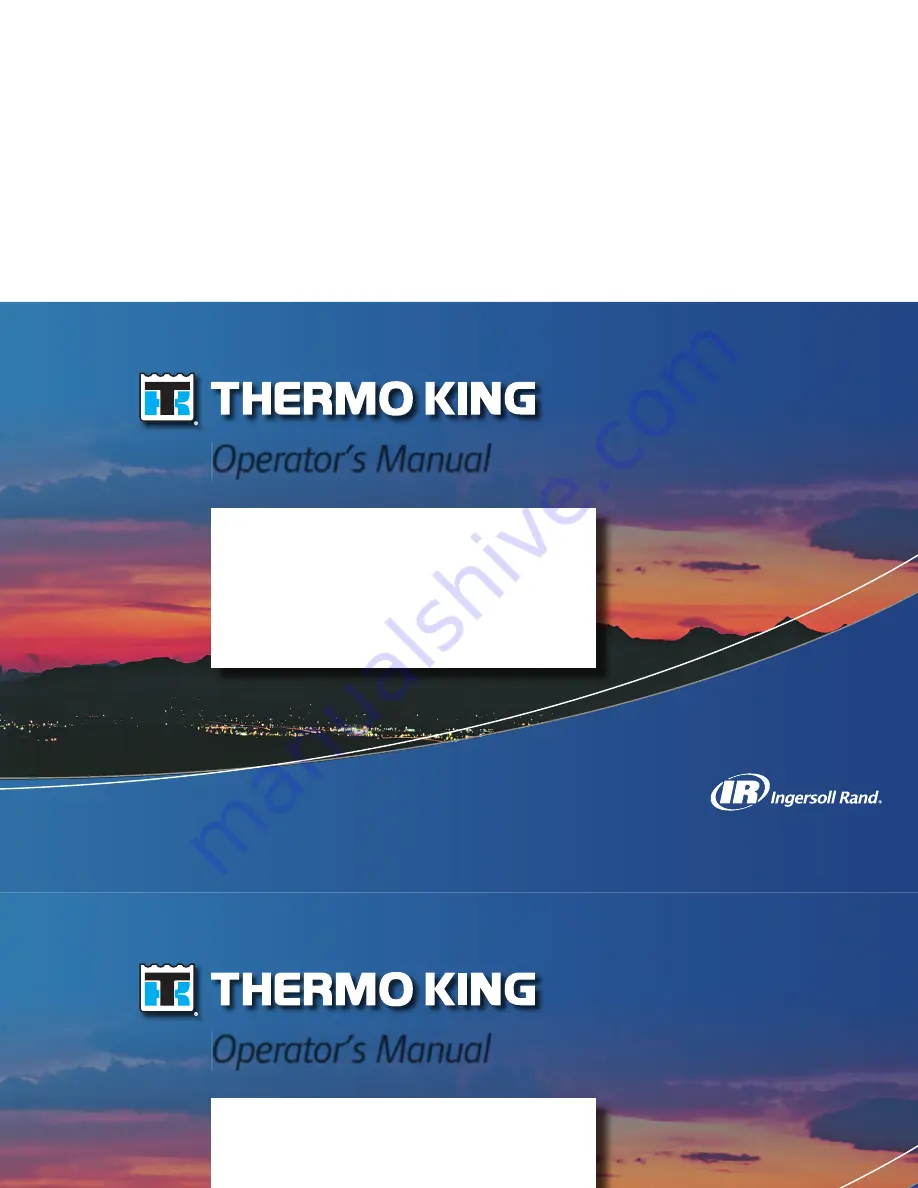
Operator’s Manual
Ingersoll Rand’s Climate Solutions sector delivers energy-effi cient HVACR solutions for
customers globally. Its world class brands include Thermo King, the leader in transport
temperature control and Trane, a provider of energy effi cient heating, ventilating and
air conditioning systems, building and contracting services, parts support and advanced
controls for commercial buildings and homes.
©2011 Ingersoll-Rand Company
Printed in U.S.A.
SB-200TG
TK 53598-2-OP (Rev. 0, 02/07)
Operator’s Manual
Ingersoll Rand’s Climate Solutions sector delivers energy-effi cient HVACR solutions for
customers globally. Its world class brands include Thermo King, the leader in transport
temperature control and Trane, a provider of energy effi cient heating, ventilating and
air conditioning systems, building and contracting services, parts support and advanced
controls for commercial buildings and homes.
©2011 Ingersoll-Rand Company
Printed in U.S.A.
SB-200TG
TK 53598-2-OP (Rev. 0, 02/07)
Summary of Contents for SB-200TG
Page 1: ...Operator s Manual SB 200TG Operator s Manual SB 200TG TK 53598 2 OP Rev 0 02 07...
Page 7: ...6 Table of Contents 6...
Page 11: ...10 Introduction 10...
Page 21: ...20 EPA Emission Control System Warranty Statement 20...
Page 43: ...42 TG VI Controller Description 42...
Page 45: ...44 Remote Status Light Optional 44...
Page 83: ...82 Alarm Codes 82...
Page 103: ...102 Warranty 102...
Page 117: ...116 Serial Number Locations 116...