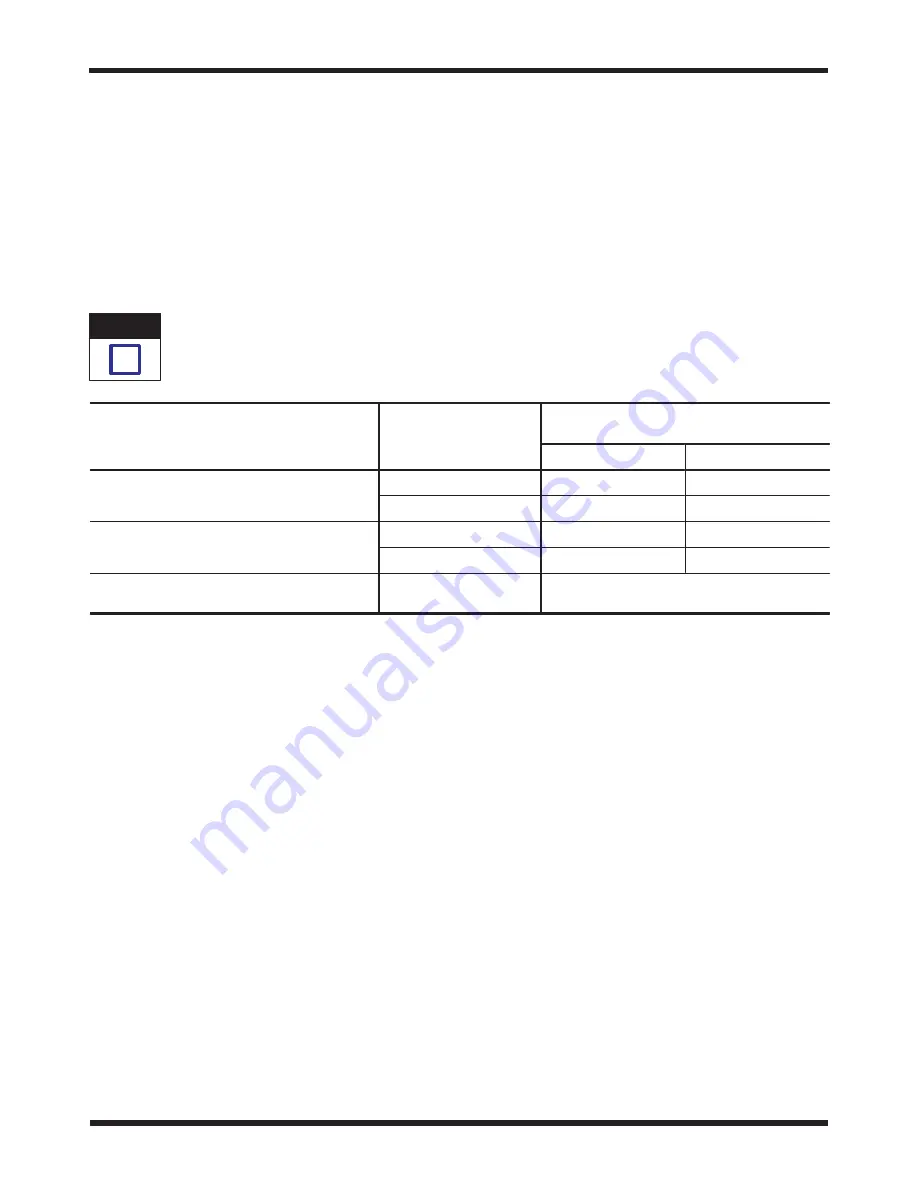
409-10042
DT-3000 Machines 1725100-[] and DT-5000 Machines 1725800-[]
Rev E
5 of 22
Tyco Electronics Corporation
2. DESCRIPTION
These machines were designed to be used as a stand–alone semi–automatic bench unit. It is assembled with
metric hardware.
A precision adjustment feature on the machine provides quick and accurate crimp height adjustments. The
batch counter provides a count of the terminations. A work light is included with the machine.
The base plate of Machines –6 and –7 also include a CQM sensor.
These machines accept a wide variety of miniature (mini) quick–change applicators, with minor adjustments,
thus providing a great selection of terminals for many applications. Figure 3 lists changeover cams required to
run 30–mm [1.181–in.] stroke cams (for AMP–O–LECTRIC* Model “K” terminating machines) and 41.28–mm
[1.625–in.] stroke cams (for Model “T” and Model “G” terminating machines) in these machines.
Some heavy-duty mini applicators require special cams that are not listed in Figure 3. Refer to the applicator logs
shipped with the applicators for additional information.
ORIGINAL APPLICATOR
FEED TYPE
CHANGEOVER CAMS
FOR DT-3000 AND DT-5000 MACHINES
ORIGINAL APPLICATOR
FEED TYPE
-2 and -6
-3 and -7
30-mm [1.181-in.] Stroke Applicator for
Pre-Feed
Ċ
690602-6
[
]
pp
Model K" Terminating Machine
Post-Feed
Ċ
690501-4
41.28-mm [1.625-in.] Stroke Applicator for
Pre-Feed
690602-5
Ċ
[
]
pp
Model T" and Model G" Terminating Machines
Post-Feed
690501-3
Ċ
Heavy-Duty Industrial (HD-I) Applicator
Pre-Feed/Post-Feed
Refer to the HD-I Applicator Customer Drawing
For Part Numbers
Figure 3
Quick–Disconnect Coupling 23238–1 is required to run air–feed applicators.
End–feed and side–feed miniature applicators are easily installed and removed without repositioning the
applicator mounting plate on the machine.
2.1. Functional Description
These machines provide the force required to crimp terminals in the applicator. A terminal is attached to the
wire by placing the wire in the crimp area and pressing the foot switch. The machine consists of four functional
areas:
1. The
motor group includes a dc motor which drives a crankshaft. The motor is activated each cycle
and rotates the crankshaft one full revolution. A motor access cover, located on the end of the motor,
covers a hex key which allows the motor to be cycled manually. See Figure 4.
2. The
crankshaft–ram group covers the motor rotational force to the up–and–down action of the ram
for driving the applicator during the crimping cycle.
3. The
base plate provides the mounting surface on which the applicator is installed. The quick–release
latching feature on Machines –2, –3, –4, –6, and –7 permits fast, easy installation and removal of the
applicator. Note that Machines –1 and –5 do not include the quick–release latching feature.
See Figure 5.
4. The
crimp height adjustment group uses an eccentric located in the ram linkage, along with
detented stops in the mechanism to adjust the crimp height. See Figure 5. Indexing the mechanism in
either direction will change the crimp height in increments of approximately 0.013 mm [.0005 in.] per
step.
NOTE
i