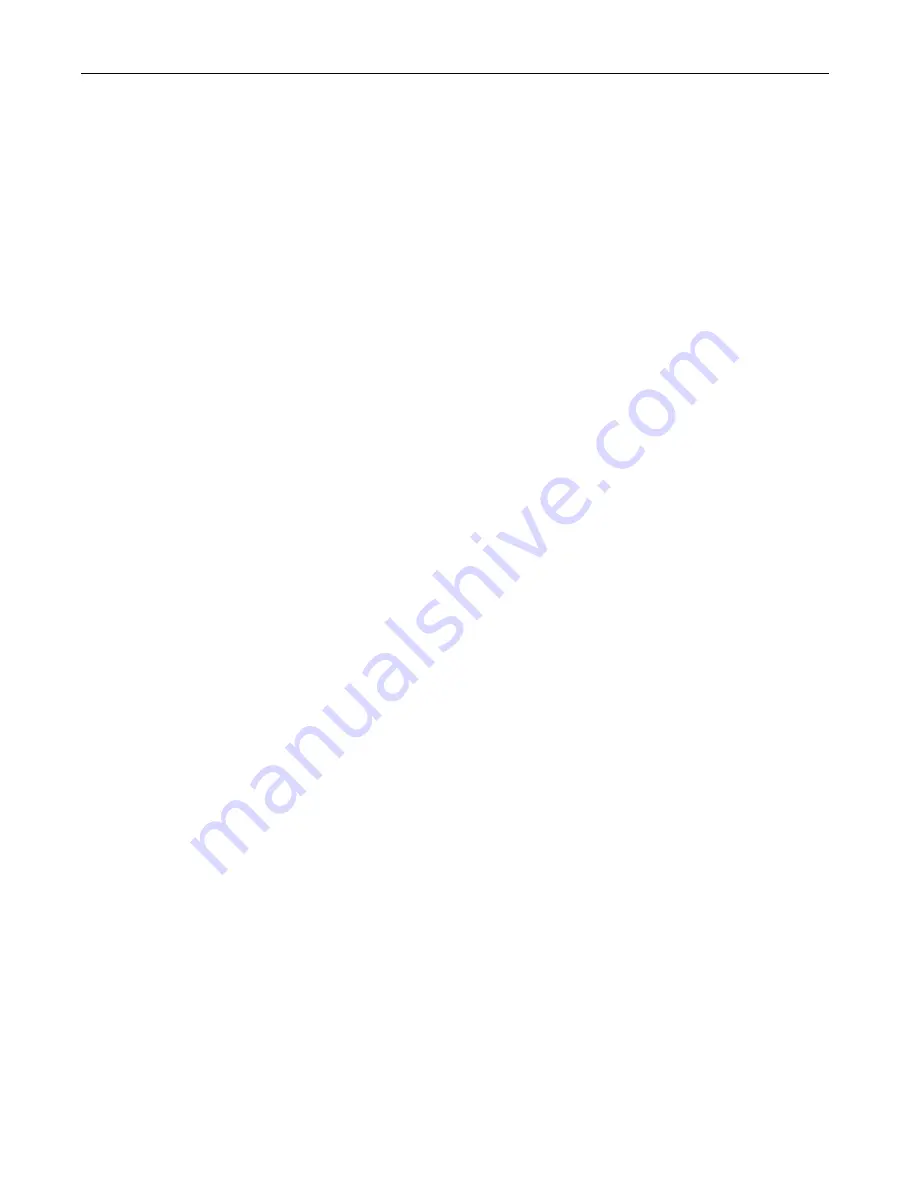
B E L 2 7 0 F
U L L Y
A
U T O M A T I C
H
O T
M
E L T
G
L U E
C
A S E
S
E A L E R
15
65-07-6 3/6/2007
T
ROUBLE
S
HOOTING
G
UIDE
S
ECTION
1 - C
ORRUGATED
C
ASE
Q
UALITY
& S
PECIFICATIONS
Corrugated case quality is a major factor in smooth running and quality sealing.
1.
Check your case dimensions
to see that the products fill the case efficiently and do not bulge, over-fill or
under-fill the case. Re-sizing of cases can often result in cost savings by using the correct box size and
material weight. Consult your corrugated supplier, for help to achieve this. A correctly filled box will help the
automatic process by supporting the case body during flap folding and the top flap sealing.
2.
Make sure that all scores (fold lines) on your cases are well defined
to help with the automatic folding
process. Your corrugated case supplier can help with this by making sure that correct scoring pressure is used
for your case specification.
This is one of the most common causes of poor case closing performance
3.
Corrugated case weakness
is often an area that needs quality control. The fluted construction of corrugated
board can be impaired by various factors in the corrugated box manufacturing process
.
Points to watch for:
a. that the flutes have not been crushed overall, causing the box to have a ‘soft’ and limp feeling. This
causes poor case rigidity during machining and also does not give your product the protection it
deserves.
b. selective bands of crushing, usually parallel to the box flutes that can cause failure lines down the box
and result in poor machine handling performance.
c. case storage, flat cases should be stored in dry conditions and on a flat surface. Be careful not to
stack excessive weight on to the cases as crushing can result.
4.
Check the ‘squareness’ of cases
. The glue joint where the manufacturer glues the flat case together often
can present a quality problem by being misaligned. It causes the case to be wider at one end than the other or
to be twisted from end to end. Both conditions can cause case jams and poor sealing quality.
5.
Corner
slots in the case should be wide as possible
so cases can be automatically folded with a minimum of
interference between major and minor flaps.
6.
Overlap or gapped case flaps
can be a result of incorrect flap lengths. Fold the box by hand to see that flaps
meet neatly in the case center.
Use your corrugated case supplier’s expertise to help you achieve the correct specifications for your automatic
sealing line.