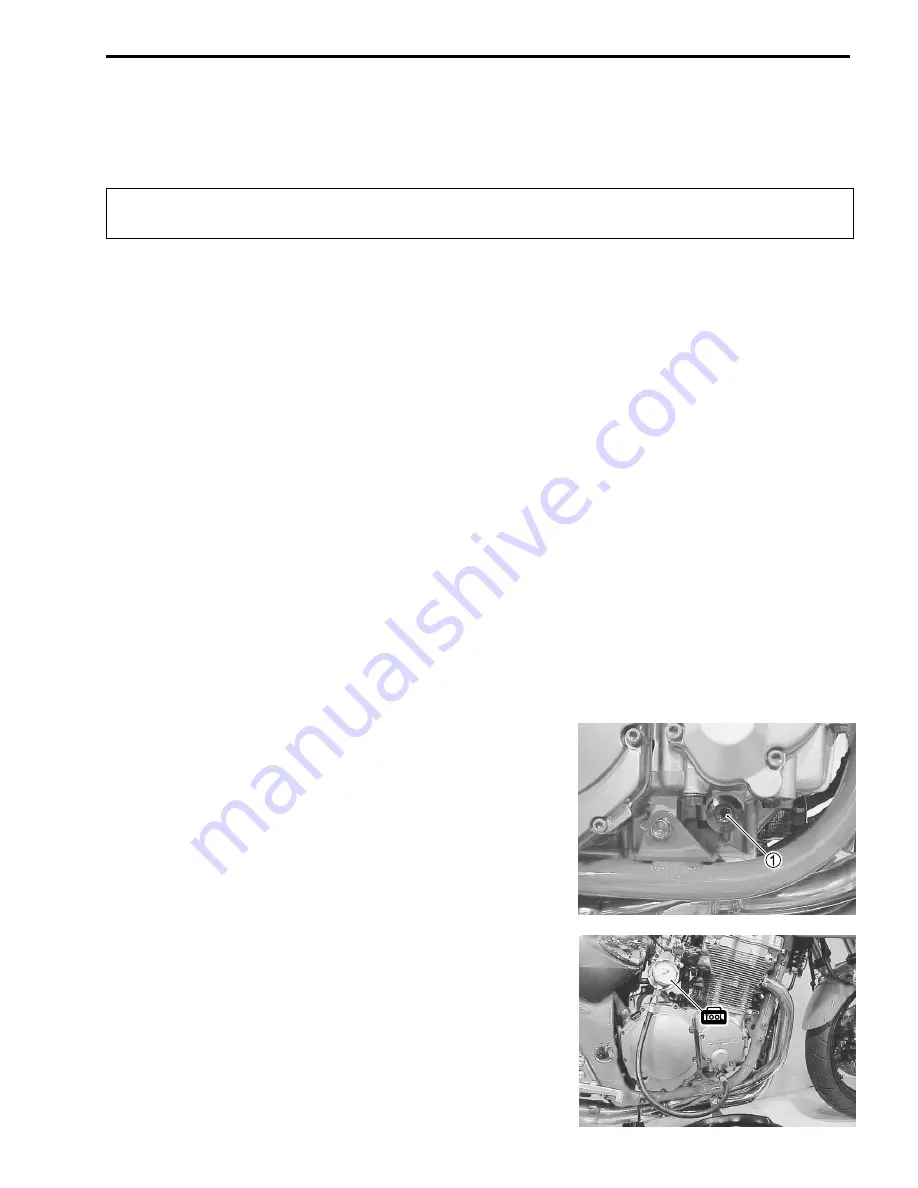
PERIODIC MAINTENANCE 2-25
PERIODIC MAINTENANCE 2-25
PERIODIC MAINTENANCE 2-25
PERIODIC MAINTENANCE 2-25
PERIODIC MAINTENANCE 2-25
OIL PRESSURE CHECK
Check the engine oil pressure periodically. This will give a good indication of the condition of the moving
parts.
OIL PRESSURE SPECIFICATION
Above 300 kPa (3.0 kgf/cm
2
, 43 psi)
Below 600 kPa (6.0 kgf/cm
2
, 85 psi)
at 3 000 r/min., oil temp. at 60°C (140°F)
If the oil pressure is lower or higher than the specification, the following causes may be considered.
LOW OIL PRESSURE
* Clogged oil filter
* Oil leakage from the oil passage
* Damaged O-ring
* Defective oil pump
* Combination of the above items
HIGH OIL PRESSURE
* Engine oil viscosity is too high
* Clogged oil passage
* Combination of the above items
OIL PRESSURE TEST PROCEDURE
Start the engine and check if the oil pressure indicator light is
turned on. If the light stays on, check the oil pressure indicator
light circuit. If the circuit is OK, check the oil pressure in the fol-
lowing manner.
• Remove the main oil gallery plug
1
.
• Install the oil pressure gauge and adaptor into the main oil
gallery.
• Warm up the engine as follows:
Summer: 10 min. at 2 000 r/min.
Winter: 20 min. at 2 000 r/min.
• After warm up, increase the engine speed to 3 000 r/min. (ob-
serve the tachometer), and read the oil pressure gauge.
&
09915-74510: Oil pressure gauge
09915-74540: Oil pressure gauge attachment
09915-77330: Meter (for high pressure)
)
Main oil gallery plug: 40 N.m (4.0 kgf.m, 29.0 lb-ft)
Summary of Contents for GSF600K1 2001
Page 1: ...9 9 5 0 0 3 6 1 0 2 0 1 E GSF600S GSF600...
Page 68: ...3 30 ENGINE BOND 1207B should be applied to the following locations The line of BOND...
Page 116: ...3 78 ENGINE...
Page 133: ...ENGINE 3 95 ENGINE LUBRICATION SYSTEM...
Page 135: ...ENGINE 3 97 CYLINDER HEAD COOLING SYSTEM...
Page 147: ...FUEL SYSTEM 4 9 I D NO LOCATION Each carburetor has an I D number 1 printed on its body...
Page 295: ...SERVICING INFORMATION 7 27 NOTE...
Page 296: ...7 28 SERVICING INFORMATION NOTE...
Page 380: ...Printed in Japan Y K1 K2...