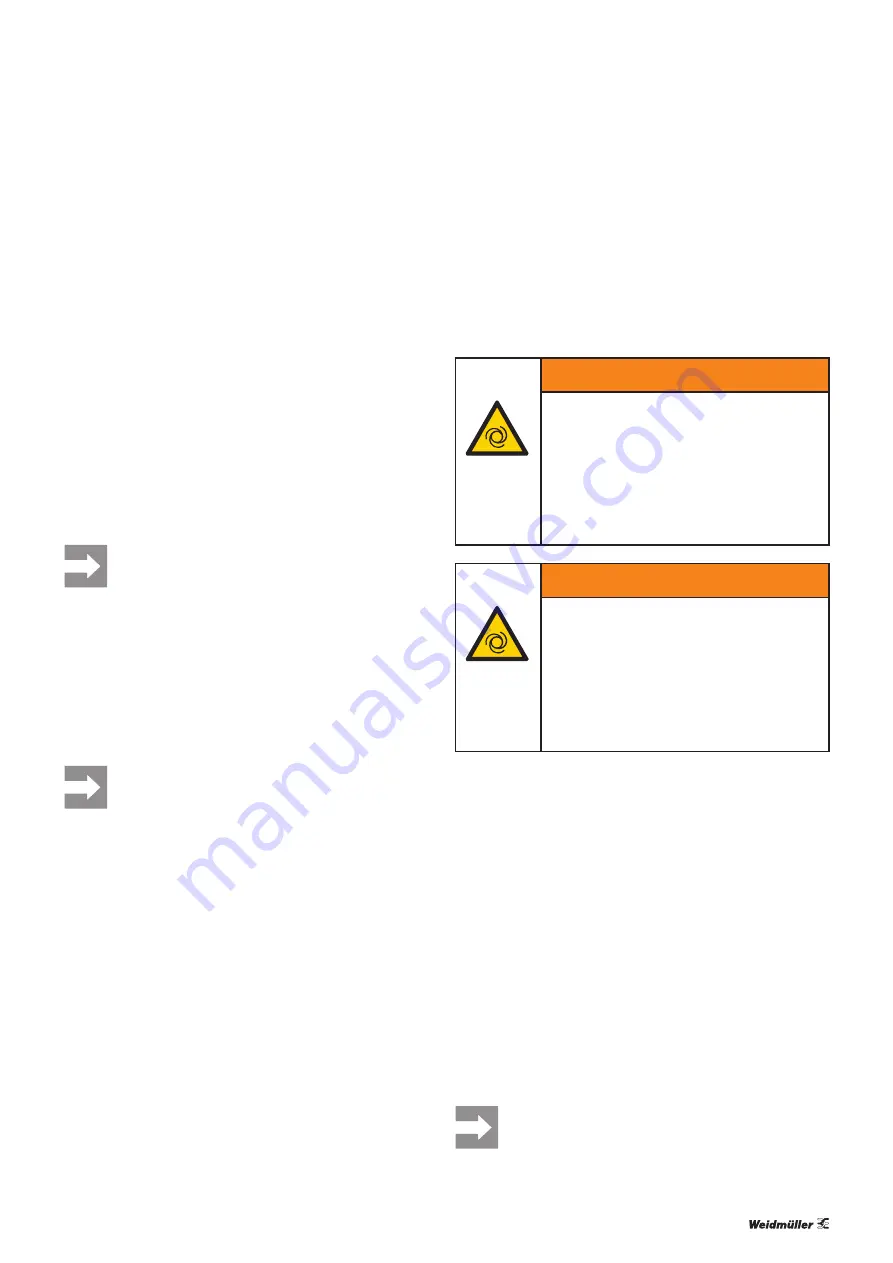
5 Commissioning and operation
| Controlling the drive system
28
Manual Stepper motor module UR20-1SM-50W-6DI2DO-P
2575290000/03/03.2020
Parameterising the module for jog or tip mode
In jog mode, the system travels a specified distance in the
specified direction with start/stop frequency, once a suitable
input signal is emitted. The motion is stopped once the sys-
tem has travelled the specified distance or has reached an
end position.
In tip mode, the system travels in the specified direction with
start/stop frequency, if a suitable input signal is emitted. The
motion is stopped once the input signal stops or an end po-
sition has been reached. End positions can only be released
in tip mode.
Jog and tip mode are set by setting the appropriate parame-
ters for the stepper motor module. For a detailed description
of the adjustable parameters, see Section 3.7.
You can also trigger jog mode without external
signalers only via the process data. In this case,
you do not have to parameterise the inputs for jog
mode.
The signalers for jog and tip mode must be connected cor-
rectly to the module (see Section 4.6).
▶
Set the “function DI” parameter for channel 2 to “jog
right/cw” for jog mode or to “tip right/cw” for tip mode.
▶
Set the “function DI” parameter for channel 3 to “jog left/
ccw” for jog mode or to “tip left/ccw” for tip mode.
We advise that you debounce switches, espe-
cially mechanical switches. To do this, set the
“filter time” parameter for the channel to “5 ms”.
5.5 Controlling the drive system
Once you have parameterised the stepper motor module for
the drive system, you can control it via the process output
data.
WARNING!
Manipulation of the control unit!
During commissioning, the system may be
manipulated to such an extent that can result
in risks to life and material damage.
▶
Make sure that system components can-
not start up unintentionally!
WARNING!
Unintentional start-up when resuming
fieldbus communication!
If the controller release is set, the connected
motor can start up unintentionally if the
fieldbus communication resumes after an
interruption.
▶
In the process output data, set the “enable
motor driver” bit to 0 if the fieldbus com-
munication fails.
Triggering referencing
The reference point of the drive system is determined
through referencing. The reference point is determined by
activating a reference switch.
If you are using a reference switch and have parameterised
the module for a reference switch, you can trigger a refer-
ence run via the process output data.
▶
Set “enable motor driver” to 1 in order to release the
motor driver.
▶
Generate a rising edge for “homing”.
The drive system executes a reference run in the parameter-
ised direction. After a successful reference run, “state hom-
ing” in the process input data changes to 1. You can then
set the current position of the stepper motor or the rotary
encoder.
If no reference switch is found during referencing,
the run ends at an end stop.