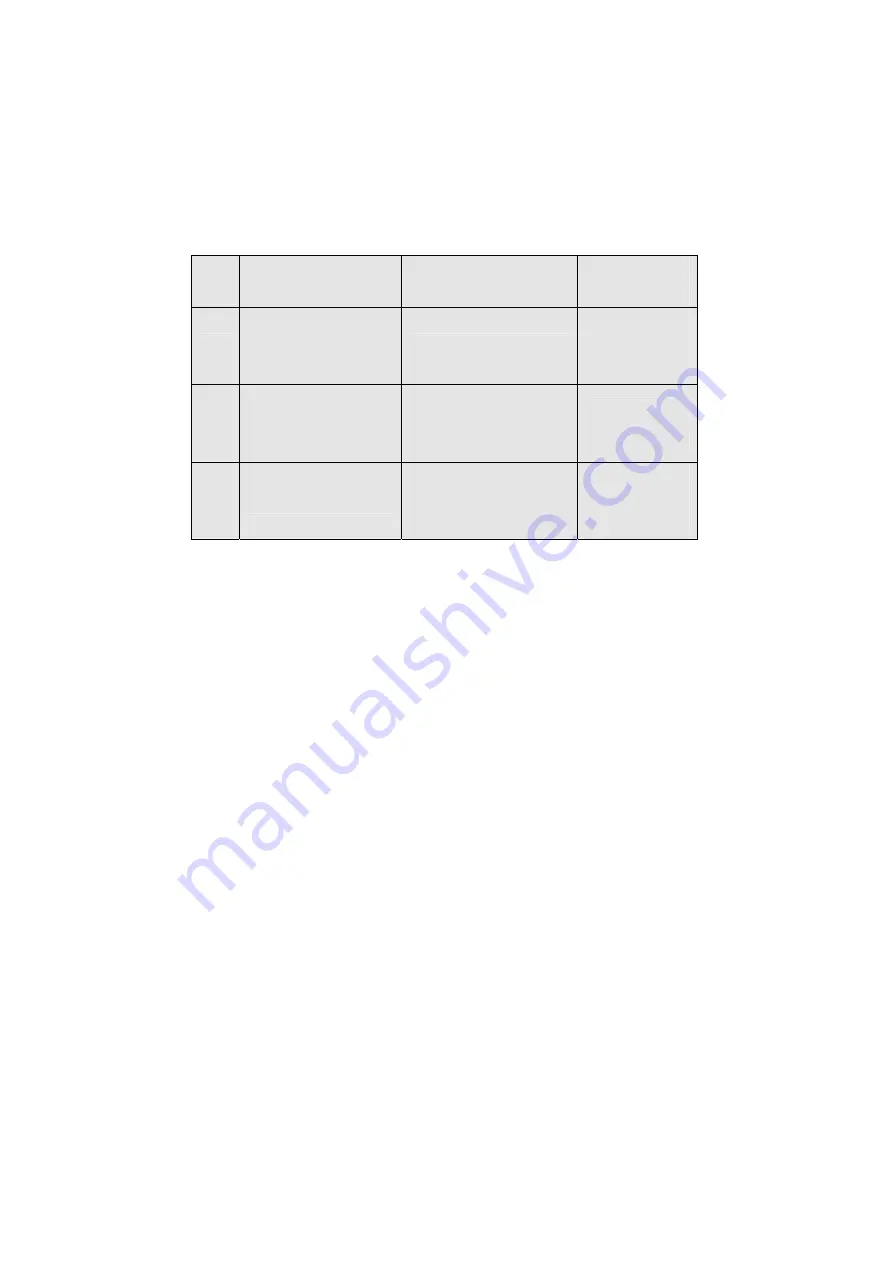
87
unit(above 18.5G/22P) can choose external braking unit and braking resistor.
This mode is mainly suitable for occasions need quick braking while stop.
1: Free stop After receiving the stop order, frequency inverter will block
the output and motor will free run to stop. If users choose this method,
frequency inverter generally coordinate with the external mechanical brake
to fulfill quick stop.
DC braking voltage is the braking voltage gived by the frequency inverter to
the motor in the DC braking stage. This numerical value is based on the frequency
inverter rated voltage input.
DC braking function can provide “0”speed torque. Normally it is used
to enhance the stop accuracy and fulfill quick stop, but it can not be used
in the deceleration braking in normal operation; Once start DC braking,
frequency inverter will stop output. If the DC braking current is set too high ,
it easily occur overcurrent fault during the frequency inverter stop.
DC braking time in stop stage is the duration of the DC braking voltage while
stop. If the braking time is 0.0 second, there is no DC braking process.
E-35
DC braking voltage
Range :0.0%~15.0%
Factory
setting :5.0%
E-36
DC braking time in stop
stage
Range :0.0~30.0 second
Factory
setting :0.0
second
E-37
DC braking initial
frequency in stop
stage
Range :0.00~60.0Hz
Factory
setting :0.00Hz
E-38
DC braking time in
start stage
Range :0.0~10.0 second
Factory
setting :0.0
second
Summary of Contents for AC60 series
Page 1: ...Manual AC60 series frequency inverter Version V2 0...
Page 30: ...26...
Page 44: ...40 2 Double display keyboard cycle switch the display of monitoring parameter mode...
Page 46: ...42 2 Double display keyboard parameter setting mode...
Page 162: ...158 8 2 2 Over current...
Page 163: ...159 8 2 3 Over voltage...
Page 164: ...160 8 2 4 Supply voltage is too low...
Page 165: ...161 8 2 5 Inner inverter over heat...
Page 166: ...162 8 2 6 Over load...
Page 167: ...163 8 2 7 No display 8 2 8 Motor heat...
Page 168: ...164 8 2 9 Motor does not rotate...