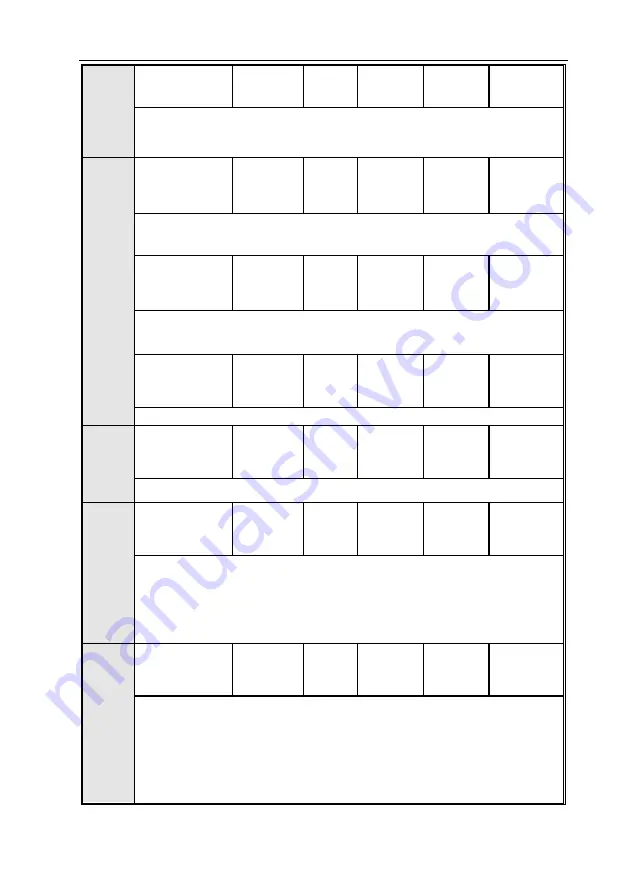
10 Function Code Instructions
222 SD780 Series Servo Technical Manual
Pn243
Model tracking
control speed
feedforward gain
0
~
1000
100.0
%
0x0243
Immediately
The feed forward gain of the model tracking speed is reduced, and the responsiveness is slower, but
position overshoot doesn’t easily occur. If the feedforward gain is too small, the position deviation will
end in a long time.
Pn244
Model tracking
control forward
torque feedforward
gain
0
~
1000
100.0
%
0x0244
Immediately
It’s a forward position command and could be used when adjusting the forward response separately.
When it is increased, the torque feed forward rises faster and the positioning time can be shortened
appropriately.
Pn245
Model tracking
control reverse
torque feedforward
gain
0
~
1000
100.0
%
0x0245
Immediately
It’s a reverse position command and could be used when adjusting the forward response separately
When it is increased, the torque feed forward rises faster and the positioning time can be shortened
appropriately.
Pn246
Second model
tracking control
attenuation
coefficient
1
~
2000
50.0
1/s
0x0246
Immediately
Use 2
nd
gain when model tracking is valid.
Pn247
Second model
tracking control
attenuation
coefficient
50
~
200
100.0
%
0x0247
Immediately
Use 2
nd
gain when model tracking is valid.
Pn249
Speed
feedforward/torque
feedforward
selection
0x00
~
0x01
0
-
0x0249
Immediately
0-Do not use model tracking control, external speed and torque feed forward at the same time.
1-Use model tracking control, external speed and torque feed forward at the same time.
When using the model tracking control, the optimal feedforward will be set and it is not recommended
to use the “speed feed forward (V-REF) input” and “torque feed forward (T-REF) input” from the
upper unit at the same time. However, it can be used at the same time as needed. In this case, if the
input feed forward is incorrect, it may cause overshoot and system instability.
Pn250
Application method
of external encoder
in full closed loop
control
0
~
3
0
-
0x0250
After restart
0 - Full closed loop function is not used .
1 - Use in standard direction.
2 - Use in reverse direction .
When setting the forward rotation of the motor, if the moving direction of the grating ruler is set
incorrectly, it may cause an alarm of speeding or excessive deviation between the motor and load.
Before operation, manually move the load and change this parameter to make the change direction
of the monitoring parameter Un007 (feedback pulse counter) and Un012 (feedback pulse counter of
external encoder) consistent before operation.