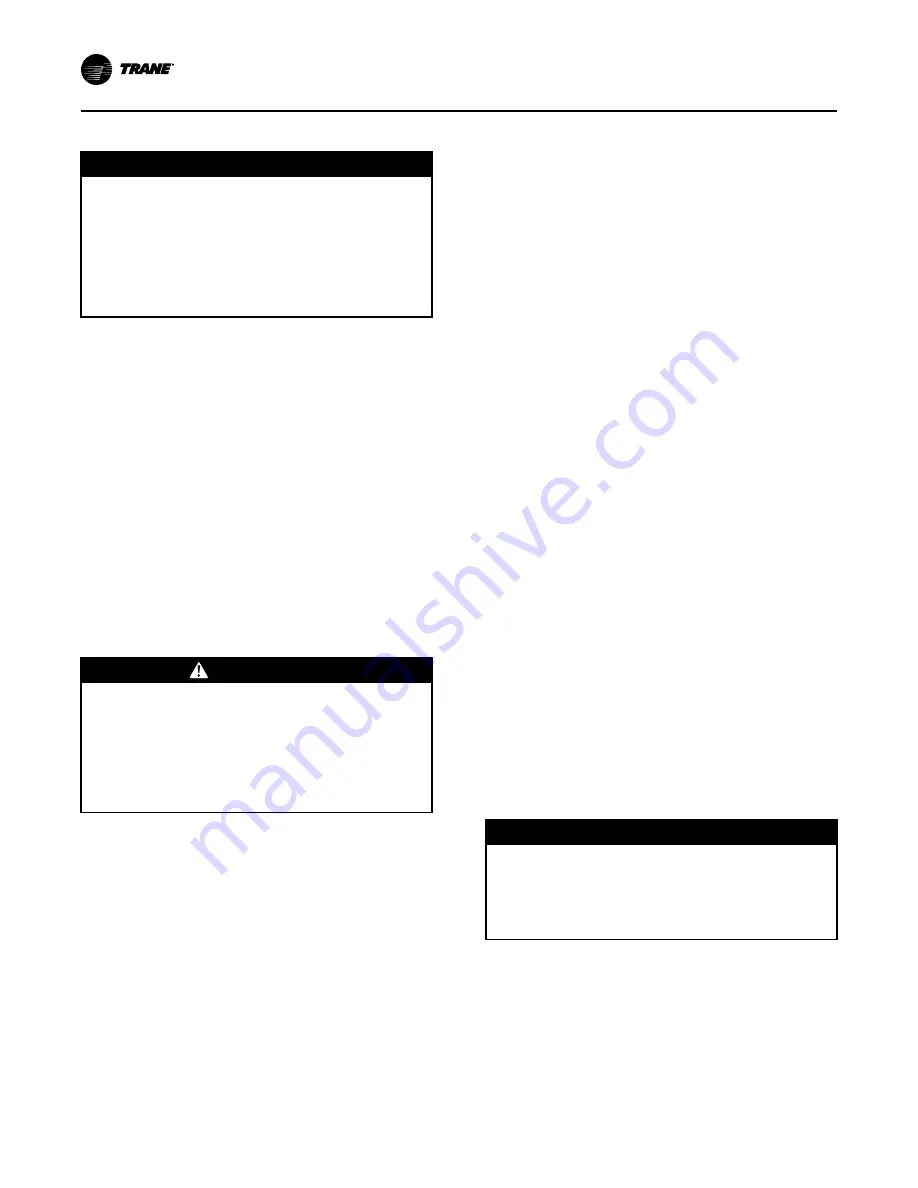
120
SS-SVX11K-EN
Coil Cleaning
N
NO
OT
TIIC
CE
E
D
Da
am
ma
ag
giin
ng
g C
Co
oiill C
Clle
ea
an
ne
errss!!
C
Co
oiill cclle
ea
an
ne
errss cca
an
n d
da
am
ma
ag
ge
e rro
oo
offss,, ssu
urrrro
ou
un
nd
diin
ng
g
b
bu
uiilld
diin
ng
gss,, v
ve
eh
hiicclle
ess,, e
ettcc..
C
Clle
ea
an
niin
ng
g ssu
ub
bsstta
an
ncce
ess ssh
ho
ou
ulld
d b
be
e cch
he
ecckke
ed
d tto
o e
en
nssu
urre
e
tth
ha
att tth
he
ey
y w
wiillll n
no
ott cca
au
usse
e d
da
am
ma
ag
ge
e tto
o ssu
urrrro
ou
un
nd
diin
ng
gss..
C
Co
oiillss a
an
nd
d rro
oo
off ((iiff a
ap
pp
plliicca
ab
blle
e)) ssh
ho
ou
ulld
d b
be
e rriin
nsse
ed
d
tth
ho
orro
ou
ug
gh
hlly
y.. D
Do
o n
no
ott ssp
prra
ay
y cco
oiill cclle
ea
an
ne
errss iin
n w
wiin
nd
dy
y
cco
on
nd
diittiio
on
nss..
Regular coil maintenance, including annual cleaning,
enhances unit’s operating efficiency by minimizing:
•
compressor head pressure and amperage draw;
•
water carryover;
•
fan brake horsepower; and,
•
static pressure losses.
At least once each year—or more often if the unit is
located in a “dirty” environment—clean the
microchannel condenser using the instructions
outlined below. Be sure to follow these instructions as
closely as possible to avoid damaging the coils.
To clean refrigerant coils, use a soft brush and a
sprayer.
N
No
otte
e:: DO NOT use any detergents with microchannel
condenser coils. Pressurized water or air ONLY.
1. Remove enough panels from the unit to gain safe
access to coils..
W
WA
AR
RN
NIIN
NG
G
N
No
o S
Stte
ep
p S
Su
urrffa
acce
e!!
F
Fa
aiillu
urre
e tto
o ffo
ollllo
ow
w iin
nssttrru
uccttiio
on
n b
be
ello
ow
w cco
ou
ulld
d rre
essu
ulltt iin
n
d
de
ea
atth
h o
orr sse
erriio
ou
uss iin
njju
urry
y..
D
Do
o n
no
ott w
wa
allkk o
on
n tth
he
e ssh
he
ee
ett m
me
etta
all d
drra
aiin
n p
pa
an
n.. W
Wa
allkkiin
ng
g
o
on
n tth
he
e d
drra
aiin
n p
pa
an
n cco
ou
ulld
d cca
au
usse
e tth
he
e ssu
up
pp
po
orrttiin
ng
g m
me
etta
all
tto
o cco
olllla
ap
psse
e a
an
nd
d rre
essu
ulltt iin
n tth
he
e o
op
pe
erra
atto
orr//tte
ecch
hn
niicciia
an
n
ffa
alllliin
ng
g..
IIm
mp
po
orrtta
an
ntt:: Bridging between the main supports
required before attempting to enter into
the unit. Bridging may consist of
multiple 2 by 12 boards or sheet metal
grating.
2. Straighten any bent coil fins with a fin comb.
3. For accessible areas, remove loose dirt and debris
from both sides of the coil. For dual row
microchannel condenser coil applications, seek
pressure coil wand extension through the local
Trane Parts Center.
N
No
otte
e:: DO NOT use any detergents with
microchannel coils. Pressurized water or air
ONLY.
4. Pour the cleaning solution into the sprayer. If a
high-pressure sprayer is used:
a. The minimum nozzle spray angle is 15 degrees.
b. Do not allow sprayer pressure to exceed 600 psi.
c. Spray the solution perpendicular (at 90 degrees)
to the coil face.
5. Spray the leaving-airflow side of the coil first; then
spray the opposite side of the coil. For evaporator
and reheat coils, allow the cleaning solution to
stand on the coil for five minutes.
6. Rinse both sides of the coil with cool, clean water.
7. Inspect both sides of the coil; if it still appears to be
dirty, repeat Steps 6 and 7.
8. Reinstall all of the components and panels removed
in Step 1; then restore power to the unit.
9. For evaporator and reheat coils, use a fin comb to
straighten any coil fins which were inadvertently
bent during the cleaning process.
Microchannel Condenser Coil Repair and
Replacement
If microchannel condenser coil repair or replacement is
required, see Service Guide document RT-SVB83*-EN
for further details.
EVP Remote Evaporator Chiller
The brazed plate evaporator is difficult to clean should
it become plugged with debris so proper installation
and maintenance of the inlet water strainer is
important. Particles larger than 0.039” entering the
heat exchanger could block flow passages causing a
failure. Indications of a plugged BPHE evaporator
include “wet” suction due to lack of heat exchange,
loss of superheat control, depressed discharge
superheat (superheat less than 63°F), compressor oil
dilution and/or starvation and premature compressor
failure.
Minimum water flow rate must be maintained to avoid
laminar flow, potential evaporator freezing, scaling and
poor temperature control.
N
NO
OT
TIIC
CE
E
H
He
ea
att E
Ex
xcch
ha
an
ng
ge
err D
Da
am
ma
ag
ge
e!!
F
Frre
ee
ezziin
ng
g a
an
nd
d h
he
ea
att e
ex
xcch
ha
an
ng
ge
err d
da
am
ma
ag
ge
e cco
ou
ulld
d o
occccu
urr
iiff w
wa
atte
err ffllo
ow
w iiss iin
ntte
errrru
up
ptte
ed
d..
D
Do
o n
no
ott sstto
op
p w
wa
atte
err ffllo
ow
w w
wiitth
h tth
he
e rre
effrriig
ge
erra
attiio
on
n
ssy
ysstte
em
m rru
un
nn
niin
ng
g..
Maximum water flow rate must not be exceeded to
avoid possible erosion.
Water Strainer Maintenance
To protect the evaporator and for maximum efficiency,
the strainer must be cleaned. A differential pressure
gauge installed across the inlet and outlet will indicate
pressure loss due to clogging and may be used as a
guide to determine when cleaning is required.