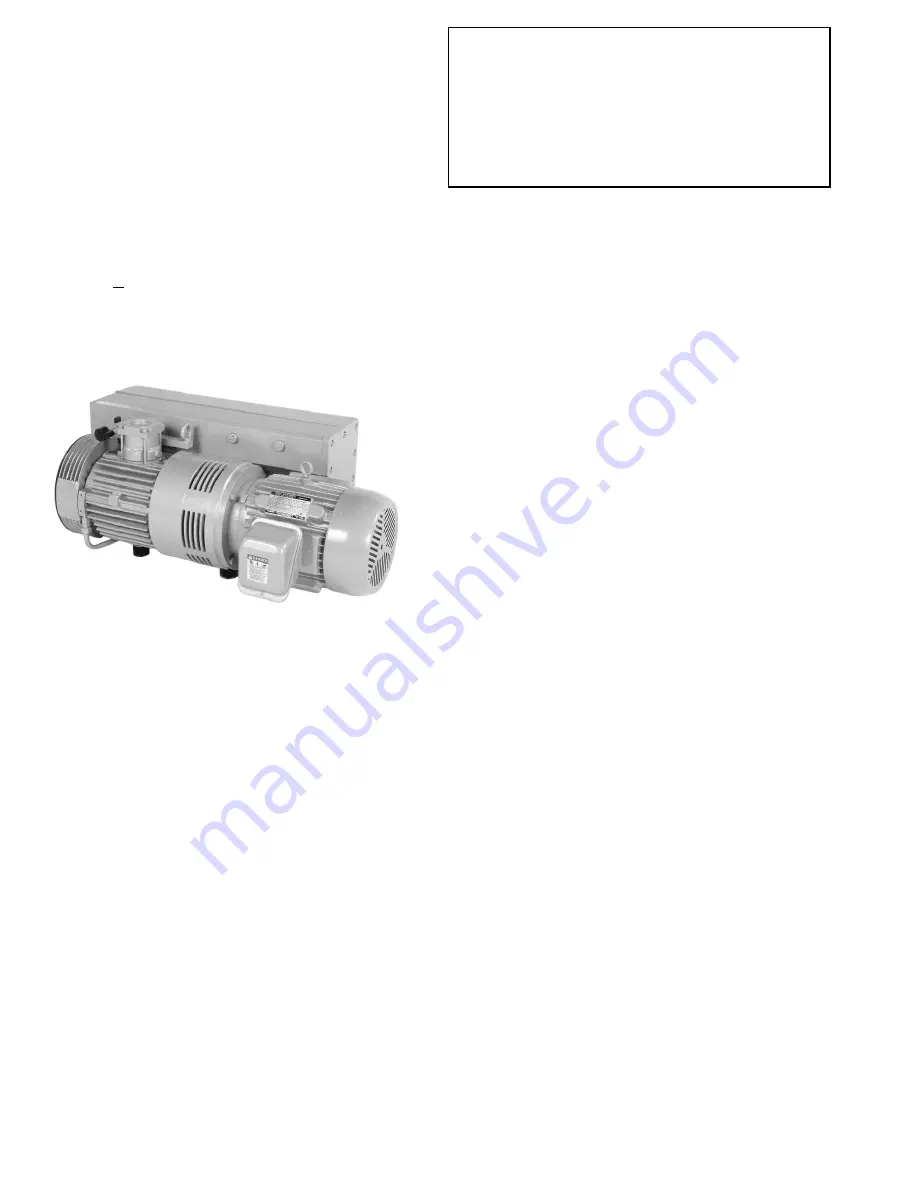
GENERAL
Identification
For model identification, see the nameplate mounted on
the side of the exhaust box.
This manual is written to cover installation and opera-
tion of the RA version of models 0165, 0205, 0255 and
0305 with a "D" appearing as the seventh character in
the model type number stamped into the nameplate.
For example it would appear as follows:
RA0XXX - DXXX - XXXX
When ordering parts, it is helpful to include the identifi-
cation code stamped into the side of the cylinder as well
as the serial number from the nameplate.
Operating Principles
All reference (Ref. XX) numbers listed in the text and on
illustrations throughout this manual are related to the
drawings and parts list near the end of this publication.
R 5 Series, Single Stage, Rotary Vacuum Pumps are
direct-driven, air-cooled, oil-sealed rotary vane pumps
which operate as positive displacement pumps (see
Fig. 1). They consist of a rotor positioned eccentrically
in a cylindrical stator (see Fig. 2). When the rotor spins,
centrifugal force pushes the vanes, which glide in slots,
towards the wall of the cylinder. The rotor has three
vanes which divide the pump chamber into three seg-
ments. The gas to be pumped enters at the inlet port,
passes through the inlet screen and the open anti-suck-
back valve into the pump chamber. As the rotor rotates,
the inlet aperture is closed, the gas is compressed and
forced out through one-way valves between the pump
cylinder and the exhaust box. Differential pressure con-
stantly causes oil to be pressed into the compression
chambers. The gas/oil mixture is separated by the dis-
charge filters (Ref. 120). The oil-free medium is dis-
charged through the exhaust cover plate (Ref. 140) to
atmosphere. This operation is repeated three times
each revolution.
1.0
INSTALLATION
1.1
Unpacking
Inspect the box and pump carefully for any signs of
damage incurred in transit. R 5 Pumps pass a rigorous
operating test in the factory and are packed carefully to
avoid transit damage. Since all pumps are ordinarily
shipped FOB our factory, such damage is the normal
responsibility of the carrier and should be reported to
them.
Remove any nuts from the bottom of the box/crate and
pull the pump out of the container using a suitable lifting
device and the lifting eye bolt (Ref. 391). Then,
unscrew any remaining studs that secured the bottom
of the rubber feet to the bottom of the crate.
The inlet port of the pump is covered with a plastic cap
prior to shipment to prevent dirt and other foreign mate-
rial from entering the pump. Do not remove this cover
until the pump is actually ready for connection to your
system.
1.2
Location
The pump must be installed in a horizontal position on
a level surface so that the pump is evenly supported on
its rubber feet. Allow sufficient air space between the
pump and any walls or other obstructions; adequate
ventilation must be provided for the fans on the pump
and motor (i.e., do not locate the pump in a stagnant air
location).
Whenever the pump is transported, be sure to drain the
oil prior to shipping to avoid vane breakage when
restarting the pump.
Do not tip the pump over if it is filled with oil.
Locate the pump for easy access to the oil sight glass
(Ref. 83) in order to inspect and control the oil level
properly. Allow clearance at the exhaust flange area to
provide service access to the exhaust filters.
1.3
Power Requirements
The schematic diagram for the electrical connection is
located in the junction box or on the nameplate of the
pump motor.
Fig. 1 - R 5 0255 D Pump
All R 5 series pumps are designed to handle air.
Vapor in the air stream can be tolerated when the
pump is operated within certain operating parameters
as defined by Busch, Inc. Engineering (see Section
2.2 - Gas Ballast). When you desire to use the pump
on an air stream that contains vapors, contact Busch,
Inc. Engineering for operating recommendations; oth-
erwise, the warranty could be void.
2
Summary of Contents for ULTRAVAC 2100
Page 2: ......
Page 81: ......
Page 90: ...9 ...
Page 91: ...10 ...
Page 93: ...12 13 ...
Page 101: ...21 Maximum oil temperature with 80 F ambient temperature and no supplemental oil cooling ...
Page 102: ...22 ...
Page 105: ......
Page 120: ...RA 0165 0205 0255 0 0305 D Ref BMC Dwg T111 911 728 D 15 Fig 5 Exploded View Drawing of Pump ...