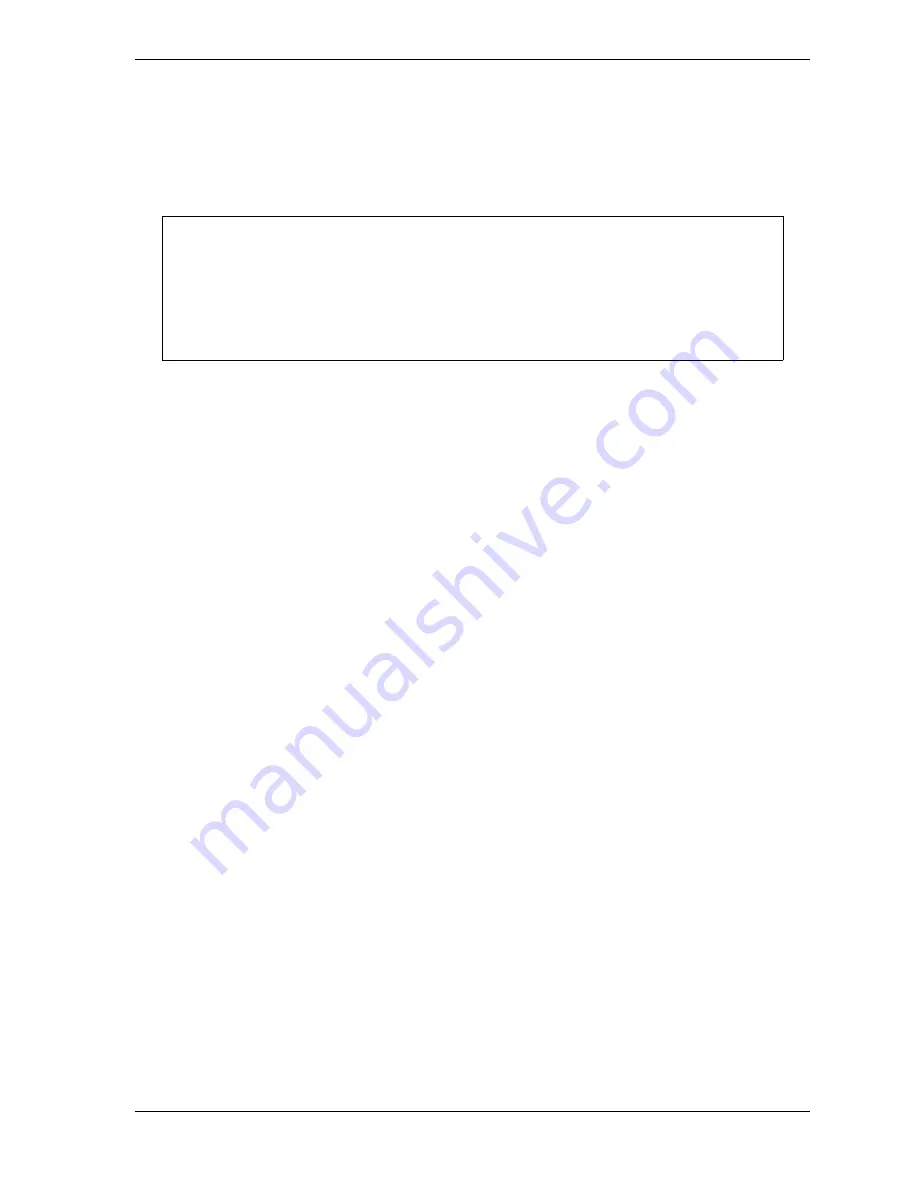
AutoSet User Manual
1137200
Operation
4-9
If you are operating in Single-stroke mode, start and cycle the press until the sample
period is completed and AutoSet displays new values in the Setpoints displays; then cycle
the press for a few additional strokes.
4.
If AutoSet stops the press after the new setpoints have been calculated, do the following:
a. Establish that the press stopped due to low setpoints by checking for malfunctions
such as a stuck part, load imbalance, misfeed, etc.
b. If the press stopped because setpoints were too low, turn the “% TOL” indicator dial
up to position 5 (i.e., 20%), and repeat steps 2 and 3.
c. If AutoSet stops the press again, turn the “% TOL” dial to the next higher setting, and
repeat steps 2 and 3. Repeat this step until the “% TOL” setting is high enough so that
AutoSet does not stop the press.
5.
If AutoSet does not stop the press after the new setpoints have been calculated, do the
following:
a. Turn the “% TOL” indicator dial down to position 3 (i.e., 10%), and repeat steps 2 and
b. If AutoSet stops the press, establish that the press stopped due to low setpoints,
referring to step 4a. If low setpoints are the cause of the press stopping, turn the “%
TOL” indicator dial back to its previous position. This is the correct setting for the
job.
c. If AutoSet does not stop the press, turn the “% TOL” indicator dial to the next lower
position, and repeat steps 2 and 3.
d. If AutoSet stops the press, repeat step 5b.
If AutoSet does not stop the press, repeat step 5c.
Determining the Correct High Tolerance and
Repeatability Settings (AutoSet Plus)
The purpose of this procedure is to determine the highest repeatability setpoint at which
AutoSet will not stop the press. The “% REP” indicator dial must be set high enough to avoid
nuisance stops, which occur when normal stroke-to-stroke tonnage variations cause AutoSet
to stop the press, but not so high that the press is vulnerable to repeatability overloads. Once
the correct repeatability setting is determined, the percent high tolerance can be set to a value
greater than the repeatability setting, typically about two times greater.
PRESS STOPPED DUE TO TONNAGE FAULT
If the press was stopped due to a tonnage fault rather than a nuisance stop (i.e., setpoints
that have been set too low), do not continue with this procedure until you have corrected
the problem. Otherwise, damage to the press and tooling may result.
Failure to comply with these instructions could result in property damage.
CAUTION
Summary of Contents for autoset 1500
Page 2: ......
Page 4: ......
Page 6: ......
Page 84: ...1137200 AutoSet User Manual 4 16 Operation ...
Page 96: ...1137200 AutoSet User Manual A 4 Wiring and Settings Tables ...
Page 102: ...1137200 AutoSet User Manual Wintriss Manuals ...