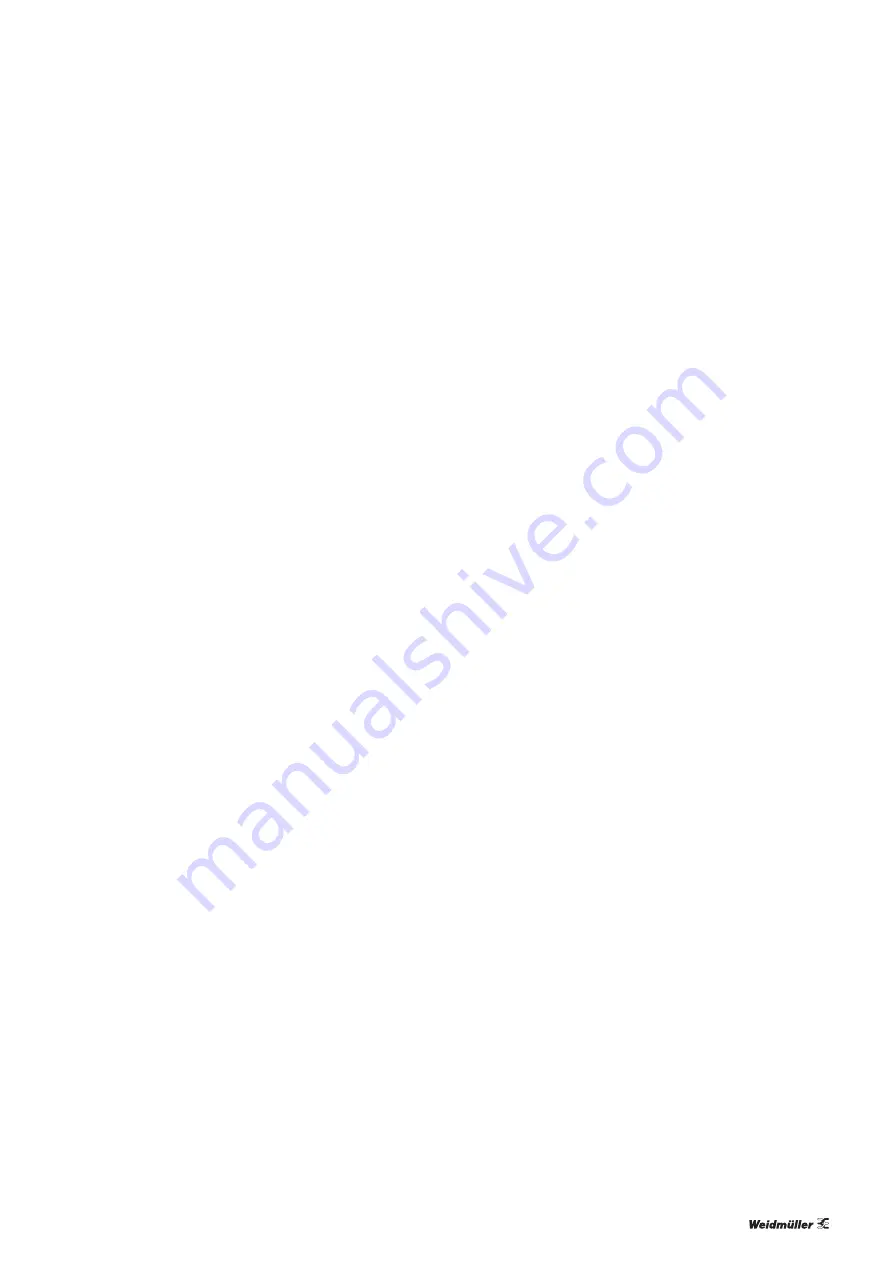
5 Commissioning and operation
| Controlling the drive system
29
Manual Stepper motor module UR20-1SM-50W-6DI2DO-P
2575290000/03/03.2020
Setting the current position of the stepper motor
You can set the current position of the stepper motor via the
process output data.
▶
Set “target position” to the desired value.
▶
Generate a rising edge for “set current position”.
The module applies the new value as the current position of
the stepper motor.
Setting the current position of the rotary encoder
You can set the current position of the rotary encoder via the
process output data.
▶
Set the “target position” to the desired value.
▶
Generate a rising edge for “set encoder value”.
The module applies the new value as the current position of
the rotary encoder.
Absolute positioning
Absolute positioning is only possible if the reference point of
the drive system has previously been determined by a refer-
ence run (“state homing” is 1 in the process input data).
During absolute positioning the drive system moves at a
specified speed from the current position to a absolute posi
-
tion within the traversing range.
▶
Set “target position” to the absolute target position (incre-
ments).
▶
Set “target velocity” to the target velocity (increments/s).
▶
Set “target acceleration” to the target acceleration in
(increments/s²).
▶
Set “acceleration” to the desired acceleration type (see
section 5.8).
▶
Set “moving mode” to 0 for absolute positioning.
▶
Set “enable motor driver” to 1 in order to release the
motor driver.
▶
Set “moving“ to 1.
The drive system travels as long as “moving“ is set to 1. The
motion is cancelled, if “moving“ is set to 0 during an active
action.
The drive system travels to the target position. “State mov-
ing” in the process input data changes to 1. “State direction”
indicates the direction. After a successful run, “state target
position” changes to 1 in the process input data.
Relative positioning
During relative positioning the drive system moves at a
specified speed from the current position by a specified dis
-
tance. The drive system can exit the parameterised traversing
range.
▶
Set “target position” to the relative distance (increments).
▶
Set “target velocity” to the target velocity (increments/s).
▶
Set “target acceleration” to the target acceleration (incre-
ments/s²).
▶
Set “acceleration” to the desired acceleration type (see
section 5.8)
▶
Set “moving mode” to 1 for relative positioning.
▶
Set “enable motor driver” to 1 in order to release the
motor driver.
▶
Set “moving“ to 1.
The drive system travels as long as “moving“ is set to 1. The
motion is cancelled, if “moving“ is set to 0 during an active
action.
The drive system travels to the target position. “State mov-
ing” in the process input data changes to 1. “State direction”
indicates the direction. After a successful run, “status target
position” changes to 1 in the process input data.
Running motion profiles
First create the motion profiles using the configuration appli
-
cation. Alternatively, write the motion profiles to the module
via the process data.
You can run motion profiles. A motion profile is a predefined
motion starting from the current position. Several motion
profiles can be combined to complex motion sequences.
▶
Set “Moving mode“ to 2 for motion profile.
▶
Set “Selection register page number“ to the number of
the register page with the first motion profile.
▶
Set “Selection data set number“ to the number of the
data set with the first motion profile.
▶
Set “Enable motor driver“ to 1, to release the motor driver.
▶
Set “moving“ to 1.
The drive system travels as long as “moving“ is set to 1. The
motion is cancelled, if “moving“ is set to 0 during an active
action.
The motion profiles are processed in the specified sequence
as long as “moving“ is set to 1. “Feedback register page num-
ber“ shows the number of the current register page. “Feed-
back data set number“ shows the number of the current data
set.