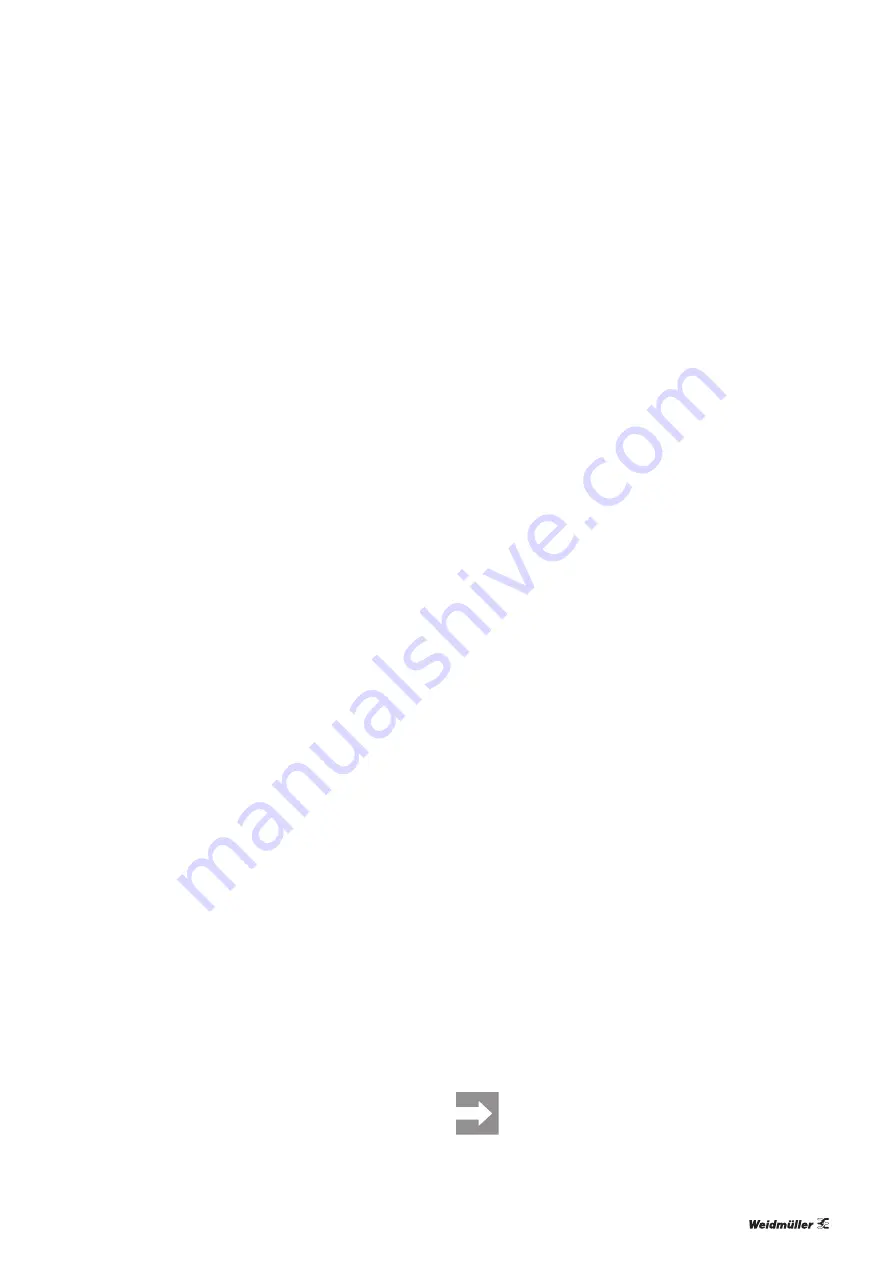
3 Module description
| Adjustable parameters
20
Manual Stepper motor module UR20-1SM-50W-6DI2DO-P
2575290000/03/03.2020
Tip left/ccw
The input records the signal for triggering tip mode in a
counter-clockwise direction.
Tip right/ccw
The input records the signal for triggering tip mode in a
clockwise direction.
“Inversion” parameter
The “inversion” parameter defines the logic of the input.
Disabled
A low level at the input generates a 0 in the process image.
A high level at the input generates a 1 in the process image.
This adjustment is ideal for sensors with NO contact switch
output.
Enabled
A low level at the input generates a 1 in the process image.
A high level at the input generates a 0 in the process image.
This adjustment is ideal for sensors with NC contact switch
output.
“Filter time” parameter
The “filter time” parameter defines the filter behaviour of an
input.
no (default)
Signals are not filtered.
5 ms
Signals with a duration of less than 5 ms are filtered.
“Function DO” parameter
The “function DO” parameter defines the function of the as
-
sociated digital output.
Digital output
The output works as a general digital output.
Position reached
The output signal is low if the current position of the stepper
motor deviates from the target position. The output signal
switches to high once the motor has reached the target po-
sition.
Position not reached
The output signal is high if the current position of the step-
per motor deviates from the target position. The output sig-
nal switches to low once the motor has reached the target
position.
“Encoder function” parameter
The “encoder function” parameter defines the function of the
connected rotary encoder.
Enc.Pos. in process data
The rotary encoder position is illustrated in the process input
data.
Contouring error monitoring
The module calculates the contouring error as the difference
between the current motor position and the rotary encoder
position, and generates an error message if the contouring
error is larger than the permitted contouring error. The per-
missible contouring error is adjusted using the “contouring
error” parameter.
Disabled
The rotary encoder function is disabled.
“Homing” parameter
The “homing” parameter defines the type of reference run.
Stop on ref.switch 0➝1
The motor travels in the specified direction with start/stop
frequency. The reference run ends once the reference switch
has been triggered.
Stop on ref.switch 1➝0
The motor travels in the specified direction with start/stop
frequency. The reference run ends once the reference switch
has been triggered and the motor has been moved in the op-
posite direction with ¼ of the start/stop frequency.
Stop on homing bit 1➝0
The reference run ends when the “homing” bit changes from
1 to 0 in the output data.
“Encoder resolution” parameter
The “encoder resolution” parameter is used to adjust the re-
solution of the connected rotary encoder in increments.
0 ... 65,535 (default: 1,000)
The connected rotary encoder has a resolution of
0 ... 65,535 increments.
The stepper motor module always evaluates all
four flanks of the rotary encoder signal.