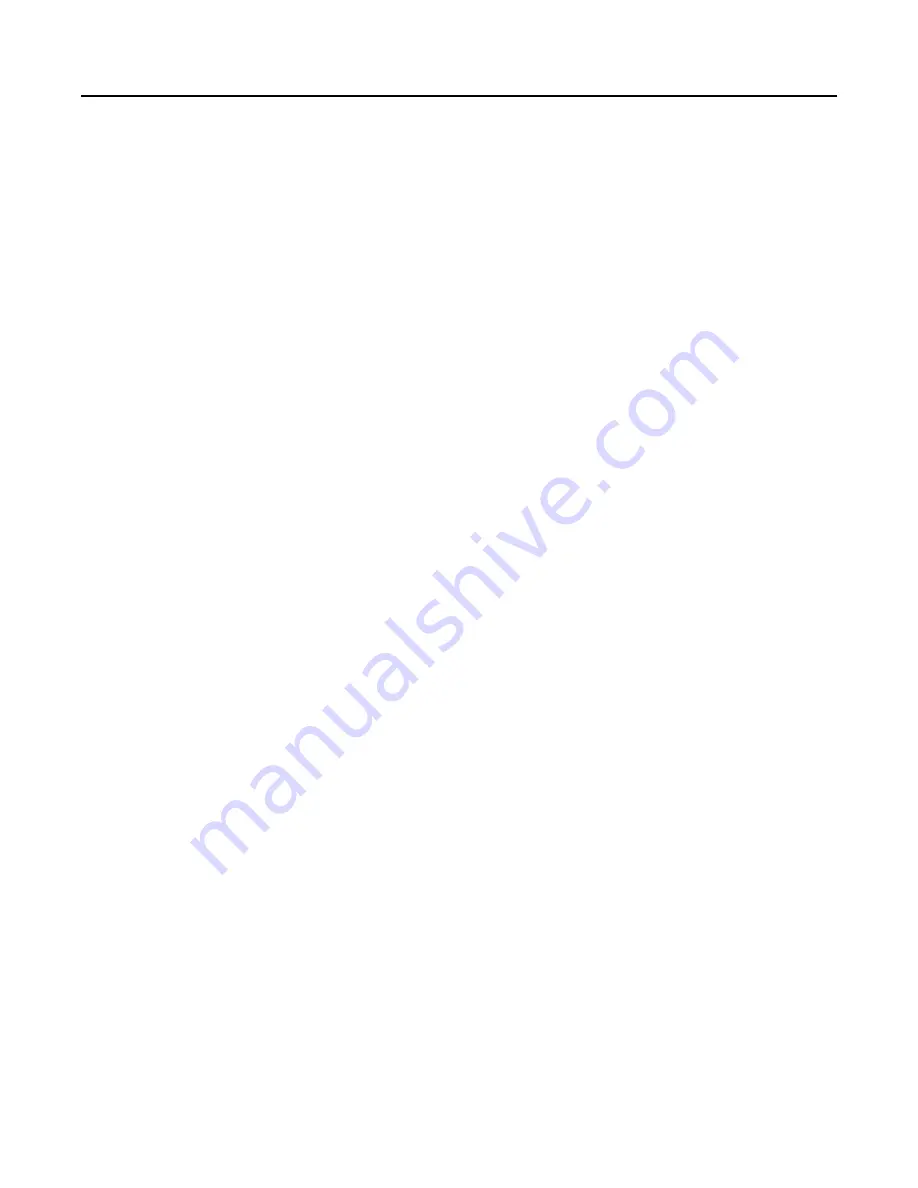
Engine Operation
i06545704
Engine Operation
SMCS Code:
1000
Proper operation and maintenance are key factors in
obtaining the maximum life and economy of the
engine. If the directions in the Operation and
Maintenance Manual are followed, costs can be
minimized and engine service life can be maximized.
The time that is needed for the engine to reach
normal operating temperature can be less than the
time needed for a walk-around inspection of the
engine.
After the engine is started and after the engine
reaches normal operating temperature, the engine
can be operated at the rated rpm. The engine will
reach normal operating temperature faster when the
engine is at rated speed. The engine will reach
normal operating temperature faster when the engine
is at low-power demand. This procedure is more
effective than idling the engine at no load. The engine
should reach operating temperature in a few minutes.
Gauge readings should be observed and the data
should be recorded frequently while the engine is
operating. Comparing the data over time will help to
determine normal readings for each gauge.
Comparing data over time will also help detect
abnormal operating developments. Significant
changes in the readings should be investigated.
Engines rated for constant speed use are allowed to
complete a starting sequence, an operation at a
single constant speed, and a shutdown sequence.
Every time the engine is run, each of these
operations should occur only once. The starting
sequence and shutdown sequence can include a
short period of operation at the low idle speed for
purposes of warming up and cooling down the engine
or driven equipment. The emissions type approval is
not valid for operation of a constant speed engine in
a manner different from that described above.
i00613522
Engine Warm-up
SMCS Code:
1000
1.
Run the engine at low idle for three to five minutes,
or run the engine at low idle until the jacket water
temperature starts to rise.
More time may be necessary when the
temperature is below −18°C (0°F).
2.
Check all of the gauges during the warm-up
period.
3.
Perform another walk-around inspection. Check
the engine for fluid leaks and air leaks.
4.
Increase the rpm to the rated rpm. Check for fluid
leaks and air leaks. The engine may be operated
at full rated rpm and at full load when the jacket
water temperature reaches 60°C (140°F).
i01646335
Engaging the Driven
Equipment
SMCS Code:
1000
1.
Operate the engine at one-half of the rated rpm,
when possible.
2.
Engage the driven equipment without a load on the
equipment, when possible.
Interrupted starts put excessive stress on the drive
train. Interrupted starts also waste fuel. To get the
driven equipment in motion, engage the clutch
smoothly with no load on the equipment. This
method should produce a start that is smooth and
easy. The engine rpm should not increase and the
clutch should not slip.
3.
Ensure that the ranges of the gauges are normal
when the engine is operating at one-half of the
rated rpm. Ensure that all gauges operate
properly.
4.
Increase the engine rpm to the rated rpm. Always
increase the engine rpm to the rated rpm before
the load is applied.
5.
Apply the load. Begin operating the engine at low
load. Check the gauges and equipment for proper
operation. After normal oil pressure is reached and
the temperature gauge begins to move, the engine
may be operated at full load. Check the gauges
and equipment frequently when the engine is
operated under load.
Extended operation at low idle or at reduced load
may cause increased oil consumption and carbon
buildup in the cylinders. This carbon buildup
results in a loss of power and/or poor
performance.
36
SEBU8312-03
Summary of Contents for TANVAC HDV3000
Page 2: ...1300 998 784 STGGLOBAL NET OPERATORS MANUAL TANVAC HDV3000 Sec on 1 ...
Page 11: ...8 4 COMPONENT IDENTIFICATION Engine Control Panel Control Panel ...
Page 14: ...11 Water System Water pump Switch Water Pump ...
Page 15: ...12 Water Strainer Hose Reel ...
Page 16: ...13 Water Tank Drain Valve Lever Vacuum System Dump valve Suction Valve ...
Page 17: ...14 Blower Vacuum ...
Page 19: ...16 Primary Shutoff Assembly Collection Tank Interior Bag House Lid ...
Page 20: ...17 Bag House Drain Valve Tools Water Gun ...
Page 34: ...31 20 3000lt ELECTRIC CONTROL BOX CIRCUIT DIAGRAM 1 ...
Page 35: ...32 21 3000lt ELECTRIC CONTROL BOX CIRCUIT DIAGRAM 2 ...
Page 36: ...33 22 3000lt VACUUM UNIT BOTTOM RAIL ASSEMBLE ...
Page 37: ...1300 998 784 STGGLOBAL NET OPERATORS MANUAL Cat 2 2 Opera on Manual Sec on 2 ...
Page 137: ... Table 32 contd 100 SEBU8312 03 Reference Information Section Maintenance Log ...
Page 141: ......
Page 144: ...1300 998 784 STGGLOBAL NET OPERATORS MANUAL Comet Manual Sec on 3 ...
Page 161: ...1300 998 784 STGGLOBAL NET OPERATORS MANUAL Sutorbilt R Series Sec on 4 ...
Page 200: ...SB 7 632 Page 39 SECTION 8 PARTS LIST ...
Page 202: ...SB 7 632 Page 41 ...
Page 204: ...SB 7 632 Page 43 301GAE810 A Ref Drawing ...
Page 206: ...SB 7 632 Page 45 ...
Page 208: ...SB 7 632 Page 47 ...
Page 210: ...SB 7 632 Page 49 303GAE810 A Ref Drawing ...
Page 212: ...SB 7 632 Page 51 ...
Page 214: ...SB 7 632 Page 53 ...
Page 216: ...SB 7 632 Page 55 300GAE810 A Ref Drawing ...
Page 218: ...SB 7 632 Page 57 ...
Page 220: ...SB 7 632 Page 59 ...
Page 222: ...SB 7 632 Page 61 302GAA810 A Ref Drawing ...
Page 224: ...SB 7 623 Page 63 ...
Page 226: ...1300 998 784 STGGLOBAL NET OPERATORS MANUAL Sutorbilt P Series Sec on 5 ...
Page 245: ...SB 7 622 Page 12 1 PIPE STEEL 2 SCH 80 2 MED CARBON STEEL 1 2 FIGURE 9 GEAR DRIVER SK2150 ...
Page 258: ...SB 7 622 Page 25 SECTION 8 PARTS LIST 300GAF810 B Ref Drawing ...
Page 260: ...SB 7 622 Page 27 300GAG810 A Ref Drawing ...
Page 262: ...SB 7 622 Page 29 300GAH810 A Ref Drawing ...
Page 265: ......
Page 266: ...1300 998 784 STGGLOBAL NET OPERATORS MANUAL Lofa Manual Sec on 6 ...
Page 294: ...1300 998 784 STGGLOBAL NET OPERATORS MANUAL Excava on Hydro SWMS Sec on 7 ...
Page 314: ...1300 998 784 STGGLOBAL NET OPERATORS MANUAL Pressure Cleaner Water SWMS Sec on 8 ...