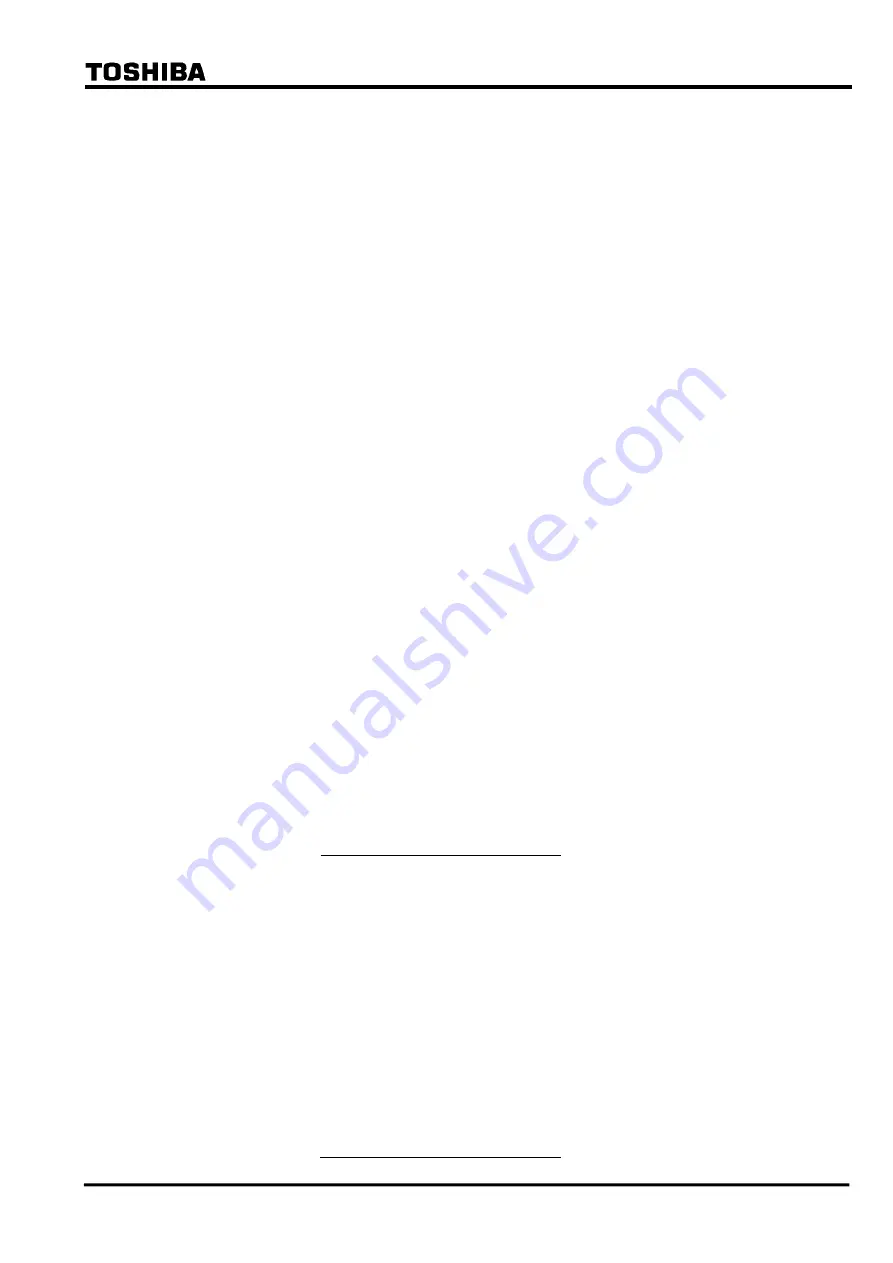
⎯
218
⎯
6
F
2
S
0
8
3
5
If no message is shown on the LCD, it means that the failure location is either in the DC power
supply circuit or in the microprocessors mounted on the SPM module. In this case, check the
"ALARM" LED. If it is off, the failure is in the DC power supply circuit. If it is lit, open the relay
front panel and check the LEDs mounted on the SPM module. If the LED is off, the failure is in
the DC power supply circuit. If the LED is lit, the failure is in the microprocessors.
In the former case, check if the correct DC voltage is applied to the relay.
If so, replace the IO1 or IO8 module mounting the DC/DC converter and confirm that the
"ALARM" LED is turned off.
In the latter case, replace the SPM module mounting the processors and confirm that the
"ALARM" LED is turned off.
When a failure is detected during regular testing, it will not be difficult to identify the failed
module to be replaced.
Note: When a failure or an abnormality is detected during the regular test, confirm the following
first:
- Test circuit connections are correct.
- Modules are securely inserted in position.
- Correct DC power voltage with correct polarity is applied and connected to the correct
terminals.
- Correct AC inputs are applied and connected to the correct terminals.
- Test procedures comply with those stated in the manual.
6.7.3 Replacing Failed Modules
If the failure is identified to be in the relay module and the user has spare modules, the user can
recover the protection by replacing the failed modules.
Repair at the site should be limited to module replacement. Maintenance at the component level
is not recommended.
Check that the replacement module has an identical module name (VCT, SPM, IO1, IO2, etc.)
and hardware type-form as the removed module. Furthermore, the SPM and FD modules should
have the same software name.
The module name is indicated on the bottom front of the relay case. The hardware type-form is
indicated on the module in the following format:
Module name Hardware type-form
VCT
G1PC1 -
∗∗∗∗
SPM
G1SP
∗
-
∗∗∗∗
IO1
G1IO1 -
∗∗∗∗
IO2
G1IO2 -
∗∗∗∗
IO3
G1IO3 -
∗∗∗∗
IO4
G1IO2 -
∗∗∗∗
IO5
G1IO3 -
∗∗∗∗
IO6
G1IO3 -
∗∗∗∗
IO8
G1IO8 -
∗∗∗∗
FD
G1FD1 -
∗∗∗∗
HMI ----
Summary of Contents for GRL100-101A
Page 223: ... 222 6 F 2 S 0 8 3 5 ...
Page 228: ... 227 6 F 2 S 0 8 3 5 Appendix B Signal List ...
Page 256: ... 255 6 F 2 S 0 8 3 5 Appendix C Variable Timer List ...
Page 258: ... 257 6 F 2 S 0 8 3 5 Appendix D Binary Output Default Setting List ...
Page 269: ... 268 6 F 2 S 0 8 3 5 ...
Page 270: ... 269 6 F 2 S 0 8 3 5 Appendix E Details of Relay Menu ...
Page 279: ... 278 6 F 2 S 0 8 3 5 ...
Page 288: ... 287 6 F 2 S 0 8 3 5 Appendix G Typical External Connection ...
Page 326: ... 325 6 F 2 S 0 8 3 5 Appendix J Return Repair Form ...
Page 330: ... 329 6 F 2 S 0 8 3 5 Customer Name Company Name Address Telephone No Facsimile No Signature ...
Page 331: ... 330 6 F 2 S 0 8 3 5 ...
Page 332: ... 331 6 F 2 S 0 8 3 5 Appendix K Technical Data ...
Page 343: ... 342 6 F 2 S 0 8 3 5 ...
Page 344: ... 343 6 F 2 S 0 8 3 5 Appendix L Symbols Used in Scheme Logic ...
Page 347: ... 346 6 F 2 S 0 8 3 5 ...
Page 348: ... 347 6 F 2 S 0 8 3 5 Appendix M Multi phase Autoreclose ...
Page 351: ... 350 6 F 2 S 0 8 3 5 ...
Page 352: ... 351 6 F 2 S 0 8 3 5 Appendix N Data Transmission Format ...
Page 358: ... 357 6 F 2 S 0 8 3 5 Appendix O Example of DIF and DIFG Setting ...
Page 364: ... 363 6 F 2 S 0 8 3 5 Appendix Q IEC60870 5 103 Interoperability ...
Page 377: ... 376 6 F 2 S 0 8 3 5 ...
Page 378: ... 377 6 F 2 S 0 8 3 5 Appendix R Failed Module Tracing and Replacement ...
Page 384: ... 383 6 F 2 S 0 8 3 5 Appendix S PLC Setting Sample ...
Page 386: ... 385 6 F 2 S 0 8 3 5 Appendix T Ordering ...
Page 392: ......