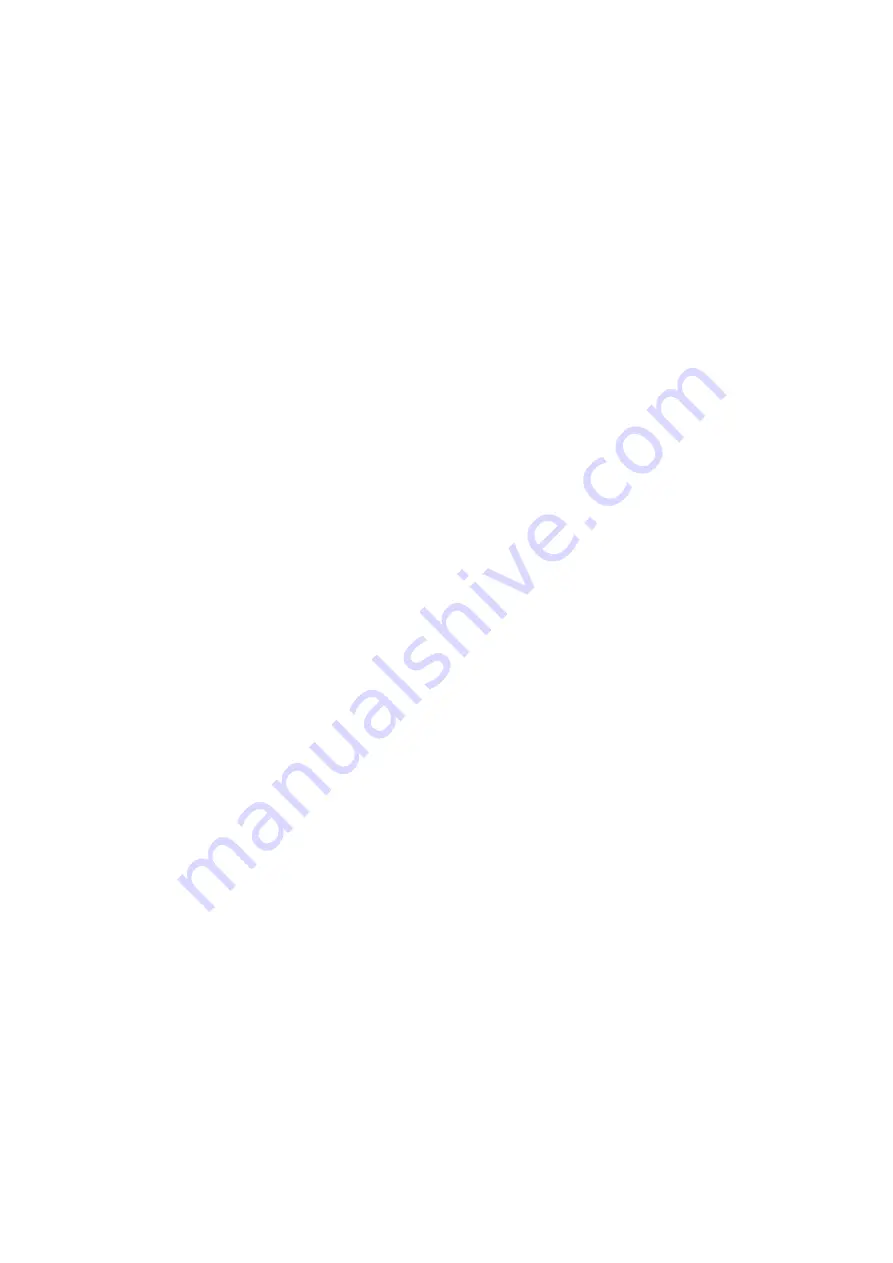
Installation and operating instructions Wilo-RexaBloc RE/Rexa BLOC 49
TROUBLESHOOTING AND POSSIBLE SOLUTIONS English
9.
Troubleshooting and possible solutions
In order to prevent damage or serious injury while rectifying
hydraulics faults, the following points must be observed:
•
Only attempt to remedy a fault if you have qualified
staff, meaning that each job must be carried out by
qualified personnel. Electrical work, for example, must be
performed by a trained electrician.
• Always secure the hydraulics against an accidental
restart by disconnecting the motor from the mains. Take
appropriate safety precautions.
• Always have a second person on hand to ensure the
hydraulics are switched off in an emergency.
• Secure moving parts to prevent injury.
• Unsanctioned changes to the hydraulics are made at the
operator’s own risk and release the manufacturer from
any warranty obligations!
Fault: The unit will not start
1. Tripping of fuses, motor protection switch and/or moni-
toring devices
• Check that the impeller runs freely. If necessary, clean
it and ensure it runs freely again
2. The sealing chamber monitoring (optional) has inter-
rupted the electric circuit (operator-related)
•
See fault: Mechanical seal leak, sealing chamber mon
-
itoring reports a fault or shuts down the unit
Fault: The unit starts, but the motor protection switch
triggers shortly after commissioning
1. Incorrect direction of rotation
•
Swap the 2 phases of the mains supply
2. Impeller slowed by accumulation, clogging and/or solid
matter, increased current consumption
• Switch off the hydraulics, secure them against being
switched back on again and free the impeller or clear
the suction port
3.
The density of the fluid is too high
• Contact Wilo customer service
Fault: The unit is running, but not pumping
1.
No fluid available
• Open inlet for tank or slide valve
2. Inlet clogged
• Clean the supply line, slide valve, suction piece, suc-
tion port or suction strainer
3. Impeller blocked or slowed
• Switch off the hydraulics, secure them against being
switched back on again and free the impeller
4. Defective piping
• Replace defective parts
5. Intermittent operation
• Check switching system
Fault: The unit is running, but not within the specified
operating parameters
1. Inlet clogged
• Clean the supply line, slide valve, suction piece, suc-
tion port or suction strainer
2. Slide valve closed in the discharge pipe
• Fully open the slide valve
3. Impeller blocked or slowed
• Switch off the hydraulics, secure them against being
switched back on again and free the impeller
4. Incorrect direction of rotation
•
Swap 2 phases of the mains supply
5. Air in the system
• Check the piping and hydraulics, and vent if necessary
6. Hydraulics pumping against excessive pressure
• Check the slide valve in the discharge pipe and open
it completely if necessary, use a different impeller,
consult the factory
7. Signs of wear
• Replace worn parts
8. Defective piping
• Replace defective parts
9.
Inadmissible levels of gas in the fluid
• Consult the factory
10. 2-phase operation
• Have a specialist inspect the connection and correct
it if necessary
Fault: The unit is not running smoothly and is noisy
1. Hydraulics are operating in an inadmissible range
• Check the operating data of the hydraulics and cor-
rect if necessary and/or adjust the operating condi-
tions
2. Suction port, suction strainer and/or impeller clogged
• Clean the suction port, suction strainer and/or impel-
ler
3. Impeller stiff
• Switch off the hydraulics, secure them against being
switched back on again and free the impeller
4.
Inadmissible levels of gas in the fluid
• Consult the factory
5. Incorrect direction of rotation
•
Swap 2 phases of the mains supply
6. Signs of wear
• Replace worn parts
7. Shaft bearing defective
• Consult the factory
8. Hydraulics are installed under tension
• Check installation, use rubber compensators if neces-
sary
Fault: Mechanical seal leak, sealing chamber monitoring
reports a fault or shuts down the unit
1. Condensation water build-up due to extended storage
and/or temperature fluctuations
•
Operate the hydraulics briefly (max. 5 min) without
pencil electrode
2. Increased leakage when running in new mechanical seals
• Change the oil
3. Defective pencil electrode cables
• Replace pencil electrode
4. Mechanical seal is defective
• Replace the mechanical seal and contact the factory!
Further steps for troubleshooting
If the points listed here do not rectify the fault, contact Wilo
customer service. They can help you as follows:
• Telephone and/or written support from Wilo customer
service
• On-site support from Wilo customer service
• Inspection or repair of the hydraulics at the factory
Please note that you may be charged for some services
provided by our customer service! For more details, please
contact the Wilo customer service.