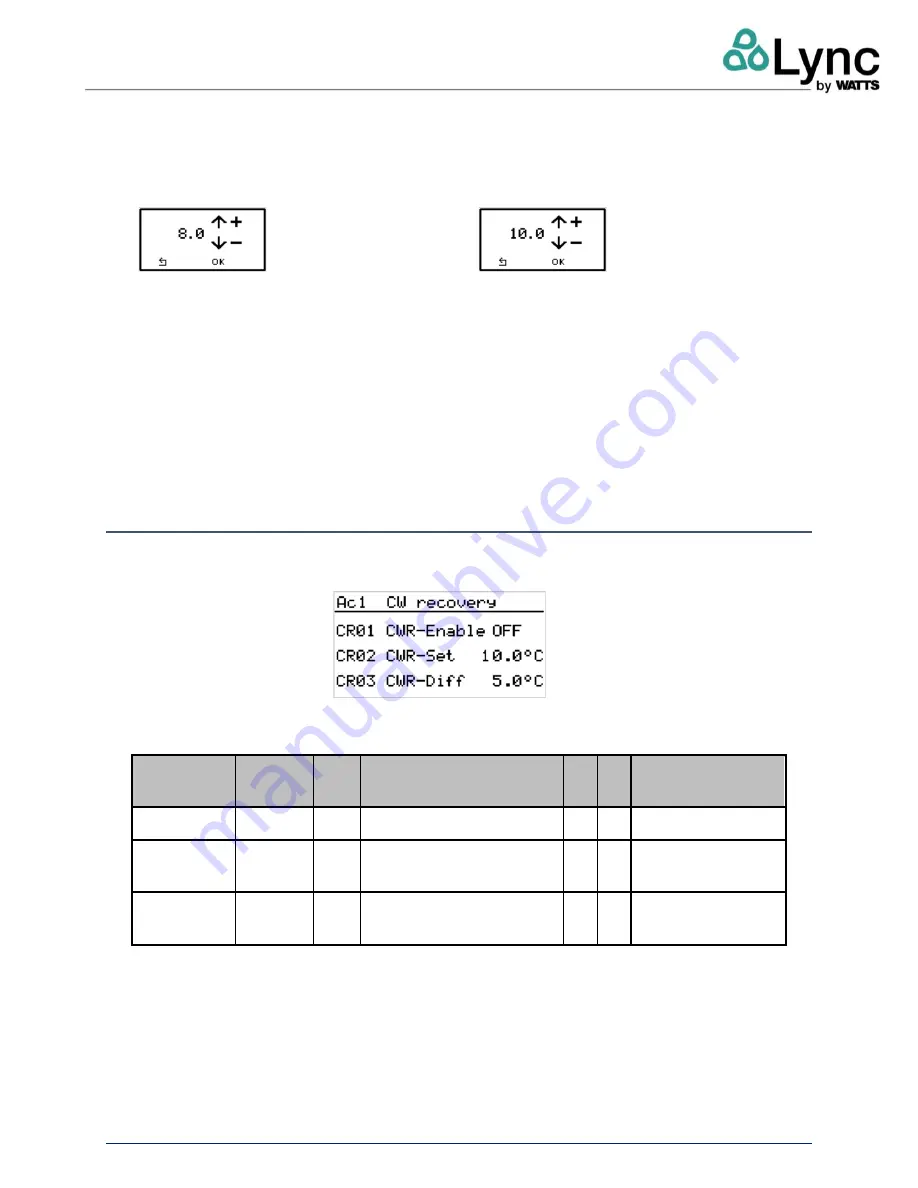
Lync AEGIS Controller
8: APPENDIX D
L-OMM-013_A
• 4/20/2022Technical Support • (800) 433-5654 • Mon-Fri, 8 am - 5 pm EST
74
of
100
•
press the OK key to confirm changes and close the set point screen.
In the differential temperature windows (parameters ST04
– ST07):
•
press the UP key to increase the value by 0.1°C (32.1°F);
•
long press the UP key to increase the value by 1°C (33.8°F);
•
press the DOWN key to reduce the value by 0.1°C (32.1°F);
•
long press the DOWN key to reduce the value by 1°C (33.8°F).
•
press the BACK key to close differential adjustment screen without confirming changes;
•
press the OK key to confirm changes and close the differential adjustment screen.
8.9.9. MENU - AC CW RECOVERY (COOL RECOVERY)
On the A.Settings menu, with the c.CW RECOVERY menu selected, press the RIGHT key to
access the cold recovery function setting screen.
Select the following parameters with the UP and DOWN keys:
Modbus
address
Read
Write
Code
Meaning
Min
Max
Unit of
measurement
9638
RW
CR01 Enable cold water recovery OFF
ON
16807
RW
CR02 Cold water recovery set
point
-30 50 °C
16808
RW
CR03 Cold water recovery
differential
0
30 °C
When the parameter is selected, press the OK key to access the window where it can be edited.
In the function enable/disable window (parameter CR01):