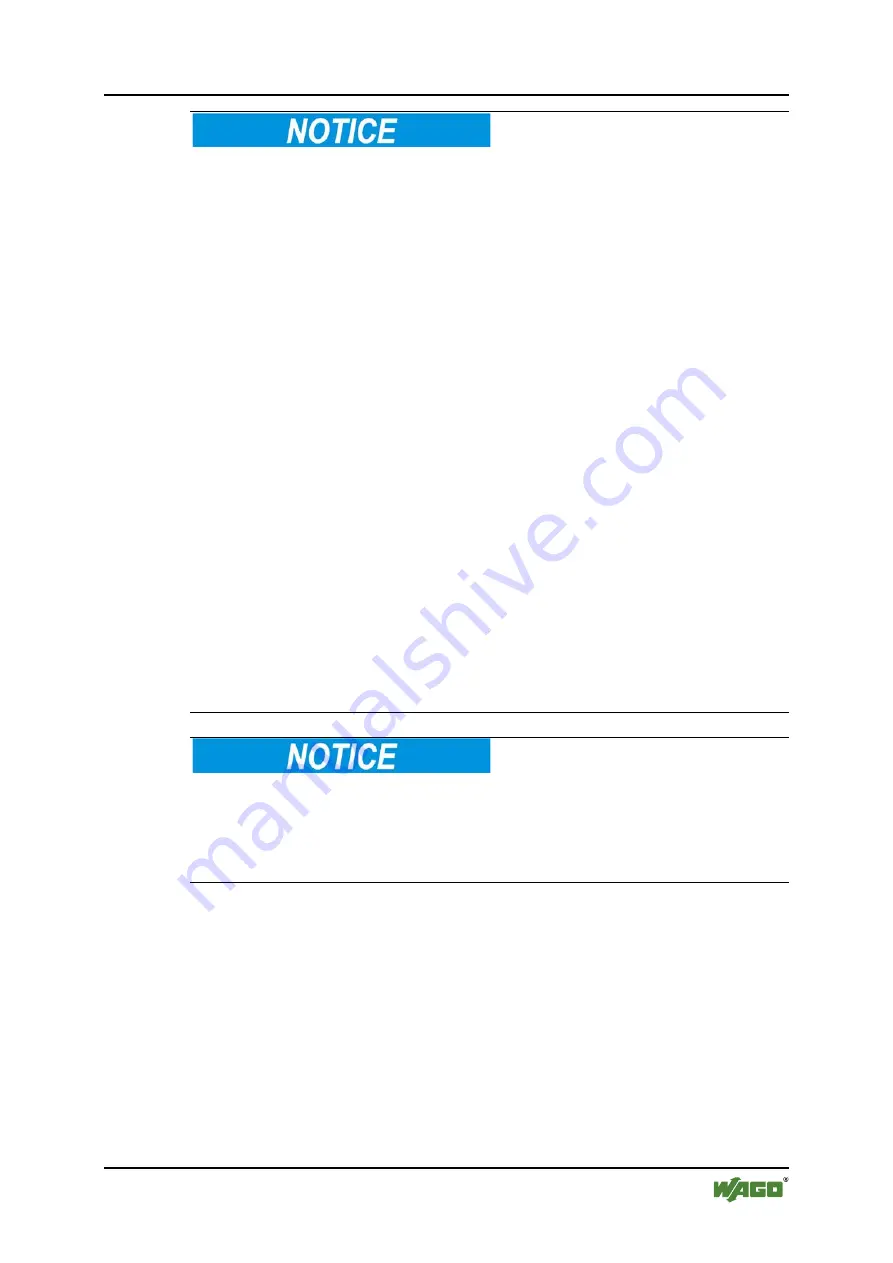
WAGO-I/O-SYSTEM 750
Connect Devices
53
750-666/000-003 4FDI/2FDO 24V/10A PROFIsafe V2 iPar
Manual
Version 1.2.0, valid from HW/SW Version 01/01
Only operate the PROFIsafe I/O module with external fuse!
A suitable fuse must be used to protect the PROFIsafe I/O module because the
PROFIsafe I/O module does not have internal overcurrent protection. Please note
that a suitable fuse must also be used to protect digital power output O2 when
using the "H-Side/L-Side 2" and "H-Side/H-Side 2" output configurations (see
section "Initial Configuration Parameters"). You can a safety fuse according to
EN 60127-2, miniature circuit-breaker according to EN 60947-2 or a electronic
fuse such as WAGO 787-861 to protect the PROFIsafe I/O module.
The safety fuse according to EN 60127-2 must have the following technical
properties:
•
G fuse link (e.g., WAGO Order No. 282-122)
•
Rate current 10A
•
Time-lag
•
Surge resistant
•
Large or increased breakin capacity
•
Rated voltage of min. 250 V
•
Time-current characteristic: 275% from rated current corresponding to
27.5A maximum 80s
The miniature circuit-breaker according to EN 60947-2 must have the following
technical properties:
•
Miniature circuit-breaker according to EN 60947-2
•
Rate current 10A
•
Tripping characteristic Z
•
Rate
d voltage ≥ 60V DC
Do not exceed maximum current via power contacts!
The maximum current that can flow through the power jumper contacts is 10 A.
The power jumper contacts can be damaged when the maximum is exceeded.
When configuring the system, do not exceed this current. This can be achieved by
using additional power supply modules.
A PELV/SELV power supply unit must be used to power each fieldbus node in a
PROFIBUS or PROFINET network, even if it does not contain any PROFIsafe
I/O modules. The overall cabling of the fieldbus node in the field must meet
PELV/SELV guidelines.
The PROFIsafe I/O module 750-666/000-003 has two supply points for the 24V
field supply voltage.
For clock outputs T1 - T2 and digital inputs I1 - I4, the field supply voltage is
provided by an upstream module or the fieldbus coupler/controller via the power
jumper contacts implemented as knife blade contacts/V-type.