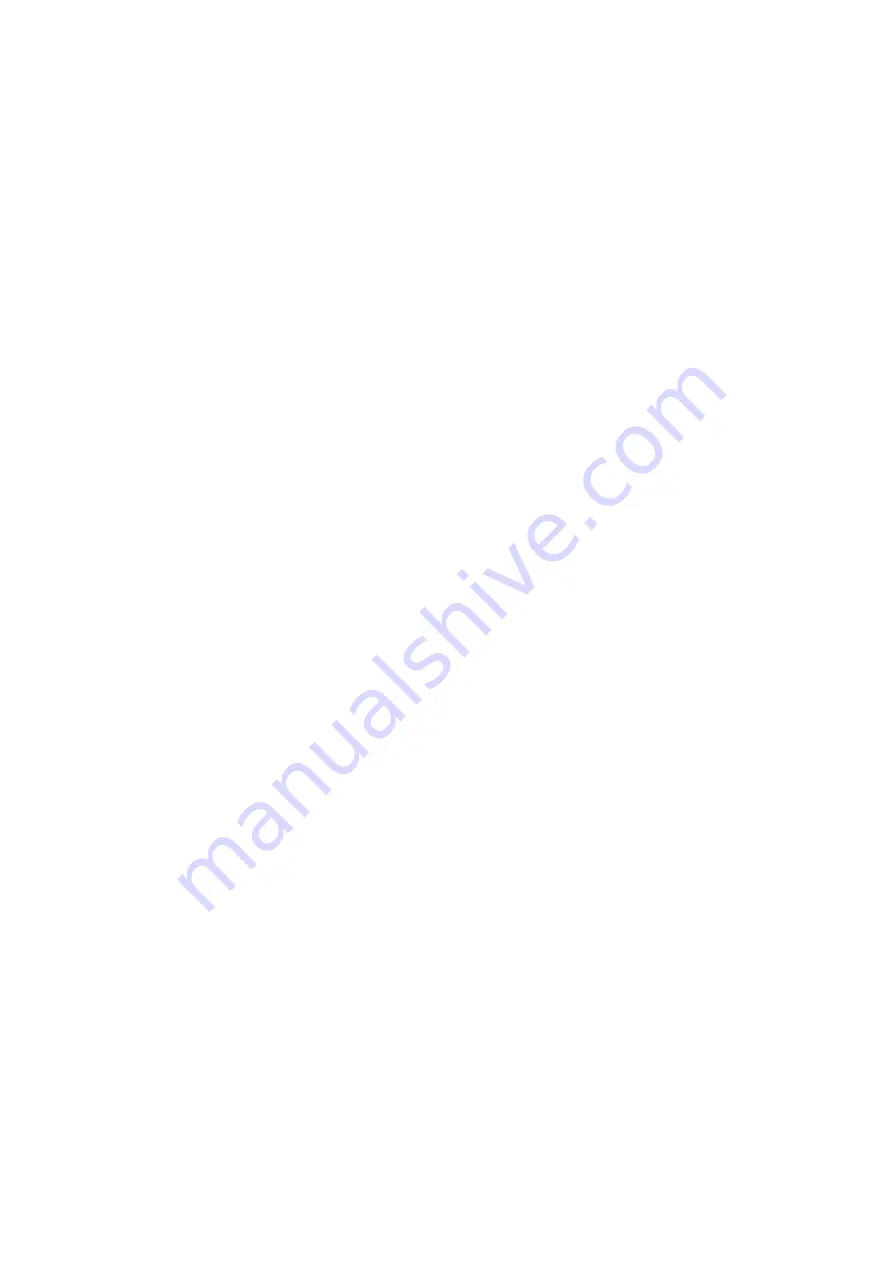
88
Under the action of the spring relief valve 1 is closed. With the governor in
such a state the pneumatic system is filled with compressed air from the compressor.
When the pressure in hollow A equals 800 kPa (8.0 kgf/cm
2
), piston 7 overcomes
the force of spring 5 and goes up, valve 4 gets closed, inlet valve 11 gets opened,
and the compressed air from hollow A is delivered to hollow B.
Under the action of the compressed air relief piston 13 goes down, valve 1 gets
opened, and the compressed air from the compressor via outlet III is let out to the
atmosphere together with the condensate accumulated in the hollow; in so doing
return valve 10 gets closed.
When the pressure at outlet II and in hollow A drops to 637 kPa (6.5 kgf/cm
2
),
piston 7 under the action of spring 5 goes down, valve 11 gets closed, outlet valve 4
connects hollow B with the atmosphere through outlet I. In so doing relief piston 13
gets closed under the action of the spring, and the compressor resumes to charge
the compressed air into the pneumatic system.
Relief valve 1 serves also as a safety valve. If the regulator fails to operate at
the pressure of 800 kPa (8.0 kgf/cm
2
) and the pressure increases up to 1000-1300 kPa
(1.0-1.3 kgf/cm
2
), then valve 1 gets opened, and the system gets free from the
excess pressure.
The regulator is adjusted with bolt 6: when it is being screwed in, the pressure
is growing, when being screwed out – the pressure is decreases. The pressure,
when the safety valve comes into action, is adjusted by changing a number of the
shims mounted under valve 1 spring. To determine if the pressure regulator operates
properly, you should regularly observe values of the air pressure with the help of
the two
-
pointer pressure gauge on the dashboard in the course of engine running
and check how often the governor comes into action.
The two-unit brake valve
(Fig. 70) is designed for control over the actuating
mechanisms of the truck service brake system as well as for control over the trailer
brake drive valve.
The brake valve consists of the upper and lower casings. The lever mechanism
of the valve is fastened to the upper casing. The lever body is protected from mud
and moisture by the hood.
Small piston 14, which is pressed to large piston 23 by spring 21, is installed in
lower casing 15. Valve 24 in the upper unit of the brake valve is pressed to the seat
in the lower casing by spring 16.
V
1
and V
2
outlets are connected with the air bottles of two separate circuits of
service brake drive. The compressed air flows from Z
1
outlet to the air booster of the
front axle brake circuit and it flows from Z
2
outlet to the braking forces regulator
and air booster of the intermediate and rear axle brake circuit.
When pressing the brake pedal, the effort is transmitted via the system of lev-
ers and drive tie rods to lever 1 of the brake valve and then via lifter 6, head 8
and the elastic element to follower piston 25. Moving down, piston 25 first closes
the outlet hole of valve 24 of the brake valve upper unit, and then detaches valve 24
from the seat in upper casing 11, opening the passage to the compressed air from
V
1
outlet or Z
1
outlet and further to the actuating mechanisms of one of the circuits.
Pressure at Z
1
outlet is being increased until the force of pressing lever 1 has been
equalized by the force established by the pressure onto upper follower piston 25.
Thus, the action of the follower is performed in the upper unit of the brake valve.
At the same time as the pressure grows at Z
1
outlet, the compressed air
through hole «a» gets into hollow above large piston 23 of the brake valve lower
unit. Moving down, the large piston closes the outlet hole of valve 17 and detaches