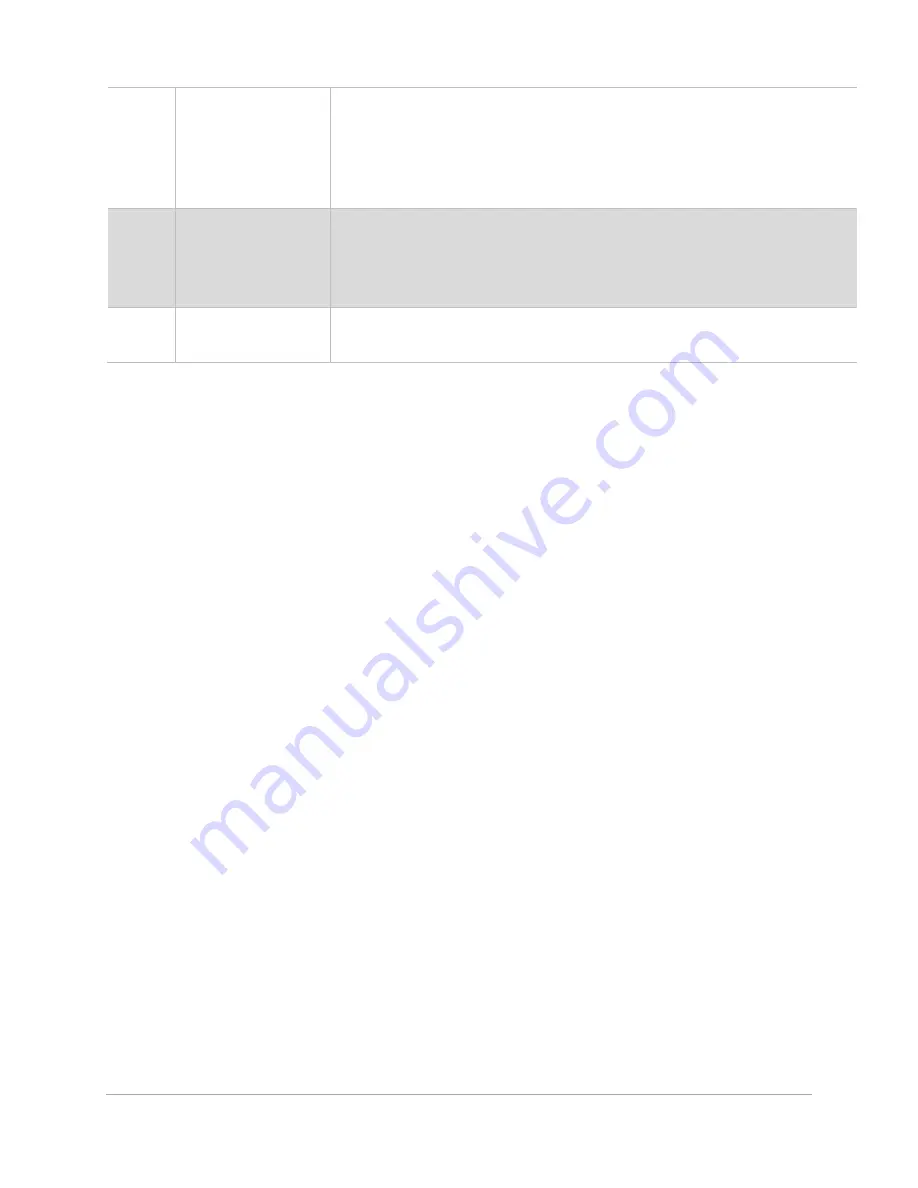
42
C
Duplication Gap
Dialog
Provides fields for adjustment of the design file duplication gap in both
the X and Y directions. The gap is the space between the outermost
extents of the design file.
Changing either the pitch or gap will override any previous pitch or gap
settings. Units are adjustable in the
Systems Configuration
Page
.
D
Duplicate to Fill
Button
Generates duplications to fill the field rightwards and downwards from
the location of the original design file.
To maximize the number of instances, place the original design file in
the upper left-hand corner of the processing area before duplication.
E
Remove
Duplicates Button
Removes all duplicate design files and returns the
Row
and
Column
counts to a value of one.
Summary of Contents for ULTRA X6000
Page 1: ...ULTRA X6000 Laser System User Guide www ulsinc com Version 2020 06 0102...
Page 4: ...4 This page left intentionally blank...
Page 12: ...12 ULTRA X6000 Platform Side View All dimensions are indicated in inches and millimeters...
Page 19: ...19 ULS CO2 Laser Source Safety Labels...
Page 20: ...20 ULS Fiber Laser Source Safety Label...
Page 21: ...21 ULTRA X6000 Platform Safety Labels Isometric Side View...
Page 22: ...22 ULTRA X6000 Platform Safety Labels Rear View...
Page 23: ...23 ULTRA X6000 Platform Safety Labels Left View...
Page 24: ...24 Class 4 Pass Through Safety Labels...
Page 27: ...27 Meet the ULTRA X6000 Platform 3...
Page 32: ...32 This page left blank intentionally...
Page 83: ......