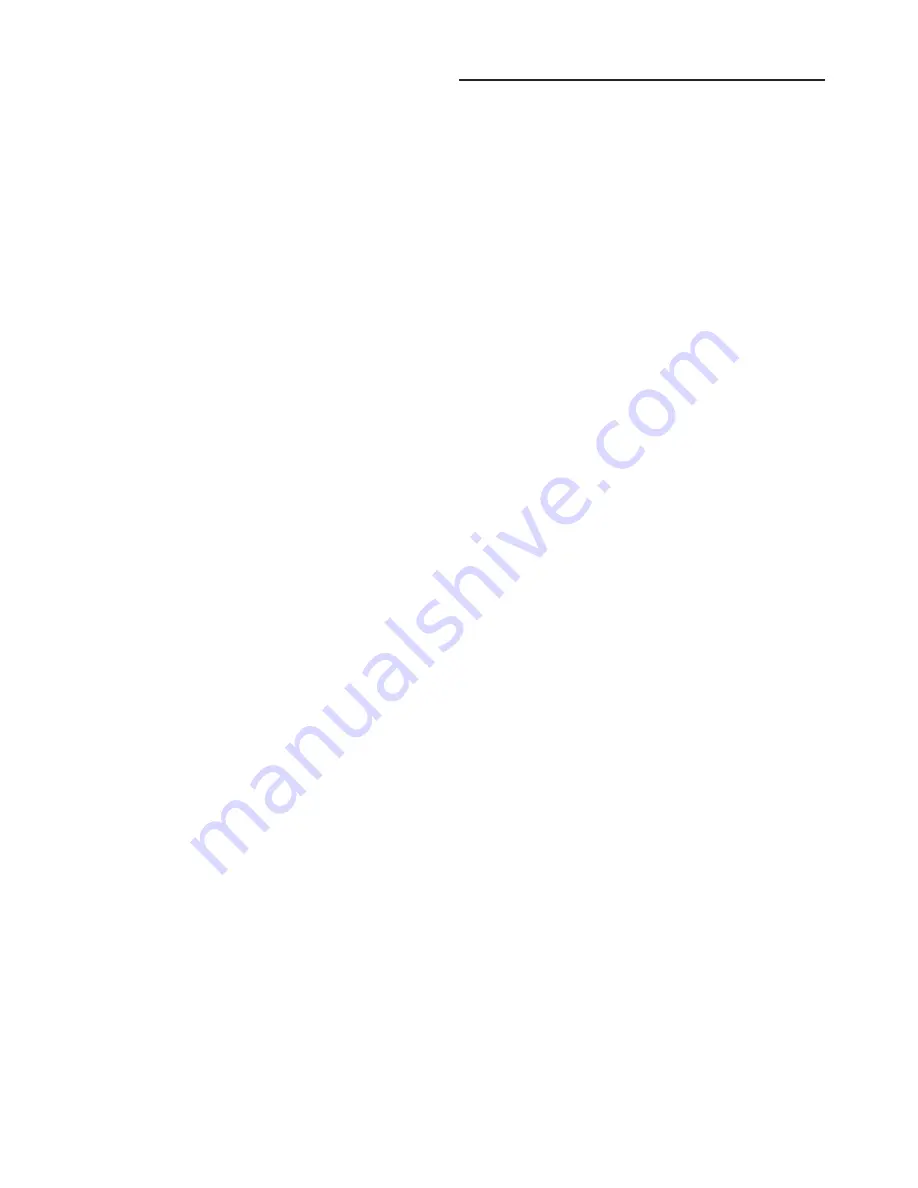
7
General Information
UCM Control System
Trane Large Commercial Cold Generator Units are con-
trolled by a microelectronic control system that consists of a
network of modules and are referred to as Unit Control
Modules (UCM).
The unit size, peripheral devices, options, etc... determine
the number and type of modules that a particular unit may
employ.
The UCM receives analog and binary inputs, then pro-
cesses this information and supplies outputs in the form of
modulating voltages, contact closures, etc... to control
damper actuators, fan motors, compressors, valves, and
other electrical devices in the system to maintain set tem-
perature levels.
The UCM provides some equipment protection functions
both directly and indirectly, such as chilled water flow and
compressor lockouts.
Listed below are the various modules that may be em-
ployed in a UCM control system.
Cold Generator Module (1U48) (CGM - Standard)
The Cold Generator Module (CGM) responds to cooling re-
quests by energizing the proper unit components based on
information received from other unit modules, sensors, re-
mote panels, and customer supplied binary inputs. It ini-
tiates unit operation based on that information.
Compressor Module (1U49) (MCM)
The Compressor module, (Single Circuit & Multiple Circuit),
upon receiving a request for mechanical cooling, energizes
the appropriate compressors and condenser fans. It moni-
tors the compressor operation through feedback information
it receives from various protection devices. It also provides
heat tape output control for heat exchanger protection.
Interprocessor Communications Board (1U55) (IPCB -
used with Optional Remote Human Interface)
The Interprocessor Communication Board expands commu-
nications from the unit’s UCM network to a Remote Human
Interface Panel. DIP switch settings on the IPCB module for
this application should be; Switches 1 and 2 “Off”, Switch 3
“On”.
Trane Communications Interface Module (1U54) (TCI -
Optional - used with Trane ICS
™
)
The Trane Communication Interface module expands com-
munications from the unit’s UCM network to a Trane Tracer
100
™
or a Tracer Summit
™
system and allows external
setpoint adjustment and monitoring of status and diagnos-
tics.
DIP Switch settings on the TCI module for these applica-
tions should be:
Switches 1, 2, and 3 are “Off”
Generic Building Automation System Module (1U51 =
GBAS 0-5V, 1U98 = GBAS 0-10V) (Optional - used with
Non-Trane Building Control System)
The Generic Building Automation System (GBAS) module
allows a non-Trane building control system to communicate
with the unit and accepts external setpoints in form of ana-
log inputs (0 - 5 DCV or 0 - 10 DCV depending on the mod-
ule selected) and a binary Input for demand limit. Five (5)
binary outputs are available on 0 - 5 DCV modules. One (1)
binary output and four (4) analog outputs are available on
the 0 - 10 DCV modules. Refer to the “Field Installed Con-
trol Wiring” section for the control wiring to the GBAS mod-
ule and the various desired setpoints with the correspond-
ing DC voltage inputs.
Lontalk Communication Interface Module (1U54)
(LCI Optional - used on units with Trane ICS
™
or 3rd party
Building Automation Systems)
The LonTalk Communication Interface module expands
communications from the unit’s UCM network to a Trane
Tracer Summit
™
or a 3rd party building automation system,
that utilizes LonTalk, and allows external setpoint and con-
figuration adjustment and monitoring of status and diag-
nostics.
Current Sensing Module (1U90) (CSM - Optional)
Current transformers located around two (2) of the main
power leads for each compressor monitors the running cur-
rent during compressor operation. The information is sent to
the UCM and can be accessed through the “Compressor
Status” submenu displayed at the Human Interface Module.
Superheat & Subcooling Module (1U91) (SSM -
Optional)
Monitors the system operating superheat and subcooling
through the use of pressure transducers, liquid line, and
suction line temperature sensors. The information is sent to
the SSM and can be accessed through the “Compressor
Status” submenu displayed at the Human Interface Module.
Power Disconnecting Switches
Manual Disconnect Switch
(Optional 1S14) Manual disconnect switch 1S14, located in
the unit control panel, instead of the power terminal block
1TB1, allows the operator to disconnect power from the
unit's “high” voltage (200V-575V) section, the 115V section,
and the 24V section without having to open the control
panel door. A description of its features and operation are
given in the Installation, Operation, & Maintanence manual.
115V Control Circuit Switch (1S1)
Control circuit switch (1S1) is provided on all units and is lo-
cated downstream of the 115V transformer 1T1. It allows
the operator to disconnect power from the unit's 115V con-
trol components by placing the switch in the "Off" position.
24V Transformer Switch (1S70)
Transformer switch 1S70 is provided on all units and is lo-
cated downstream of 24V transformers 1T2 and 1T3. It al-
lows the operator to disconnect (24V) power from all of the
unit's control modules by placing the switch in the "Off" po-
sition.
For a complete description of the 24V components and op-
eration, refer to the latest edition of the applicable Installa-
tion, Operation and Maintenance manual listed on the unit
nameplate.
Summary of Contents for IntelliPak CGAF Series
Page 68: ...68...