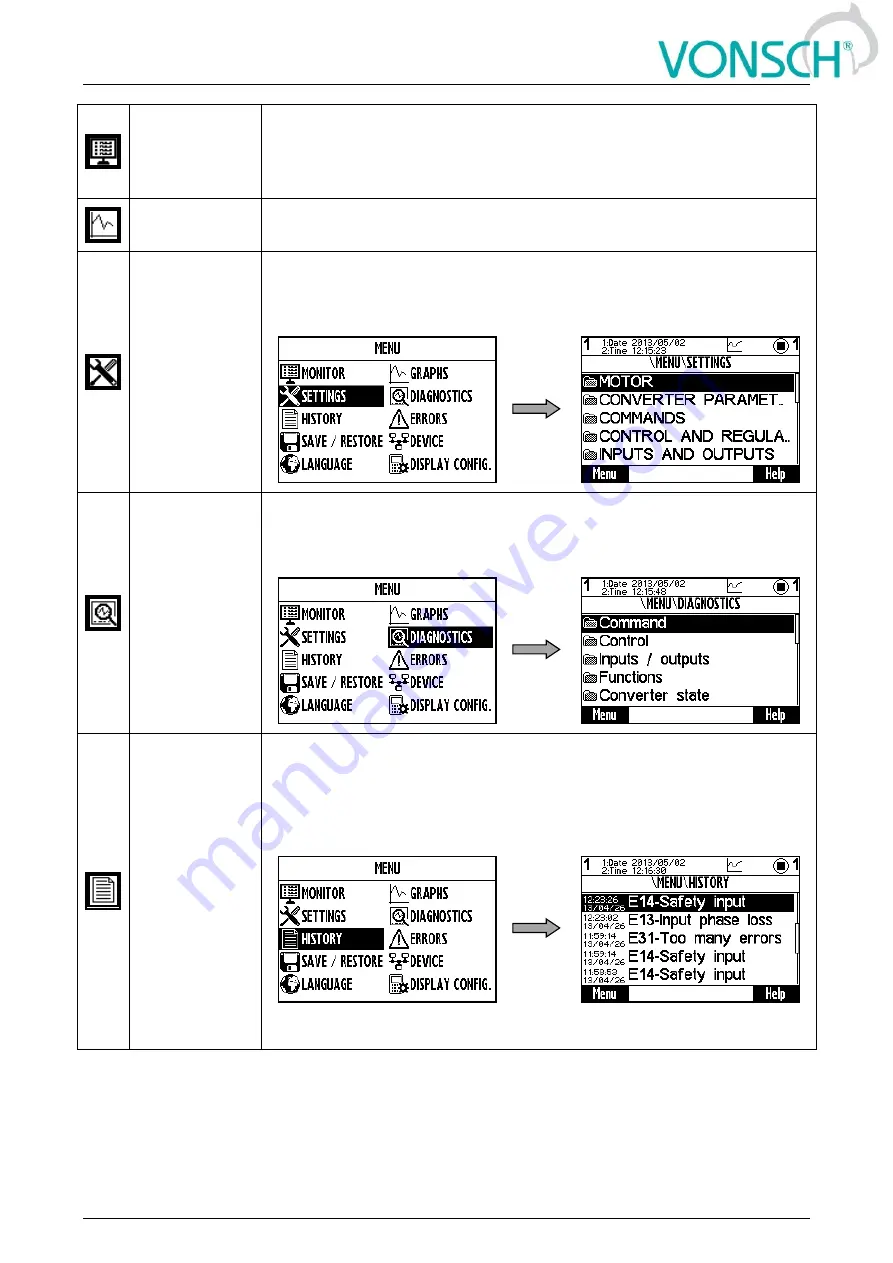
UNIFREM v.3.41x
10 May 2017
Page 171 from 180
Panel function selection
MONITOR
Monitor view (Monitor detail)
Setpoint frequency setting, if control panel is selected as the setting
source
GRAPH
Signal record displaying.
SETTING
Converter parameter setting in the tree structure. Move by using selection
arrows or by using the F1 button to the SETTINGS item and confirm by
pressing ENTER.
DIAGNOSTICS
All converter status informations displaying in the tree structure.Move by
using selection arrows or by using the F1 button to the item
DIAGNOSTICS and confirm by pressing ENTER.
HISTORY
Move by using selection arrows or by using the F1 button to the item
HISTORY and confirm by pressing ENTER. Converter events
(Parameters restore, parameter change..) and event history displaying
(date and time of event emergence, description). After fault or event
selection, recorded data at emergence will be displayed.
EXAMPLE: