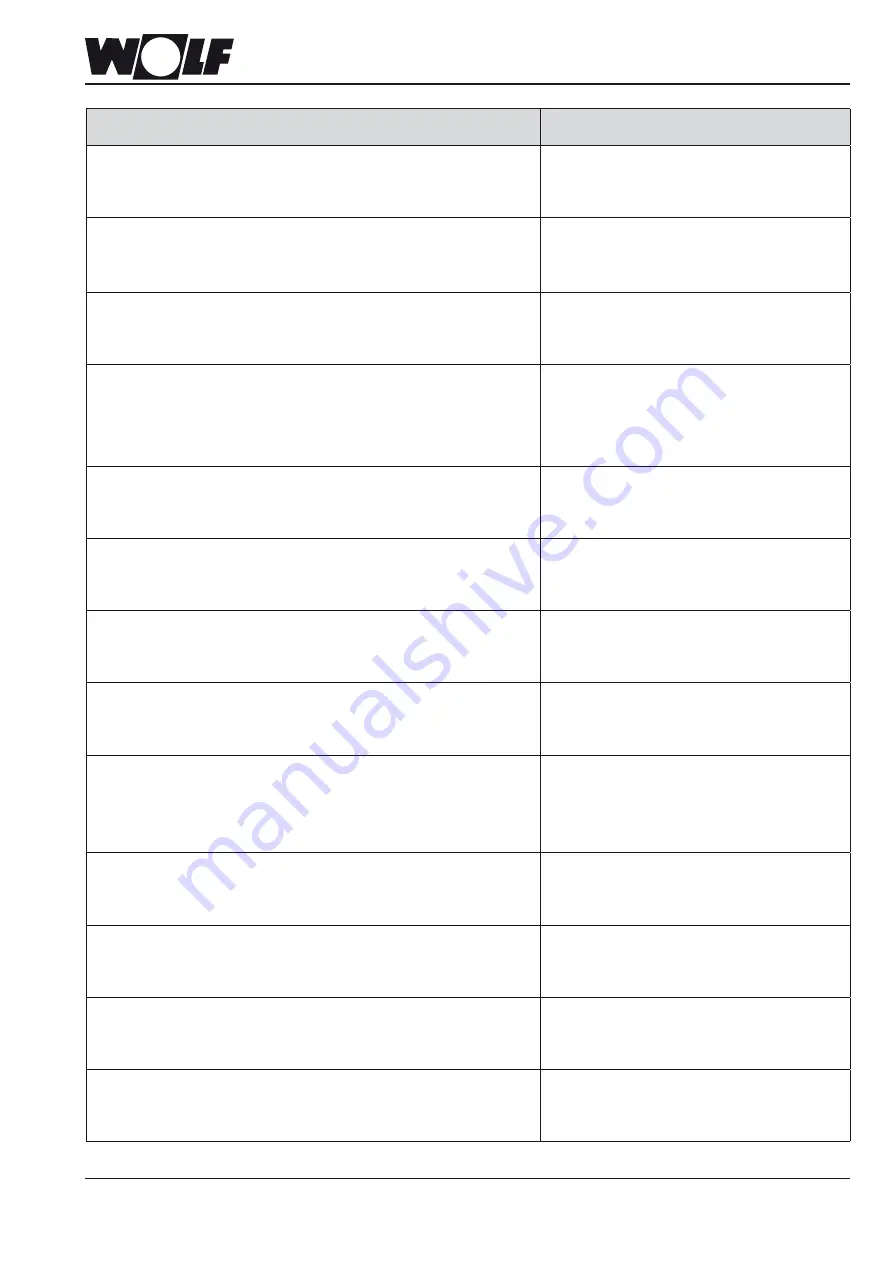
3064816_201804
67
34. Commissioning report
Commissioning steps
Test values or confirmation
1.) Serial number on the type plate
___________________________________
2.) Electrical wiring/connection/fuse protection checked in
accordance with specification from installation instructions
and VDE regulations?
□
2.) System flushed?
□
3.) System filled and water treatment carried out in accordance
with "Technical information, water treatment"?
pH value set
Total hardness set
□
________________ pH value
________________ °dH
4.) Appliance and system vented?
□
5.) System pressure 2.0 - 2.5 bar?
□
6.) Water connections checked for tightness?
□
7.) Trap filled?
□
8.) Gas valve set to gas type?
Natural gas
□
LPG
□
Wobbe index
_____________ kWh/m³
Net calorific value _____________ kWh/m³
9.) Gas supply pressure checked?
□
10.) Gas tightness test carried out?
□
11.) Switch heating appliance ON, set control unit to OFF/
Standby.
□
12.) Standard setting set on control unit?
□