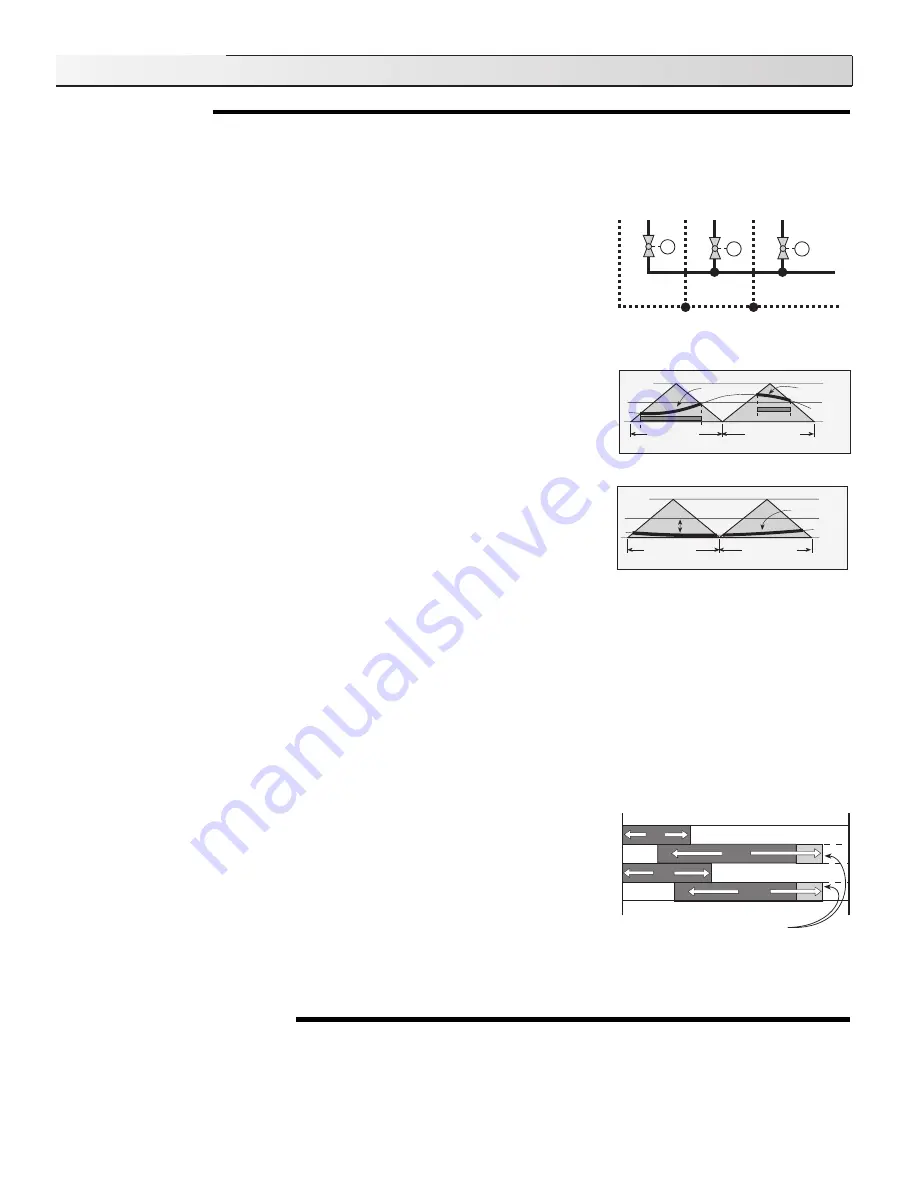
2
Control Strategy
ZONING OPERATION
In a multiple zone heating system, the zones may have different internal heat gains, heat losses or different temperature settings. Each
zone must therefore have individual temperature control. For maximum comfort, the heat should be continuously supplied to the zone
at the same rate the zone is losing heat. The most accurate method of accomplishing this is by outdoor reset; however, it is not normally
economical to modulate the supply water temperature to every zone.
Outdoor reset can be combined with zoning for a more cost effective solution. Through
indoor sensors, a zone control can provide indoor temperature feedback to the outdoor
reset control. The outdoor reset control will then adjust the supply water temperature to
satisfy the zone with the highest water temperature requirement. Heat to the remaining
zones will be cycled on and off by the zone control using zone valves or pumps. Since the
heat is cycled on and off, accurate PID control logic should be provided to maintain a stable
indoor temperature.
PID Zoning Logic
Proportional (P)
In order to prevent indoor temperature swings, the heat supplied to each zone must be
proportional to the heat required by the zone. Proportional control logic can be
accomplished by pulse width modulation (PWM). A typical PWM system has a fixed
operating cycle. During this operating cycle, the on time of the zone relay is varied
based on the difference between the desired zone temperature and the actual zone
temperature. As the zone temperature drops, the relay on time increases and as the
zone temperature rises, the relay on time decreases.
Integral (I)
Controls that are strictly proportional suffer from a problem of offset. The amount of heat
supplied to the zone depends on how far the space temperature is below the desired
setpoint. This implies that as the heating load increases, the average room temperature
droops. On the coldest day of the year, the most heat is required and therefore the room
temperature must be coldest.
In order to overcome this offset, integral control logic is used. Only digital controls can provide integral control logic due to the lengthy
response time of buildings. Integral control logic is based on time. The longer the room temperature is below the desired setpoint,
the more heat is supplied to the room. With integral control logic, full heat can be supplied to the room on the coldest day of the
year without requiring that the room be cold.
Derivative (D)
In order to speed up the control’s response to quick changes in the heating load, derivative control logic is required. However,
sudden room temperature changes, for example from an open door or window, should be ignored by an intelligent control.
P + I + D = PID
If proportional, integral and derivative (PID) control logic are combined, the control is more able to prevent excessive temperature
swings and provide a stable room temperature under all conditions. It not only takes into account how much the room temperature
has drooped, but also how long there has been a droop and how fast the temperature is changing.
Zone Load Staggering
In a multiple zone system, there can be sudden load changes on the boiler and system
due to multiple zones turning on or off. These sudden load changes often lead to boiler
short cycling and unnecessary mechanical stresses. The operation of the system can be
improved by staggering the starting points of each zone relay within the operating cycle.
Staggering of the zones maintains a relatively constant system flow rate which improves
boiler operation. Controlled staggering can also minimize boiler running time and improve
system efficiency when only a few zones are needed for short periods.
Zone Post Purge
Before the last zone is turned off in a heating cycle, the boiler is turned off but the zone continues to draw heat from the boiler. This
post purge of the boiler reduces stand-by losses and reduces overall energy consumption.
UNOCCUPIED (NIGHT SETBACK)
During the night, or at times when people are not within the building, energy can be saved by lowering the building temperature for an
UnOccupied (Night Setback) period.
Due to the large thermal mass of buildings, it takes a long time for the indoor space temperature to significantly change whenever the
heating system is turned on or off. The building heat up or cool down time is further increased when high mass heating systems are
used (e.g. radiant floors). In most cases night setback cannot be used with these systems due to the long recovery time required in the
morning. A typical system is demonstrated in the diagram on page 3.
Zone 1
Zone 2
Zone 3
Zone 4
Post Purge
(Boiler off, Pump on)
On
On
On
On
On
70
°
F
(21
°
C)
15 minutes
15 minutes
13 minutes
no heat
72
°
F
(22
°
C)
68
°
F
(20
°
C)
droop
70
°
F
(22
°
C)
15 minutes
15 minutes
5 minutes
10 minutes
on
no heat
72
°
F
(22
°
C)
68
°
F
(20
°
C)
Heat
Source
90%
time on
85%
time on
100%
time on
M
M
M