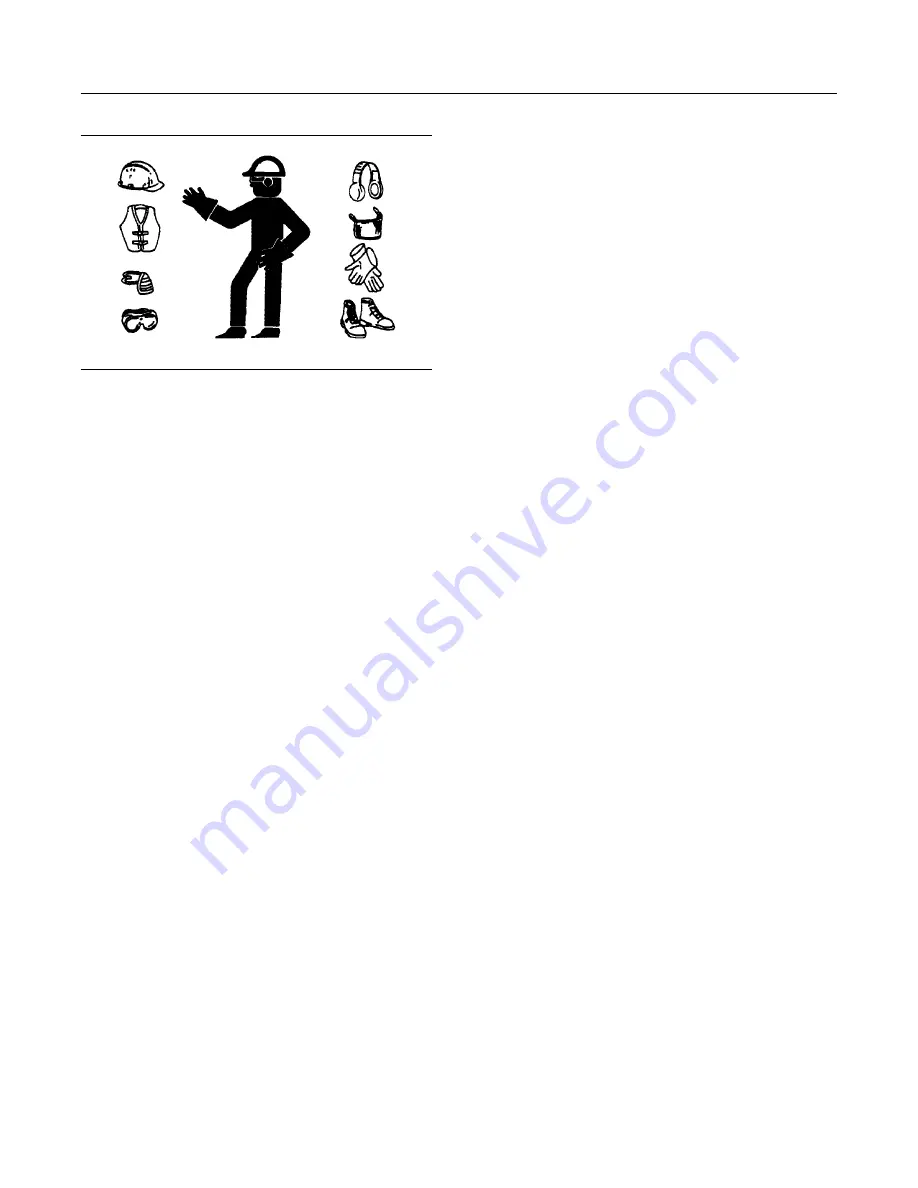
Illustration 6
g00702020
• Wear a hard hat, protective glasses, and other
protective equipment, as required.
• When work is performed around an engine that is
operating, wear protective devices for ears in
order to help prevent damage to hearing.
• Do not wear loose clothing or jewelry that can
snag on controls or on other parts of the engine.
• Ensure that all protective guards and all covers
are secured in place on the engine.
• Never put maintenance fluids into glass
containers. Glass containers can break.
• Use all cleaning solutions with care.
• Report all necessary repairs.
Unless other instructions are provided, perform
the maintenance under the following conditions:
• The engine is stopped. Ensure that the engine
cannot be started.
• The protective locks or the controls are in the
applied position.
• Disconnect the batteries when maintenance is
performed or when the electrical system is
serviced. Disconnect the battery ground leads.
Tape the leads in order to help prevent sparks.
• When starting a new engine, make provisions to
stop the engine if an overspeed occurs. If an
engine has not been started since service has
been performed, make provisions to stop the
engine if an overspeed occurs. Shutting down the
engine may be accomplished by shutting off the
fuel supply and/or the air supply to the engine.
• Do not attempt any repairs that are not
understood. Use the proper tools. Replace any
equipment that is damaged or repair the
equipment.
• Start the engine with the operator controls. Never
short across the starting motor terminals or the
batteries. This method of starting the engine could
bypass the engine neutral start system and/or the
electrical system could be damaged.
Pressurized Air and Water
Pressurized air and/or water can cause debris and/or
hot water to be blown out which could result in
personal injury.
The maximum air pressure for cleaning purposes
must be reduced to 205 kPa (30 psi) when the air
nozzle is deadheaded and used with effective chip
guarding (if applicable) and personal protective
equipment. The maximum water pressure for
cleaning purposes must be below 275 kPa (40 psi).
When pressurized air and/or pressurized water is
used for cleaning, wear protective clothing, protective
shoes, and eye protection. Eye protection includes
goggles or a protective face shield. Always wear eye
protection for cleaning the cooling system.
SEBU8312-03
9
Summary of Contents for TANVAC HDV3000
Page 2: ...1300 998 784 STGGLOBAL NET OPERATORS MANUAL TANVAC HDV3000 Sec on 1 ...
Page 11: ...8 4 COMPONENT IDENTIFICATION Engine Control Panel Control Panel ...
Page 14: ...11 Water System Water pump Switch Water Pump ...
Page 15: ...12 Water Strainer Hose Reel ...
Page 16: ...13 Water Tank Drain Valve Lever Vacuum System Dump valve Suction Valve ...
Page 17: ...14 Blower Vacuum ...
Page 19: ...16 Primary Shutoff Assembly Collection Tank Interior Bag House Lid ...
Page 20: ...17 Bag House Drain Valve Tools Water Gun ...
Page 34: ...31 20 3000lt ELECTRIC CONTROL BOX CIRCUIT DIAGRAM 1 ...
Page 35: ...32 21 3000lt ELECTRIC CONTROL BOX CIRCUIT DIAGRAM 2 ...
Page 36: ...33 22 3000lt VACUUM UNIT BOTTOM RAIL ASSEMBLE ...
Page 37: ...1300 998 784 STGGLOBAL NET OPERATORS MANUAL Cat 2 2 Opera on Manual Sec on 2 ...
Page 137: ... Table 32 contd 100 SEBU8312 03 Reference Information Section Maintenance Log ...
Page 141: ......
Page 144: ...1300 998 784 STGGLOBAL NET OPERATORS MANUAL Comet Manual Sec on 3 ...
Page 161: ...1300 998 784 STGGLOBAL NET OPERATORS MANUAL Sutorbilt R Series Sec on 4 ...
Page 200: ...SB 7 632 Page 39 SECTION 8 PARTS LIST ...
Page 202: ...SB 7 632 Page 41 ...
Page 204: ...SB 7 632 Page 43 301GAE810 A Ref Drawing ...
Page 206: ...SB 7 632 Page 45 ...
Page 208: ...SB 7 632 Page 47 ...
Page 210: ...SB 7 632 Page 49 303GAE810 A Ref Drawing ...
Page 212: ...SB 7 632 Page 51 ...
Page 214: ...SB 7 632 Page 53 ...
Page 216: ...SB 7 632 Page 55 300GAE810 A Ref Drawing ...
Page 218: ...SB 7 632 Page 57 ...
Page 220: ...SB 7 632 Page 59 ...
Page 222: ...SB 7 632 Page 61 302GAA810 A Ref Drawing ...
Page 224: ...SB 7 623 Page 63 ...
Page 226: ...1300 998 784 STGGLOBAL NET OPERATORS MANUAL Sutorbilt P Series Sec on 5 ...
Page 245: ...SB 7 622 Page 12 1 PIPE STEEL 2 SCH 80 2 MED CARBON STEEL 1 2 FIGURE 9 GEAR DRIVER SK2150 ...
Page 258: ...SB 7 622 Page 25 SECTION 8 PARTS LIST 300GAF810 B Ref Drawing ...
Page 260: ...SB 7 622 Page 27 300GAG810 A Ref Drawing ...
Page 262: ...SB 7 622 Page 29 300GAH810 A Ref Drawing ...
Page 265: ......
Page 266: ...1300 998 784 STGGLOBAL NET OPERATORS MANUAL Lofa Manual Sec on 6 ...
Page 294: ...1300 998 784 STGGLOBAL NET OPERATORS MANUAL Excava on Hydro SWMS Sec on 7 ...
Page 314: ...1300 998 784 STGGLOBAL NET OPERATORS MANUAL Pressure Cleaner Water SWMS Sec on 8 ...