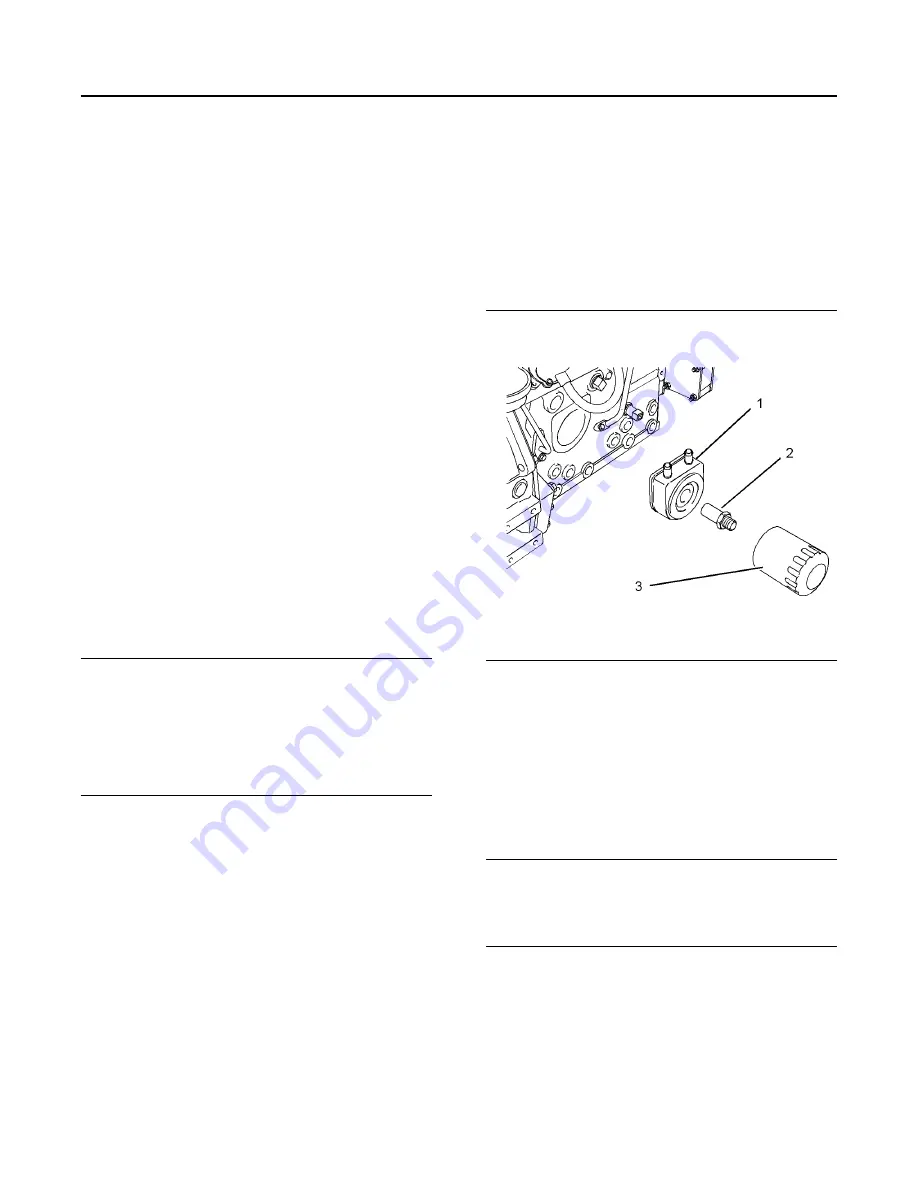
Do not drain the oil when the engine is cold. As the oil
cools, suspended waste particles settle on the
bottom of the oil pan. The waste particles are not
removed with the draining cold oil. Drain the
crankcase with the engine stopped. Drain the
crankcase with the oil warm. This draining method
allows the waste particles that are suspended in the
oil to be drained correctly.
Failure to follow this recommended procedure will
cause the waste particles to be recirculated through
the engine lubrication system with the new oil.
Drain the Engine Oil
After the engine has been run at the normal
operating temperature, stop the engine. Use one of
the following methods to drain the engine crankcase
oil:
• If the engine is equipped with a drain valve, turn
the drain valve knob counterclockwise in order to
drain the oil. After the oil has drained, turn the
drain valve knob clockwise in order to close the
drain valve.
• If the engine is not equipped with a drain valve,
remove the oil drain plug in order to allow the oil to
drain. After the oil has drained, the oil drain plug
should be cleaned and installed.
Replace the Oil Filter
NOTICE
Caterpillar oil filters are built to Caterpillar specifica-
tions. Use of an oil filter not recommended by Cater-
pillar could result in severe engine damage to the
engine bearings, crankshaft, etc., as a result of the
larger waste particles from unfiltered oil entering the
engine lubricating system. Only use oil filters recom-
mended by Caterpillar.
1.
Remove the oil filter with a
1U-8760
Chain
Wrench.
Note:
The following actions can be carried out as
part of the preventive maintenance program.
2.
Cut the oil filter open with a
175-7546
Oil Filter
Cutter Gp. Break apart the pleats and inspect the
oil filter for metal debris. An excessive amount of
metal debris in the oil filter may indicate early wear
or a pending failure.
Use a magnet to differentiate between the ferrous
metals and the nonferrous metals that are found in
the oil filter element. Ferrous metals may indicate
wear on the steel and cast iron parts of the engine.
Nonferrous metals may indicate wear on the
aluminum parts, brass parts or bronze parts of the
engine. Parts that may be affected include the
following items: main bearings, rod bearings,
turbocharger bearings and cylinder heads.
Due to normal wear and friction, it is not
uncommon to find small amounts of debris in the
oil filter. Consult your Caterpillar dealer in order to
arrange for a further analysis if an excessive
amount of debris is found in the oil filter.
Illustration 52
g01334593
(1) Oil cooler
(2) Adapter
(3) Oil filter
Note:
Oil cooler (1) and adapter (2) are not installed
on all engines.
3.
Clean the sealing surface of the cylinder block or
the oil cooler (1).
4.
Apply clean engine oil to the new oil filter seal (3).
NOTICE
Do not fill the oil filters with oil before installing them.
This oil would not be filtered and could be contami-
nated. Contaminated oil can cause accelerated wear
to engine components.
74
SEBU8312-03
Summary of Contents for TANVAC HDV3000
Page 2: ...1300 998 784 STGGLOBAL NET OPERATORS MANUAL TANVAC HDV3000 Sec on 1 ...
Page 11: ...8 4 COMPONENT IDENTIFICATION Engine Control Panel Control Panel ...
Page 14: ...11 Water System Water pump Switch Water Pump ...
Page 15: ...12 Water Strainer Hose Reel ...
Page 16: ...13 Water Tank Drain Valve Lever Vacuum System Dump valve Suction Valve ...
Page 17: ...14 Blower Vacuum ...
Page 19: ...16 Primary Shutoff Assembly Collection Tank Interior Bag House Lid ...
Page 20: ...17 Bag House Drain Valve Tools Water Gun ...
Page 34: ...31 20 3000lt ELECTRIC CONTROL BOX CIRCUIT DIAGRAM 1 ...
Page 35: ...32 21 3000lt ELECTRIC CONTROL BOX CIRCUIT DIAGRAM 2 ...
Page 36: ...33 22 3000lt VACUUM UNIT BOTTOM RAIL ASSEMBLE ...
Page 37: ...1300 998 784 STGGLOBAL NET OPERATORS MANUAL Cat 2 2 Opera on Manual Sec on 2 ...
Page 137: ... Table 32 contd 100 SEBU8312 03 Reference Information Section Maintenance Log ...
Page 141: ......
Page 144: ...1300 998 784 STGGLOBAL NET OPERATORS MANUAL Comet Manual Sec on 3 ...
Page 161: ...1300 998 784 STGGLOBAL NET OPERATORS MANUAL Sutorbilt R Series Sec on 4 ...
Page 200: ...SB 7 632 Page 39 SECTION 8 PARTS LIST ...
Page 202: ...SB 7 632 Page 41 ...
Page 204: ...SB 7 632 Page 43 301GAE810 A Ref Drawing ...
Page 206: ...SB 7 632 Page 45 ...
Page 208: ...SB 7 632 Page 47 ...
Page 210: ...SB 7 632 Page 49 303GAE810 A Ref Drawing ...
Page 212: ...SB 7 632 Page 51 ...
Page 214: ...SB 7 632 Page 53 ...
Page 216: ...SB 7 632 Page 55 300GAE810 A Ref Drawing ...
Page 218: ...SB 7 632 Page 57 ...
Page 220: ...SB 7 632 Page 59 ...
Page 222: ...SB 7 632 Page 61 302GAA810 A Ref Drawing ...
Page 224: ...SB 7 623 Page 63 ...
Page 226: ...1300 998 784 STGGLOBAL NET OPERATORS MANUAL Sutorbilt P Series Sec on 5 ...
Page 245: ...SB 7 622 Page 12 1 PIPE STEEL 2 SCH 80 2 MED CARBON STEEL 1 2 FIGURE 9 GEAR DRIVER SK2150 ...
Page 258: ...SB 7 622 Page 25 SECTION 8 PARTS LIST 300GAF810 B Ref Drawing ...
Page 260: ...SB 7 622 Page 27 300GAG810 A Ref Drawing ...
Page 262: ...SB 7 622 Page 29 300GAH810 A Ref Drawing ...
Page 265: ......
Page 266: ...1300 998 784 STGGLOBAL NET OPERATORS MANUAL Lofa Manual Sec on 6 ...
Page 294: ...1300 998 784 STGGLOBAL NET OPERATORS MANUAL Excava on Hydro SWMS Sec on 7 ...
Page 314: ...1300 998 784 STGGLOBAL NET OPERATORS MANUAL Pressure Cleaner Water SWMS Sec on 8 ...