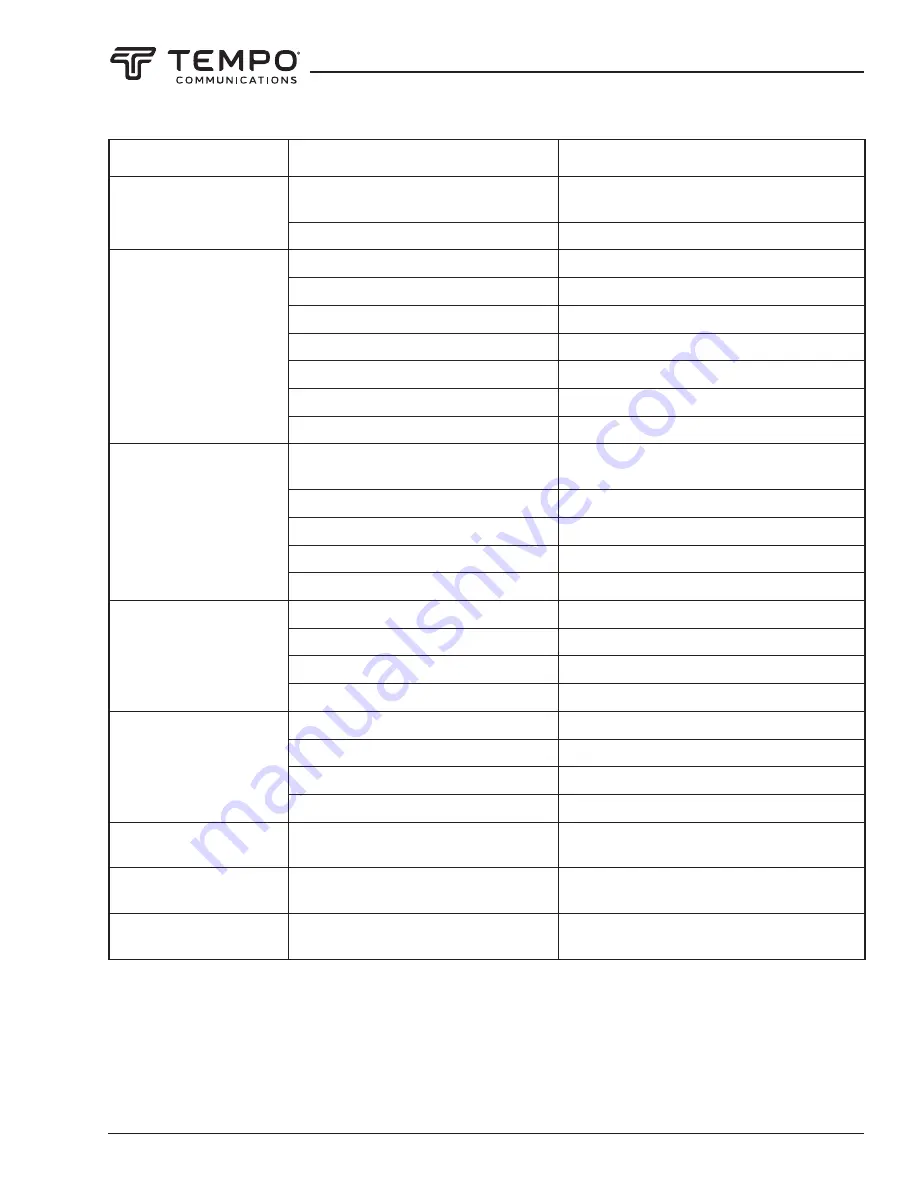
FSP200
33
Tempo Communications Inc.
1390 Aspen Way • Vista, CA 92081 USA • 800-642-2155
Error Message
Reason
Solution
Display “Wait Download..”
ON/OFF and ENTER buttons are held at the
same time.
Power off. Power back on.
Component damage – keypad.
Keypad replacement required.
LEFT_FIBER_DIRTY
RIGHT_FIBER_DIRTY
LR_FIBER_DIRTY
Fibers are dirty.
Clean fiber and recleave.
V-grooves are dirty.
Clean V-grooves.
V-grooves are damaged.
V-grooves need to be factory replaced.
Fiber presser foot is dirty.
Clean presser foot of FSP200.
Fiber adapters are dirty.
Clean fiber adapters.
Mirrors are dirty.
Clean mirrors .
Lenses are dirty.
Clean lenses.
LR_ARC_VALUE_ERR
Fibers are dirty, passing the limit of
checking process.
Clean fiber and recleave.
Cleave angle is too big.
Recleave fibers to obtain good cleave angle.
Failure to do the arc calibration.
Do arc calibration.
Electrodes are oxidized.
Clean electrodes or replace with a new pair.
Lenses are dirty.
Clean lenses.
FIBER_PUSH_ERR
Fiber is not in V-groove.
Replace fiber and check if fiber is in the V-groove.
Fiber holder is not tight.
Reposition the fiber.
Backward tension is on fiber.
Release any tension on fiber.
The adapter holder is dirty.
Clean the fiber adapter holder.
ARC_OFFSET_TOO_LARGE
Failure to do the arc calibration.
Do arc calibration.
Electrodes position error.
Check and or replace electrodes.
Electrodes are broken.
Replace electrodes.
Electrodes are oxidized.
Replace electrodes.
LENS_OFFSET_TOO_LARGE
Fiber is beyond observation range.
Perform “Screen Adjust” to allow fibers to be
displayed on the screen.
COVER_OPEN when the
windshell is closed
The magnet on windshell is missing.
Magnet needs to be factory replaced.
Notified to replace
electrodes
Electrodes require calibration or
replacement.
Stabilize electrodes as per Menu 3; replace
electrodes.
Error Messages
(cont’d)