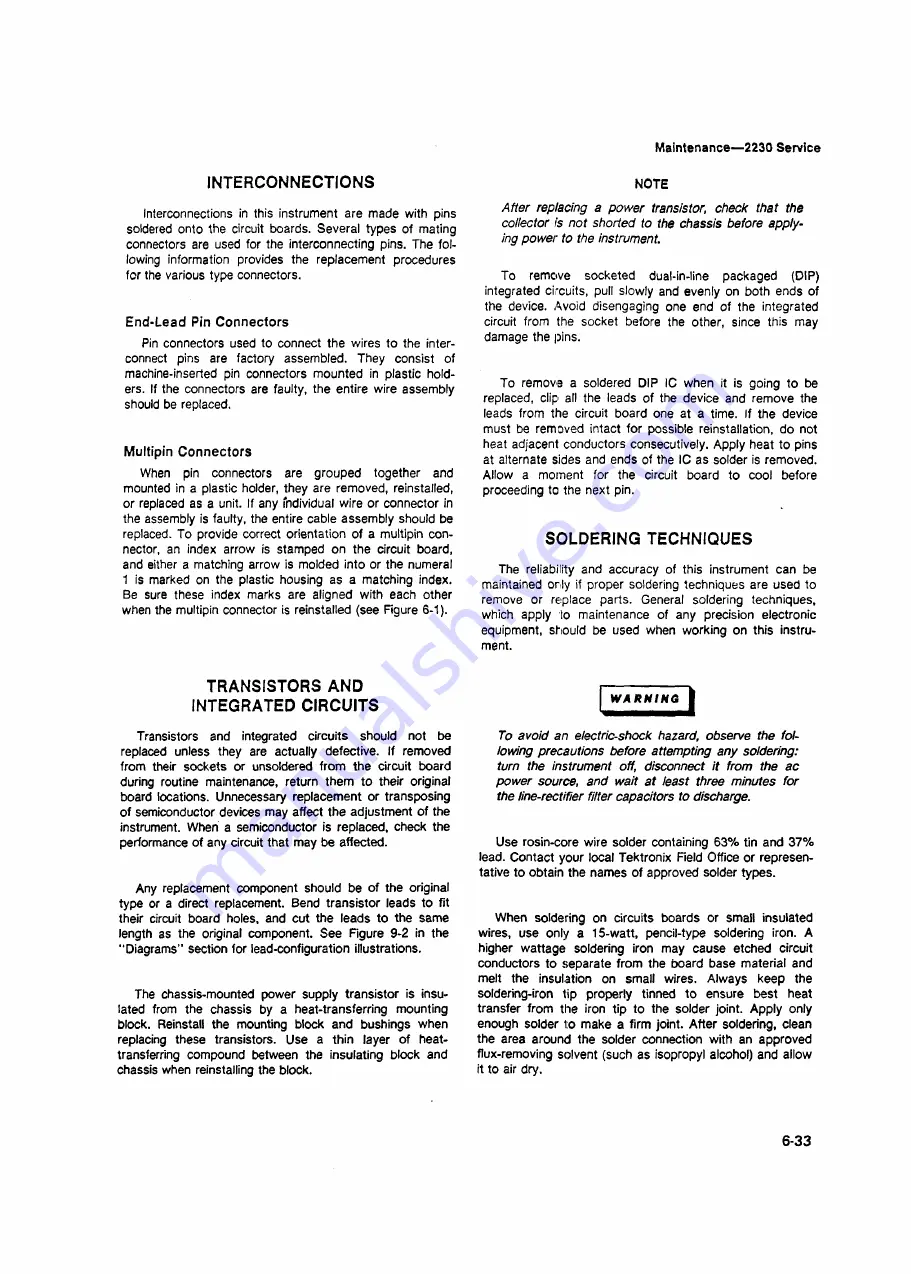
INTERCONNECTIONS
Interconnections in this instrument are made with pins
soldered onto the circuit boards. Several types of mating
connectors are used for the interconnecting pins. The fol
lowing information provides the replacement procedures
for the various type connectors.
End-Lead Pin Connectors
Pin connectors used to connect the wires to the inter
connect pins are factory assembled. They consist of
machine-inserted pin connectors mounted in plastic hold
ers. If the connectors are faulty, the entire wire assembly
should be replaced.
Multipin Connectors
When pin connectors are grouped together and
mounted in a plastic holder, they are removed, reinstalled,
or replaced as a unit. If any individual wire or connector in
the assembly is faulty, the entire cable assembly should be
replaced. To provide correct orientation of a multipin con
nector, an index arrow is stamped on the circuit board,
and either a matching arrow is molded into or the numeral
1 is marked on the plastic housing as a matching index.
Be sure these index marks are aligned with each other
when the multipin connector is reinstalled (see Figure 6-1).
TRANSISTORS AND
INTEGRATED CIRCUITS
Transistors and integrated circuits should not be
replaced unless they are actually defective. If removed
from their sockets or unsoldered from the circuit board
during routine maintenance, return them to their original
board locations. Unnecessary replacement or transposing
of semiconductor devices may affect the adjustment of the
instrument. When a semiconductor is replaced, check the
performance of any circuit that may be affected.
Any replacement component should be of the original
type or a direct replacement. Bend transistor leads to fit
their circuit board holes, and cut the leads to the same
length as the original component. See Figure 9-2 in the
"Diagrams" section for lead-configuration illustrations.
The chassis-mounted power supply transistor is insu
lated from the chassis by a heat-transferring mounting
block. Reinstall the mounting block and bushings when
replacing these transistors. Use a thin layer of heat
transferring compound between the insulating block and
chassis when reinstalling the block.
Maintenance— 2230 Service
NOTE
After replacing a power transistor, check that the
collector is not shorted to the chassis before apply
ing power to the instrument.
To remove socketed dual-in-line packaged (DIP)
integrated circuits, pull slowly and evenly on both ends of
the device. Avoid disengaging one end of the integrated
circuit from the socket before the other, since this may
damage the pins.
To remove a soldered DIP 1C when it is going to be
replaced, clip all the leads of the device and remove the
leads from the circuit board one at a time. If the device
must be removed intact for possible reinstallation, do not
heat adjacent conductors consecutively. Apply heat to pins
at alternate sides and ends of the 1C as solder is removed.
Allow a moment for the circuit board to cool before
proceeding to the next pin.
SOLDERING TECHNIQUES
The reliability and accuracy of this instrument can be
maintained only if proper soldering techniques are used to
remove or replace parts. General soldering techniques,
which apply to maintenance of any precision electronic
equipment, should be used when working on this instru
ment.
W A R M I N G
I
To avoid an electric-shock hazard, observe the fol
lowing precautions before attempting any soldering:
turn the instrument off, disconnect it from the ac
power source, and wait at least three minutes for
the line-rectifier filter capacitors to discharge.
Use rosin-core wire solder containing 63% tin and 37%
lead. Contact your local Tektronix Field Office or represen
tative to obtain the names of approved solder types.
When soldering on circuits boards or small insulated
wires, use only a 15-watt, pencil-type soldering iron. A
higher wattage soldering iron may cause etched circuit
conductors to separate from the board base material and
melt the insulation on small wires. Always keep the
soldering-iron tip properly tinned to ensure best heat
transfer from the iron tip to the solder joint. Apply only
enough solder to make a firm joint. After soldering, clean
the area around the solder connection with an approved
flux-removing solvent (such as isopropyl alcohol) and allow
it to air dry.
6-33
Summary of Contents for 2230
Page 12: ...2230 Service X The 2230 Digital Storage Oscilloscope 4998 01 ...
Page 33: ...Operating Information 2230 Service Figure 2 5 Vertical controls and connectors 2 6 ...
Page 48: ...Operating Information 2230 Service Figure 2 11 X Y Plotter interfacing ...
Page 56: ...Theory of Operation 2230 Service 4999 01 3 2 Figure 3 1 Simplified block diagram ...
Page 68: ...Operating Information 2230 Service Figure 2 11 X Y Plotter interfacing ...
Page 76: ...Theory of Operation 2230 Service 4999 01 3 2 Figure 3 1 Simplified block diagram ...
Page 98: ...Theory of Operation 2230 Service 499 9 06 Figure 3 6 Horizontal Amplifier block diagram 3 24 ...
Page 111: ...Theory of Operation 2230 Service 3 37 Figure 3 9 Acquisition Memory timing ...
Page 190: ...Maintenance 2230 Service 999 14 Figure 6 3 Isolated kernel timing 6 9 ...
Page 329: ...PUT Figure 9 2 S em ico n d u cto r lea d co n fig u ratio n s ...
Page 332: ...2230Service CHASSIS MOUNTED PARTS ...
Page 334: ...A14 CH 1 LOGIC BOARD ...
Page 337: ......
Page 344: ...u sr z z o 1 ...
Page 347: ...i n 5 a O Q q o u S a o h UJ s a b c d e f g h j k l m n ...
Page 352: ......
Page 355: ...WAVEFORMS FOR DIAGRAM 5 4999 83 ...
Page 358: ...I W L U O U rc a 4 2 s ...
Page 361: ...WAVEFORMS FOR DIAGRAM 6 S 84 ...
Page 362: ...2230 Service TEST SCOPE TRIGGERED ON U665 PIN 8 FOR WAVEFORMS 31 THROUGH 33 ...
Page 365: ... I I ...
Page 366: ...A 1 6 S W E E P R EFEREN CE BOARD FIG 9 17 2230 Service Figure 9 17 A16 Sweep Reference board ...
Page 369: ... o 0 UJU sa eg aiu c u J in su eg 5 C sis n g e s o N QO ...
Page 371: ...Static Sensitive Devices See Maintenance Section CM I rv CD o 2230 Service ...
Page 378: ......
Page 384: ... I I c o C u o a 5 r O tD v j If 3 IV if I I ci if 5 3 I ...
Page 386: ......
Page 388: ...H K L M N 7 8 8 2 2 3 0 INPUT OUTFUT WIRING INTERCONNECT ...
Page 392: ...W A V E F O R M S F O R D IA G R A M 14 ...
Page 393: ...2230Service 0 0 d s t 4 9 9 9 9 5 ...
Page 394: ...2230 Service TEST SCOPE TRIGGERED ON U911 PIN 21 FOR WAVEFORMS 64 THROUGH 69 4999 92 ...
Page 396: ... ...
Page 397: ...WAVEFORMS FOR DIAGRAM 15 TEST SCOPE TRIGGERED ON U9111 PIN 21 FOR WAVEFORMS 70 THROUGH 77 ...
Page 399: ......
Page 403: ......
Page 404: ......
Page 405: ......
Page 409: ......
Page 415: ...IMF PU TPR A IR TM FQ U I W A V E F O R M SF O RO IA G R A M1 5 W A V E F O R M SF O R i ...
Page 417: ...4999 9S ...
Page 419: ...i s 5 0 C C p F 2 CC p 2 a u 4 I s c c O 2 e e o 5 a o 5 i 2 i f 2 E C 52 ...
Page 423: ...W A V E F O R M SF O RD IA G R A M1 8 O c n ...
Page 424: ...Figure 9 22 A11A1 Input Output board ...
Page 430: ...Figure 9 23 A11A2 Vector Generator board ...
Page 434: ...49 9 9 tOO ...
Page 436: ......
Page 437: ...22 3 0 S ervice W A V E F O R M S F O R D I A G R A M 2 1 m f n h ...
Page 442: ...WAVEFORMS FOR DIAGRAM 22 4999 78 ...
Page 443: ...XY PLOTTER BOARD DIAGRAM 22 See Parts List for serial number ranges ...
Page 447: ...A21 RS 232 OPTION BOARD Flfi A 9 K 01 01 W M ...
Page 450: ......
Page 452: ...COMPONENT NUMBER EXAMPLE ...
Page 459: ...A16 SWEEP REFERENCE ADJUSTMENT LOCATION ...
Page 467: ...2230 Service ...
Page 468: ......
Page 474: ......
Page 475: ...2230 Service ...
Page 476: ...2230 Service ...
Page 477: ... D ...
Page 483: ...2230 Service ...