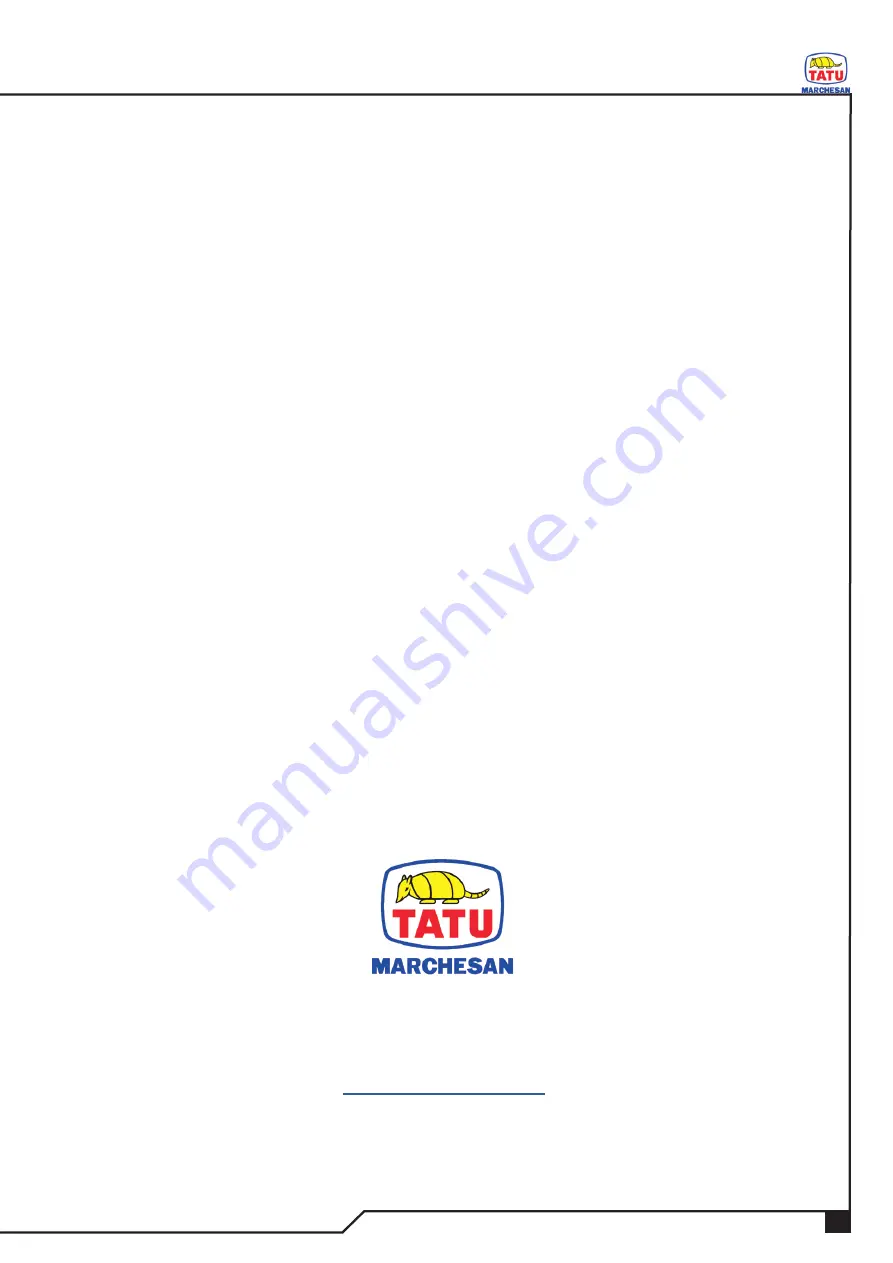
1
GNCRP / GNCRPE / GNCRPE 230 - Rev. 03 - Aug/22
Introduction
MARCHESAN IMPLEMENTOS E MÁQUINAS AGRÍCOLAS "TATU" S.A.
MARCHESAN IMPLEMENTOS E MÁQUINAS AGRÍCOLAS "TATU" S.A.
Marchesan Av., 1979 - Zip Code 15994-900 - Matão - SP - Brazil
Telephone 55.16.3382.8282
www.marchesan.com.br
This operator's manual helps on the assembly process and
provides the necessary information for the correct operation
and maintenance, thus assuring a higher yield, safety and
durability. This manual contains the necessary information for
the best performance of your equipment. The operator and the
maintenance staff must carefully read the entire manual before
working with the equipment. They must also read and understand
the safety recommendations.
For any further explanation or in the case of technical
problems that may arise during the service, consult your dealer
and the Technical support department of the factory, as they can
ensure the fully functioning of your TATU equipment.
We reiterate that a careful read and an observation of every
item on this manual are needed to assure a greater lifetime of
your equipment.