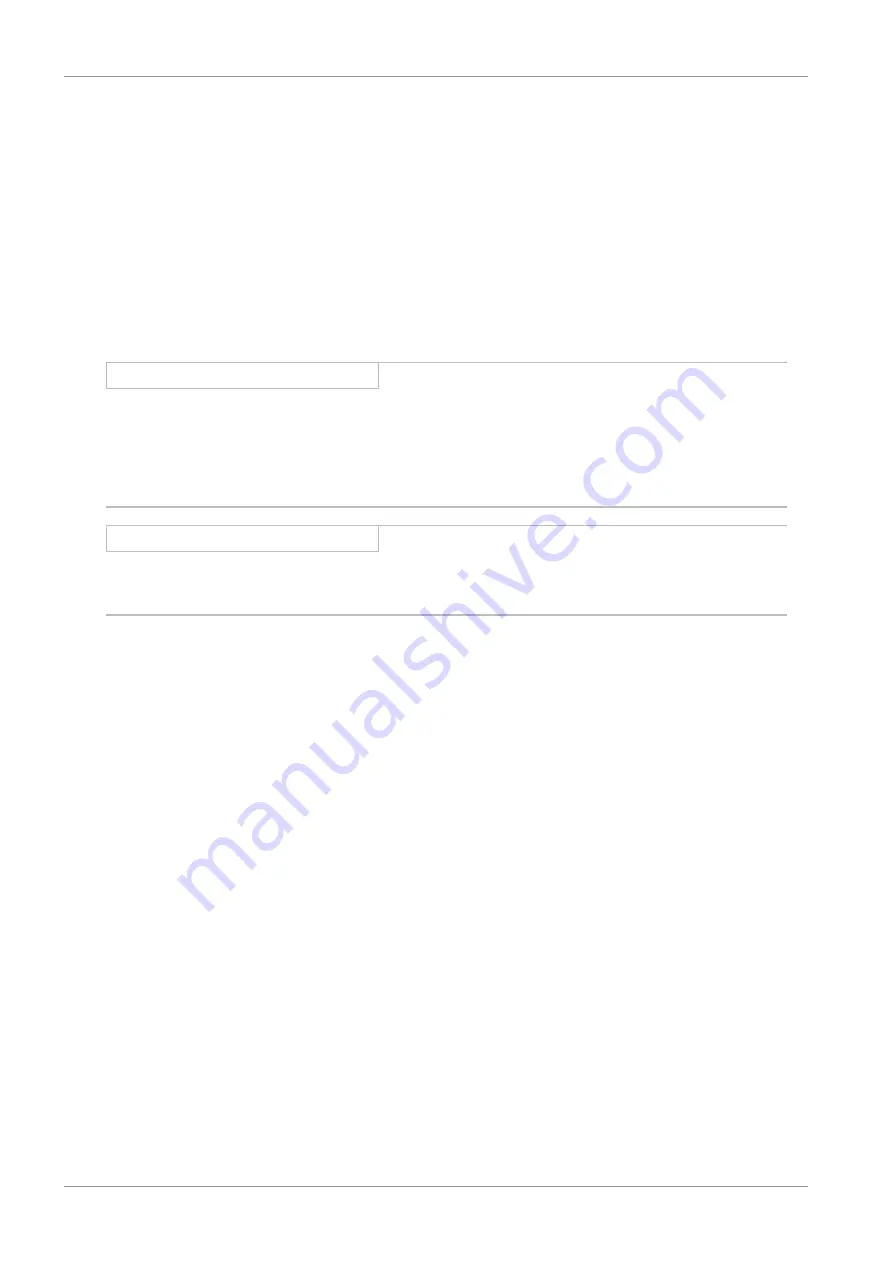
6 | Project configuration
STOBER
52
05/2019 | ID 442790.01
6
Project configuration
Relevant information on the project configuration and design of your drive system can be found in the following chapters.
6.1
Drive controllers
Minimum time between energizing two devices
The drive controllers have temperature-dependent resistors in the charging circuit that prevent the devices from being
damaged when being connected to the grid after a fault, such as a short-circuited DC link, incorrect wiring, etc. These
resistors are heated when charging the DC link. In order to prevent overloading, a specified, minimum time period must be
maintained between energizing two devices.
Information
For the time span between two energizing processes, note that:
a) Direct, repeat activation of the supply voltage is possible for power-on/power-off operation.
b) A time span of > 15 must be observed between two energizing processes during continuous, cyclical power-on/
power-off operation with increased charging capacity.
Information
The STO safety function is available for safe shutdown as an alternative to continuous, cyclical power-on/power-off
operation.
6.2
DC link connection
Braked motors work like generators: Operating with an active drive controller, they convert kinetic energy from movement
into electrical energy. This electrical energy is stored in the DC link capacitors of the drive controller. It can be supplied to
powered motors with connected DC circuits and be used efficiently as a result.
However, capacitors in the DC link can only accept a limited amount of energy. The DC link voltage increases when a motor
decelerates. If the DC link voltage rises above a defined limit, a chopper circuit is activated that tries to convert the excess
energy into heat by means of a connected braking resistor. If the permitted maximum voltage is nonetheless reached, any
possible damage must be prevented. The drive controller switches to the Fault state and shuts down.
In a DC link connection, the DC link capacitors of the drive controllers involved are connected in parallel. As a result, the
maximum acceptable amount of energy increases in the DC link in comparison to a single unit.
The DC link connection can help save energy and reduce costs, especially in coil winding technology or during regular
acceleration and braking cycles.