
2
9
P_
SI
ZE
1
10
P_
SI
ZE
2
11
P_
SI
ZE
3
12
P
1
VC
C
2
3.
3V
3
PA
NEL
_T
X
4
PA
NE
L_
RX
5
PA
NE
L_
RE
SE
T
6
GN
D
6P
6P
1
24
V
2
24
V
3
24
VS
4
24
VS
5
GN
D
6
5V
S
2P
1
24
2
24
VS
MA
IN
MO
TO
R
4P
1
PA
_1
2
PA
_2
3
PB
_1
4
PB
_2
8P
1
24
VS
2
24
VS
3
GN
D
4
GN
D
5
GN
D
6
VC
C
7
nS
TA
RT
_S
TO
P
8
M
O
TO
R_
RE
ADY
9
M
O
TO
R_
CL
K
2P
1
24
VS
2
MA
IN
_C
LU
T
3
MP
_C
LU
T
4
RE
GI
_C
LUT
8P
5
MP
_E
M
PT
Y
6
3.
3V
7
PR
O_
M
F
8
GN
D
MP
-CLU
TC
H
RE
GI
SE
NS
OR
3P
1
VC
C
2
SI
GN
AL
3
GN
D
MP
-E
M
PT
Y
3P
2P
2P
3P
1
NC
2
24V
3
DE
V_
PW
M
4
24V
5
M
HV_
PW
M
6
24V
7
GN
D
8
GN
D
9
M
HV_
R
EAD
10
GN
D
11
TH
V_
READ
12
3.3
V
13
TH
V_
EN
14
3.3
V
15
TH
V_
PW
M
16
GN
D
17
24
VS
18
GN
D
19
VC
C
20
VC
C
21
NC
22
P_
EXI
T
23
P_
DU
PL
EX
24
FU
SER
1
3.
3V
2
SC
F_
ST
S
3
SC
F_
CM
D
4
SC
F_
CL
K
5
SC
F_
RDY
6
24
V
7
GN
D
8
GN
D
SC
F
8P
FA
N
3P
-
PRINT CARTRIDGE INTERCONNECT
BOARD
POWER SUPPLY BOARD
AC INPUT
MAIN BOARD
Summary of Contents for Phaser 3425
Page 1: ...Service Manual P h a s e r L a s e r P r i n t e r 3425 ...
Page 2: ......
Page 14: ...xii Phaser 3425 Laser Printer ...
Page 20: ...xviii Phaser 3425 Laser Printer ...
Page 29: ...General Information 1 9 Consumables 1 Print Cartridge 1 ...
Page 48: ...2 14 Phaser 3425 Laser Printer Service Manual ...
Page 93: ...6 Chapter Adjustments and Calibrations In this chapter Margin Calibration Resetting NVRAM ...
Page 98: ...7 4 Phaser 3425 Laser Printer Service Manual ...
Page 144: ...8 46 Phaser 3425 Laser Printer Service Manual ...
Page 145: ...9 Chapter Parts Lists In this chapter Using the Parts List Print Engine Parts Xerox Supplies ...
Page 175: ...10 6 Phaser 3425 Laser Printer Service Manual ...
Page 179: ......
Page 180: ......