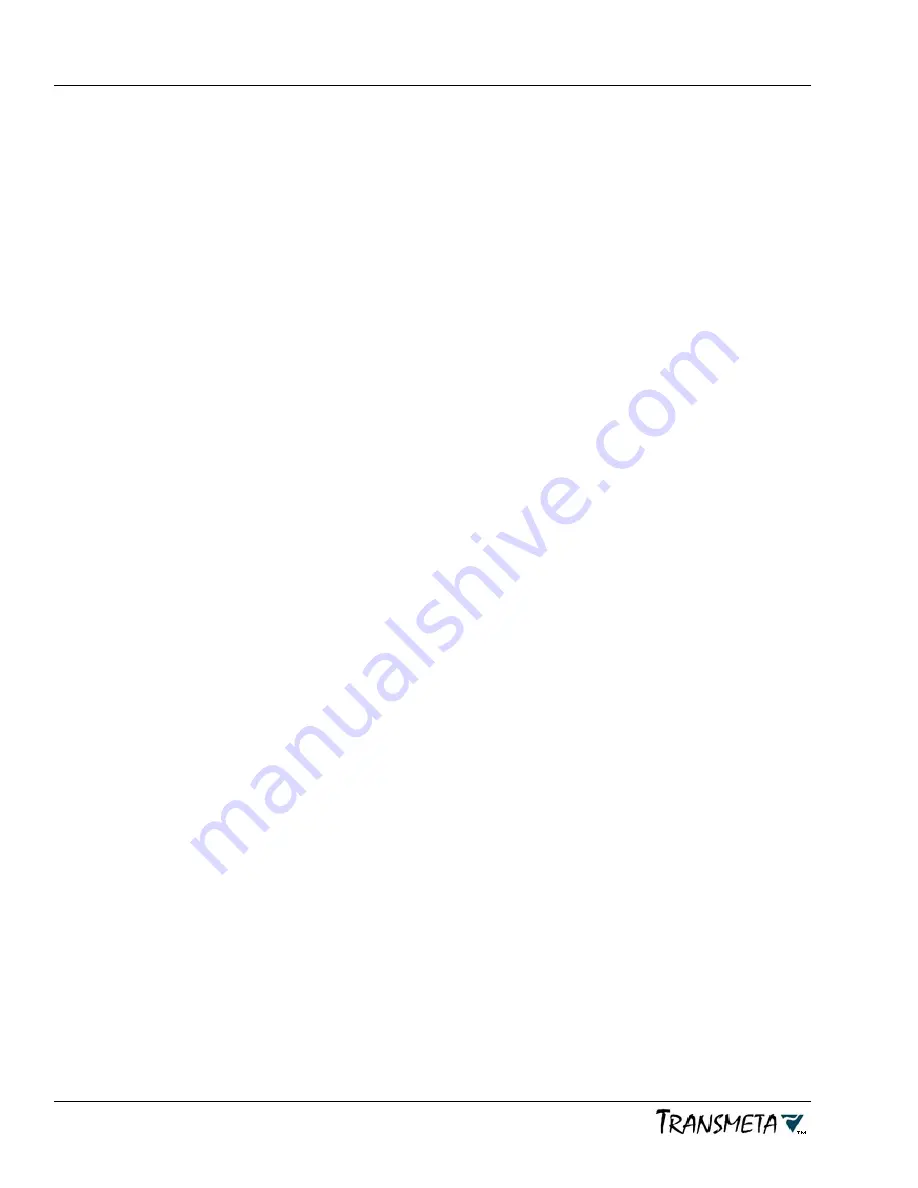
July 17, 2002
104
System Design Considerations
6.8.2 Thermal Sensor Issues
As mentioned, the thermal sensor chip generates a bias current for the diode. This current is on the order of
10-200 nA. This current is carried along the interconnect circuitry to the diode.
On the way from the sensor to the diode (and back again) the current encounters two major sources of noise:
•
Crosstalk from adjacent high-speed circuits. The EM fields of nearby circuits can couple inductively into
the thermal connector wiring, causing voltage noise on the circuit.
•
Leakage currents from power, ground, or signal circuits. There is always some surface resistance on a
PCB board in the order of 10 M
Ω
or more. This means that some leakage current is always present, but
is small relative to the current on the sensor. However, surface contamination local to the thermal sensor
circuit can lower the surface resistance to 10-100 K
Ω
. This creates a much larger leakage current. If the
source of the current is a power rail, the result is a fairly constant offset of the temperature from the
correct reading.
The thermal connection does allow for a low-pass filter (a 2200 pF capacitor) to filter out some of the
noise. However, this is not sufficient to ensure a good reading. It is necessary to lay the board out so that
the opportunities for noise to enter the circuit are eliminated, or at least minimized.
6.8.3 Thermal Sensor Layout
There are a number of rules to ensure minimal noise in the thermal sensor circuits:
•
Minimize the distance from the processor to the sensor chip.
This rule minimizes crosstalk because the parallelism with other lines is reduced, and the area of the
inductive loop of the circuit is also at a minimum. The opportunities for that area of the system board to
become contaminated are also kept to a minimum. If possible, place the sensor chip
directly adjacent
to
the processor.
•
Route the sensor lines as a differential pair.
A differential pair is a structure that places the signal and its complement directly adjacent to each other.
Route the anode and cathode connections as close as the PCB manufacturing process will allow, 0.004-
0.005” is reasonable for most fabricators. Follow this structure from the point that the two signals emerge
from the sensor chip to the point the signals enter the processor. Any electromagnetic disturbance that
the two lines are subjected to should be rejected by the sensor chip as common-mode noise.
•
Route the circuit on internal layers.
This allows the power planes to act as a shield. If possible, have a layer reserved for sensitive circuitry.
Do not run digital lines on the layer adjacent to the thermal circuit.
•
Use guard traces.
Surround the differential pair with a copper trace connected every 0.250” to ground. Do this on ALL
layers, not just the routing layers. This serves two purposes:
›
Any leakage current that does occur is shorted to ground.
›
It ensures extra distance from noisy circuits to the thermal circuit.
•
Keep signal traces away from the thermal circuit.
Summary of Contents for Crusoe TM5500
Page 1: ...TM5500 TM5800 System Design Guide July 17 2002...
Page 6: ...July 17 2002 6 List of Tables...
Page 8: ...July 17 2002 8 List of Figures...
Page 50: ...July 17 2002 50 Processor Power Supplies and Power Management...
Page 110: ...July 17 2002 110 System Design Considerations...
Page 122: ...July 17 2002 122 System Design Checklists...
Page 128: ...July 17 2002 128 Serial Write protection PLD Data...
Page 130: ...July 17 2002 130 Index...