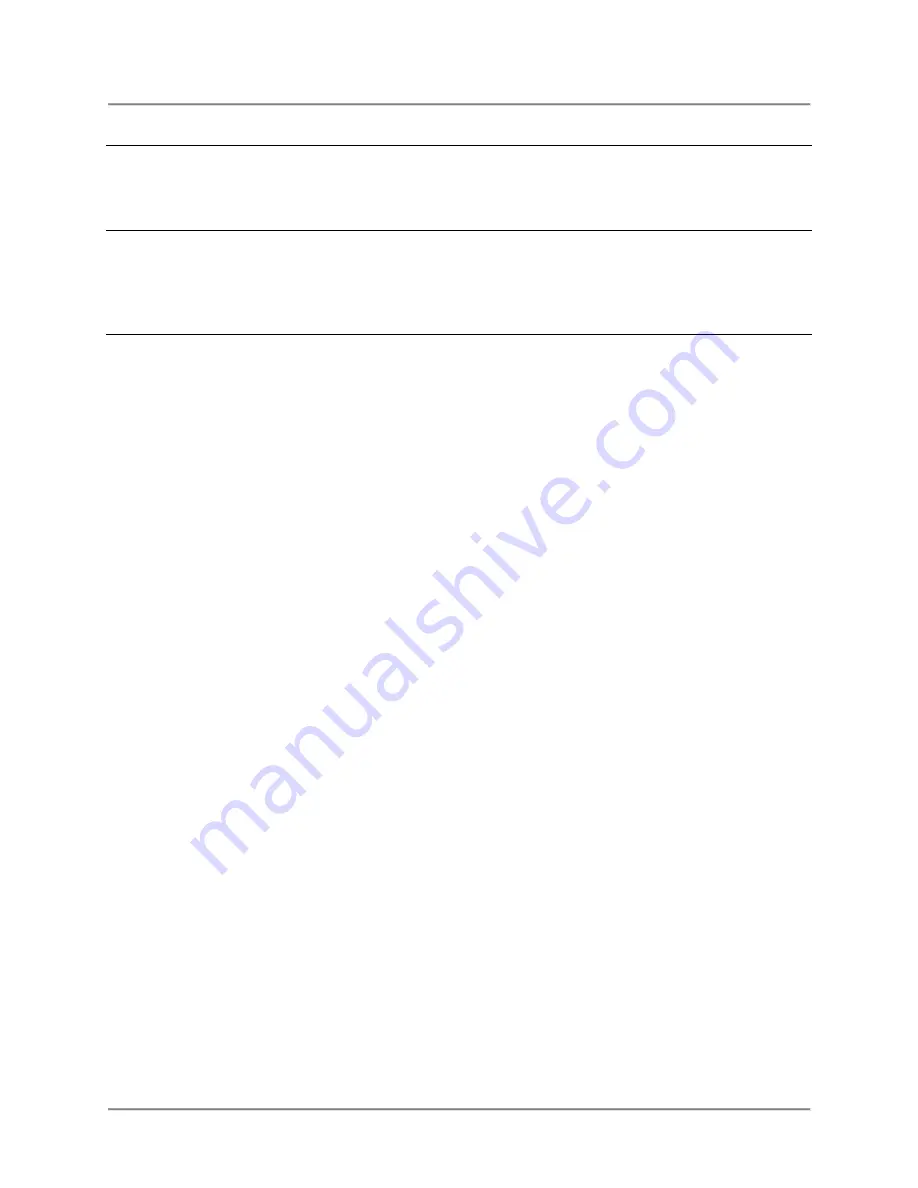
- 4 -
Section
Page
7.
TROUBLESHOOTING
7.1 General Information ........................................................................................................................... 81
7.2 Monitored Errors ................................................................................................................................ 81
7.3 Retort Fill Error ................................................................................................................................... 81
8.
SERVICE AND REPLACEMENT PARTS
8.1 Service Information ............................................................................................................................ 91
8.2 Replacement Accessory Items ........................................................................................................... 91
8.3 Replacement Parts ............................................................................................................................. 91
8.4 Tissue-Tek VIP AI Preservice Checklist ............................................................................................... 92
9.
EXAMPLE PROCESSING
9.1 Sample Programs ............................................................................................................................... 93
Summary of Contents for VIP 6 AI
Page 1: ...Operating Manual Tissue TekVIP 6 AI Vacuum Infiltration Processor...
Page 2: ...O p e r a t i n g M a n u a l Vacuum Infiltration Processor Tissue Tek VIP 6 AI...
Page 3: ...1...
Page 74: ...72...
Page 98: ...96...