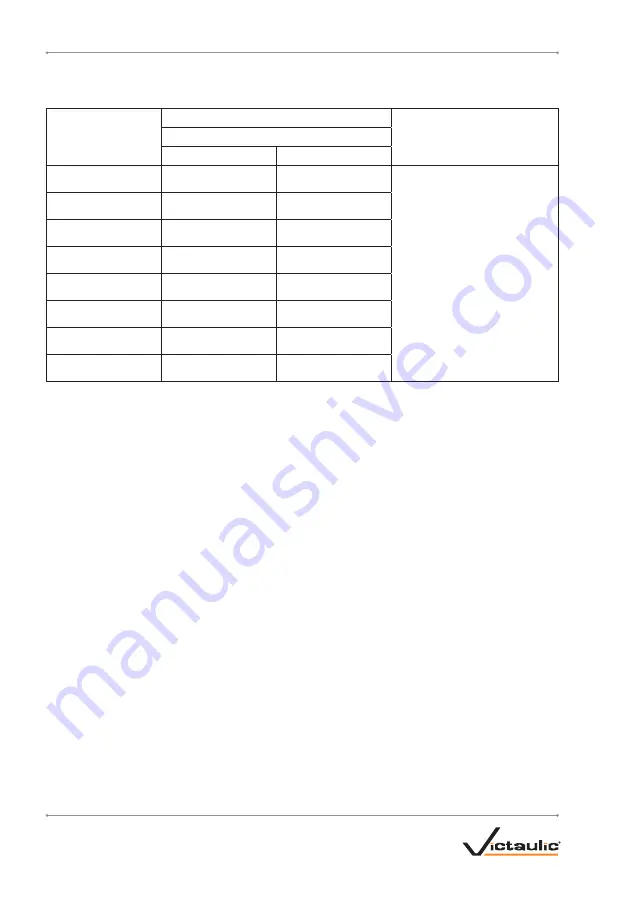
TM-VE414/415MC_52
REV_D
TM-VE414/415MC
/ Operating and Maintenance Instructions Manual
ROLLS FOR EUROPEAN STANDARD – EN 1057 DRAWN COPPER TUBING –
COLOR-CODED COPPER
Nominal Size
mm
Dimensions – millimeters/inches
Copper Roll
Part Numbers
Copper Tubing Wall Thickness ‡
Minimum
Maximum
54.0
1.2
2.0
Lower Roll
RRE1272L06
Upper Roll
RRE1272U06
0.047
0.079
64.0
2.0
2.0
0.079
0.079
66.7
1.2
2.0
0.047
0.079
76.1
1.5
2.0
0.059
0.079
88.9
2.0
2.0
0.079
0.079
108.0
1.5
2.5
0.059
0.098
133.0
1.5
3.0
0.059
0.118
159.0
2.0
3.0
0.079
0.118
NOTE: The European Standard (EN 1057) replaces the British Standard (BS 2871) and DIN Standard (DIN 1786). However, to
ensure proper product performance, refer to Tables X and Y in the British Standard (BS 2871).
Summary of Contents for VE414MC
Page 2: ......
Page 47: ...This page intentionally blank...
Page 59: ...This page intentionally blank...