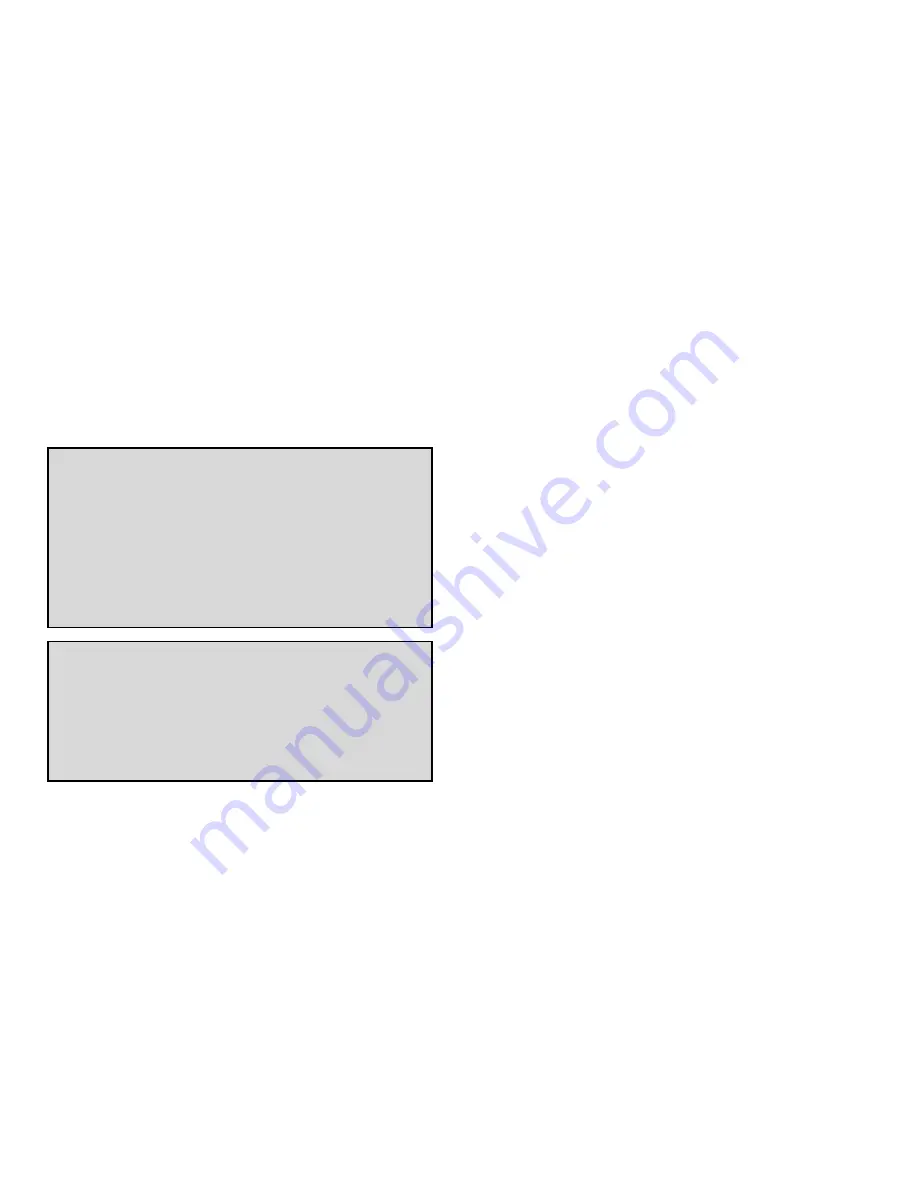
Under normal circumstances, it should not be neces-
sary to add or drain oil from the pump between recom-
mended oil changes.
A significant drop in oil level means there is an oil leak
or that an exhaust filter is broken, and the pump should
be smoking excessively. It is normal for the oil to be
foamy and light in color in an operating pump.
However, if the oil is milky colored, it is an indication
that water is present in the oil. Normally, by operating
the pump for an extended period, with the inlet suction
blanked off and the gas ballast open, the water will be
purged from the oil. If the oil is dark colored, it is con-
taminated or carbonized and must be changed.
Depending on the severity of the contamination, a thor-
ough flushing may be required. Contact the factory for
flushing oil (Busch R568) and instructions.
3.1.2 Oil Type and Quantity
See Section 1.5 and the Technical Data page 13 for
details on oil type and quantity.
3.1.3 Oil and Filter Change
Check the oil for contamination on a weekly basis by
shutting the pump off and draining some of the oil into
a small glass or a similar transparent container through
the oil drain port (Ref. 95).
Oil life is dependent upon the conditions to which it is
exposed. A clean, dry air stream and an oil operating
temperature under 210°F are ideal conditions. Oil must
be changed after the first 100 initial hours of operation.
After the initial oil change, and when using R530
(hydrocarbon oil), it is recommended that oil changes
are made every three (3) to four (4) months or 500 to
750 hours of operation, or as necessary if high heat is
contaminating the oil. The use of Busch R570 (syn-
thetic) or R590 (semi-synthetic) oil may significantly
extend the operating hours between oil changes; how-
ever, you may need to flush out the pump before chang-
ing. Contact the factory Service Department for advice
or refer to Section 3.1.4 for the flushing procedure.
To change the oil, the pump must be switched off and
ventilated to reach atmospheric pressure. Remove the
oil drain plug (Ref. 95) and drain the oil. Dispose of the
oil in compliance with local or national regulations.
When the oil stops draining, replace the oil drain plug.
Start the pump again for a few seconds. Stop the pump
once again, and then reopen the drain plug and dis-
charge any remaining oil.
Refasten the oil drain plug. Remove the oil filter (Ref.
100) and replace it with a new one using a Busch gen-
uine oil filter. Make sure to tighten the filter securely
against the aluminum sealing surface so that leaks will
not occur.
Excessive Heat
When the pump is subjected to operating conditions
that will cause the oil to be heated above 210°F, the oil
will carbonize and become contaminated after a rela-
tively low number of operating hours. The higher the
temperature, the quicker the oil becomes contaminated.
If the oil temperature is too severe, Busch R570 or
R590 synthetic oil should be used to withstand the ele-
vated temperatures. When changing to synthetic oil,
the pump should be flushed with Busch R568 oil.
Contact the factory for instructions on the flushing pro-
cedure. Auxiliary oil cooling is the most practical
approach to a severe heating problem.
Contaminated Air Stream
When the air stream contains solids and/or liquid that
contaminate the oil, the oil must be changed more
often. If the air stream contains a small percentage of
contaminates and/or they are slightly aggressive* (mild
acids, etc.), synthetic oil, such as Busch R570, will
resist breakdown better than the standard Busch R530.
The solution is to install a filter or knock-out pot to keep
the contaminates out of the pump.
*Process air streams with a large percentage of con-
taminates and/or are more than slightly aggressive
must use a chemical duty pump.
Oil change intervals can only be established by experi-
ence with the pump operating in the actual conditions
(see previous paragraph for some of the conditions).
Develop the oil change interval by periodically checking
an oil sample removed from the pump. When the oil
sample has become dark in color (from solids and car-
bonized particles) or is milky looking (from water), it is
time to discard it. As mentioned before, a thorough
flushing may be required.
CAUTION: When changing the oil and fil-
ters, it may be necessary to flush the pump
to remove any build-up of degraded oil from
the sumps, oil lines, radiators, etc. to
ensure proper oil flow through the pump.
Reduced oil flow, especially through radia-
tors and cooling coils, can cause mechani-
cal damage or extreme overheating which
could cause the oil vapors to ignite.
WARNING: Always take the necessary pre-
cautions concerning personal protective
equipment when changing oil and make
sure the pump is switched to the "off" so
that accidental starting will not occur. Oil
temperature can reach 212°F and may pose
a danger of scalding.
6
Summary of Contents for ULTRAVAC 2100
Page 2: ......
Page 81: ......
Page 90: ...9 ...
Page 91: ...10 ...
Page 93: ...12 13 ...
Page 101: ...21 Maximum oil temperature with 80 F ambient temperature and no supplemental oil cooling ...
Page 102: ...22 ...
Page 105: ......
Page 120: ...RA 0165 0205 0255 0 0305 D Ref BMC Dwg T111 911 728 D 15 Fig 5 Exploded View Drawing of Pump ...