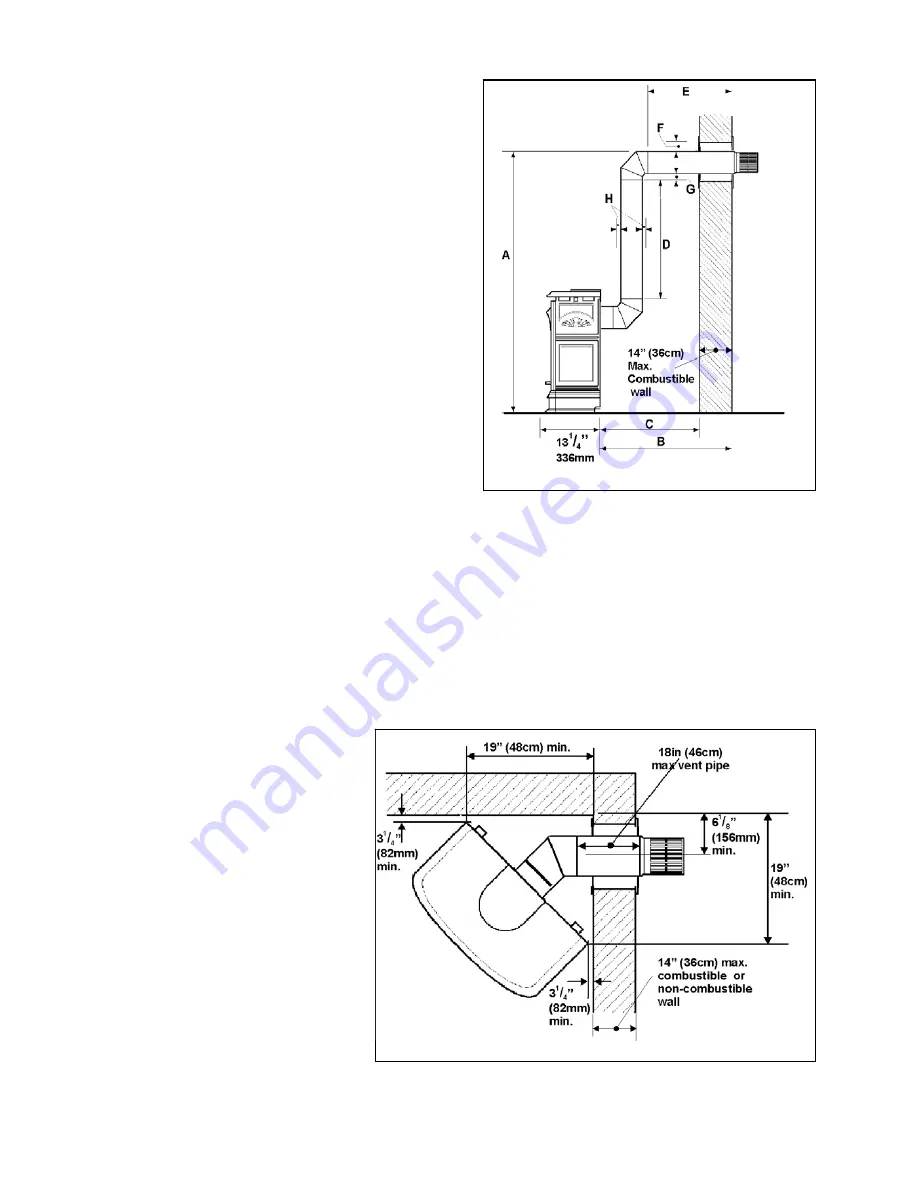
Manufactured by Miles Industries Ltd., British Columbia, Canada
7
4.2.3.
Rear vent connection, vertical vent rise with
horizontal termination (Fig. 7)
Can be used with either #551DVK standard vent kit or #984
Dura-vent terminal cap and accessories.
Adapter #817VAK, two 90° vent elbows #990B and Dura-vent
pipe lengths will be required.
(See venting options section of this manual).
No more than two 90°elbows must be used.
The location requirements are (See figure 7):-
Minimum Maximum
A
: From floor to top of
vent duct
3ft 7in
(109cm)
10ft 7in
(323cm)
B
: Back of appliance
to outside wall
- 5ft
5in
(165cm)
C
: Back of appliance
to inside wall
14
1
/
8
in
(36cm)
-
D
: Vertical pipe run
12in (30cm)
8ft (244cm)
E
: Horizontal pipe run
(Total before and after
elbows)
- 4ft
6in
(137cm)
F
: Clearance to
combustible materials
above horizontal pipe
run
2
5
/
8
in
(6.7cm)
-
G
: Clearance to
combustible materials
below horizontal pipe
run
1
5
/
16
in
(3.3cm)
-
H
: Clearance to
combustible materials
all round vertical pipe
run and at sides of
horizontal pipe run
1
5
/
16
in
(3.3cm)
-
Figure 7
4.2.4.
Rear vent connection, vertical vent rise with horizontal snorkel termination
For “semi-basement” situations where vertical vent rise does not raise horizontal termination sufficiently above ground level.
The dimensional requirements in section 4.2.3 and figure 7 apply.
Adapter #817VAK, two 90° vent elbows #990B, Dura-vent pipe lengths and a Dura-vent snorkel termination will be
required.
#942 Dura-vent wall thimble kit may also be
necessary.
(See venting options section of this manual).
No more than two 90°elbows must be used.
4.2.5.
Corner location, horizontal vent
run only (Fig. 8)
Can be used with either #551DVK standard
vent kit or #984 Dura-vent terminal cap and
accessories.
Adapter #817VAK and 45° Dura-vent elbow
will be required.
(See venting options section of this manual).
Be aware of the limited maximum vent pipe
length and wall depth for this type of
installation – See figure 8.
Figure 8