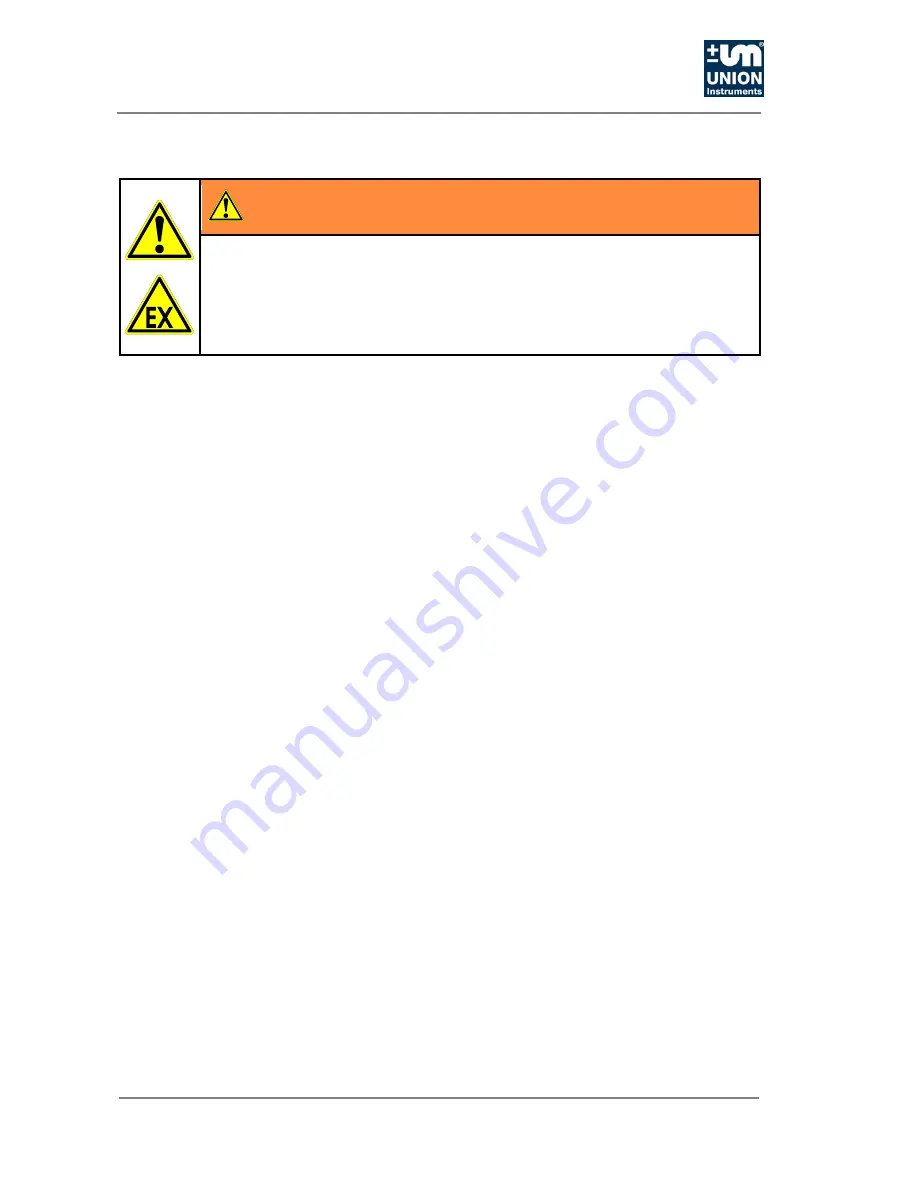
CWD2005 DPC
chapter — page:
3—8
3.4.5 Instrument air supply
WARNING
Protective gas - instrument air generates the protective functions against explo-
sions by purging and creating an overpressure!
Establishing instrument air connections and working on the instrument air equip-
ment of the system may only be carried out by specialists adhering to the safety
regulations, especially those regarding explosive areas.
Summary of Contents for CWD2005 DPC
Page 1: ...Operating instructions Combustion calorimeter CWD2005 DPC Mai 2017 V2 01 ...
Page 12: ...CWD2005 DPC chapter page 2 2 ...
Page 28: ...CWD2005 DPC chapter page 4 6 ...
Page 114: ...CWD2005 DPC chapter page 9 2 ...
Page 116: ...CWD2005 DPC chapter page 10 2 ...
Page 119: ...CWD2005 DPC Annex chapter page 11 5 ...
Page 120: ...CWD2005 DPC Annex February 2015 V2 00 chapter page 11 6 ...