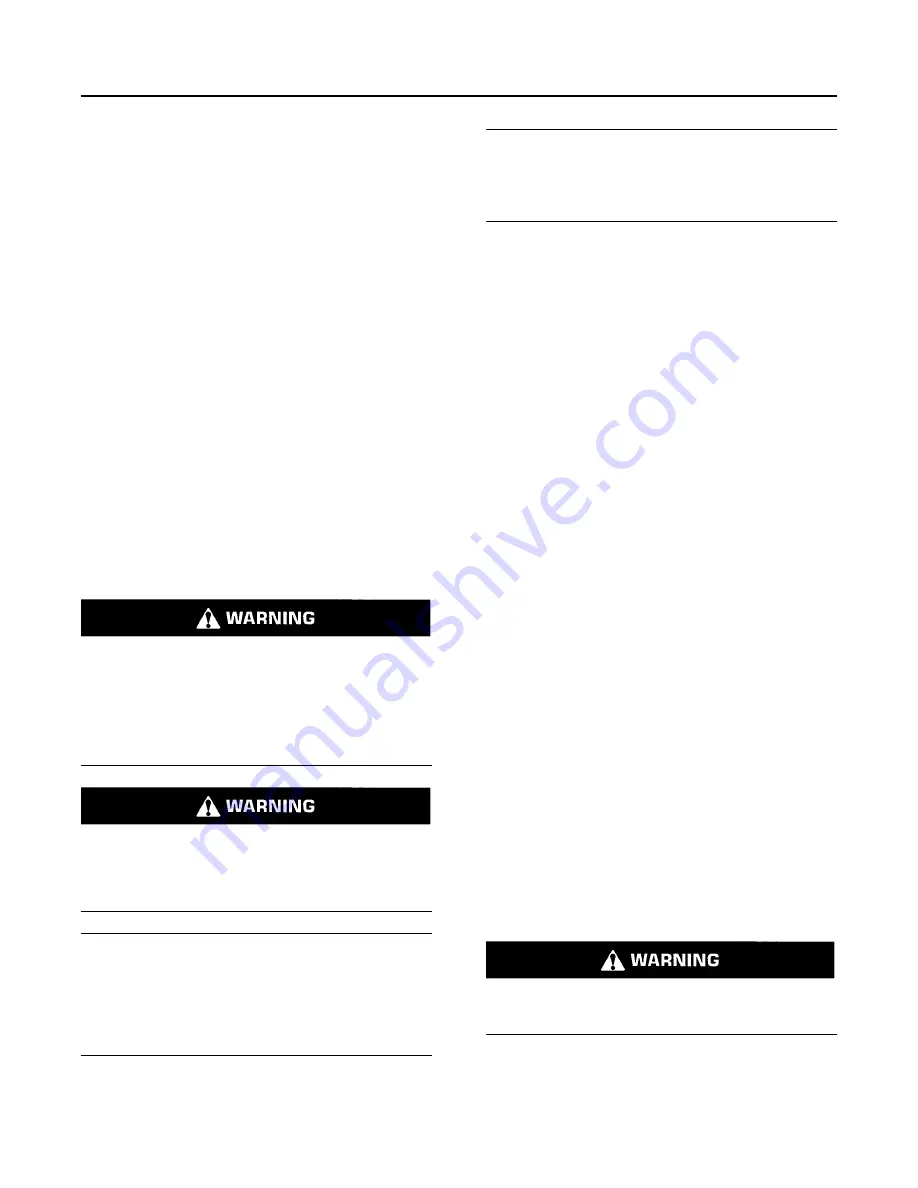
5.
Drain the coolant from the cooling system to a
level that is below the hose that is being replaced.
Drain the coolant into a suitable clean container.
The coolant can be reused.
6.
Remove the hose clamps.
7.
Disconnect the old hose.
8.
Replace the old hose with a new hose.
9.
Install hose clamps which have been inspected or
install new hose clamps. Refer to Specifications,
SENR3130, “Torque Specifications” “Hose
Clamps” for information about selecting and
installing the proper hose clamps.
10.
Refill the cooling system.
11.
Clean the coolant filler cap. Inspect the gaskets
on the filler cap. Inspect the gasket seat. Inspect
the vacuum valve and seat for debris or damage.
Replace the filler cap if the gaskets are damaged.
Install the filler cap.
12.
Start the engine. Inspect the cooling system for
leaks.
Fuel System
Personal injury can result from removing hoses
or fittings in a pressure system.
Failure to relieve pressure can cause personal
injury.
Do not disconnect or remove hoses or fittings un-
til all pressure in the system has been relieved.
Contact with high pressure fuel may cause fluid
penetration and burn hazards. High pressure fuel
spray may cause a fire hazard. Failure to follow
these inspection, maintenance and service in-
structions may cause personal injury or death.
NOTICE
Do not bend or strike high pressure lines. Do not in-
stall bent or damaged lines, tubes or hoses. Repair
any loose or damaged fuel and oil lines, tubes and
hoses. Leaks can cause fires. Inspect all lines, tubes
and hoses carefully. Tighten all connections to the
recommended torque.
NOTICE
Do not allow dirt to enter the fuel system. Thoroughly
clean the area around a fuel system component that
will be disconnected. Fit a suitable cover over any
disconnected fuel system components.
Note:
High-pressure fuel lines may be installed
between the high-pressure fuel pump and the fuel
injectors. High-pressure fuel lines are constantly
charged with high pressure. Do not check the high-
pressure fuel lines with the engine or the starting
motor in operation. Wait for 10 minutes after the
engine stops before you perform any service or
repair on high-pressure fuel lines. Waiting for 10
minutes will to allow the pressure to be purged.
1.
Drain the fuel from the fuel system to a level that is
below the hose that is being replaced.
2.
Remove the hose clamps.
3.
Disconnect the old hose.
Note:
When servicing fuel system, use cap/s or
cover/s as required to protect the system and
maintain fuel system cleanliness.
4.
Replace the old hose with a new hose.
5.
Install hose clamps which have been inspected or
install new hose clamps. Refer to Specifications,
SENR3130, “Torque Specifications” “Hose
Clamps” for information about selecting and
installing the proper hose clamps.
6.
Carefully inspect the engine for any spilled fuel.
Make sure that no fuel remains on or close to the
engine.
Note:
Fuel must be added to the fuel system ahead
of the fuel filter.
7.
Refill the fuel system. Refer to this Operation and
Maintenance Manual, “Fuel System - Prime” for
information about priming the engine with fuel.
8.
Start the engine. Inspect the fuel system for leaks.
Lubrication System
Hot oil and hot components can cause personal
injury. Do not allow hot oil or hot components to
contact the skin.
1.
Drain the oil from the lubrication system to a level
that is below the hose that is being replaced.
2.
Remove the hose clamps.
86
SEBU8312-03
Summary of Contents for TANVAC HDV3000
Page 2: ...1300 998 784 STGGLOBAL NET OPERATORS MANUAL TANVAC HDV3000 Sec on 1 ...
Page 11: ...8 4 COMPONENT IDENTIFICATION Engine Control Panel Control Panel ...
Page 14: ...11 Water System Water pump Switch Water Pump ...
Page 15: ...12 Water Strainer Hose Reel ...
Page 16: ...13 Water Tank Drain Valve Lever Vacuum System Dump valve Suction Valve ...
Page 17: ...14 Blower Vacuum ...
Page 19: ...16 Primary Shutoff Assembly Collection Tank Interior Bag House Lid ...
Page 20: ...17 Bag House Drain Valve Tools Water Gun ...
Page 34: ...31 20 3000lt ELECTRIC CONTROL BOX CIRCUIT DIAGRAM 1 ...
Page 35: ...32 21 3000lt ELECTRIC CONTROL BOX CIRCUIT DIAGRAM 2 ...
Page 36: ...33 22 3000lt VACUUM UNIT BOTTOM RAIL ASSEMBLE ...
Page 37: ...1300 998 784 STGGLOBAL NET OPERATORS MANUAL Cat 2 2 Opera on Manual Sec on 2 ...
Page 137: ... Table 32 contd 100 SEBU8312 03 Reference Information Section Maintenance Log ...
Page 141: ......
Page 144: ...1300 998 784 STGGLOBAL NET OPERATORS MANUAL Comet Manual Sec on 3 ...
Page 161: ...1300 998 784 STGGLOBAL NET OPERATORS MANUAL Sutorbilt R Series Sec on 4 ...
Page 200: ...SB 7 632 Page 39 SECTION 8 PARTS LIST ...
Page 202: ...SB 7 632 Page 41 ...
Page 204: ...SB 7 632 Page 43 301GAE810 A Ref Drawing ...
Page 206: ...SB 7 632 Page 45 ...
Page 208: ...SB 7 632 Page 47 ...
Page 210: ...SB 7 632 Page 49 303GAE810 A Ref Drawing ...
Page 212: ...SB 7 632 Page 51 ...
Page 214: ...SB 7 632 Page 53 ...
Page 216: ...SB 7 632 Page 55 300GAE810 A Ref Drawing ...
Page 218: ...SB 7 632 Page 57 ...
Page 220: ...SB 7 632 Page 59 ...
Page 222: ...SB 7 632 Page 61 302GAA810 A Ref Drawing ...
Page 224: ...SB 7 623 Page 63 ...
Page 226: ...1300 998 784 STGGLOBAL NET OPERATORS MANUAL Sutorbilt P Series Sec on 5 ...
Page 245: ...SB 7 622 Page 12 1 PIPE STEEL 2 SCH 80 2 MED CARBON STEEL 1 2 FIGURE 9 GEAR DRIVER SK2150 ...
Page 258: ...SB 7 622 Page 25 SECTION 8 PARTS LIST 300GAF810 B Ref Drawing ...
Page 260: ...SB 7 622 Page 27 300GAG810 A Ref Drawing ...
Page 262: ...SB 7 622 Page 29 300GAH810 A Ref Drawing ...
Page 265: ......
Page 266: ...1300 998 784 STGGLOBAL NET OPERATORS MANUAL Lofa Manual Sec on 6 ...
Page 294: ...1300 998 784 STGGLOBAL NET OPERATORS MANUAL Excava on Hydro SWMS Sec on 7 ...
Page 314: ...1300 998 784 STGGLOBAL NET OPERATORS MANUAL Pressure Cleaner Water SWMS Sec on 8 ...