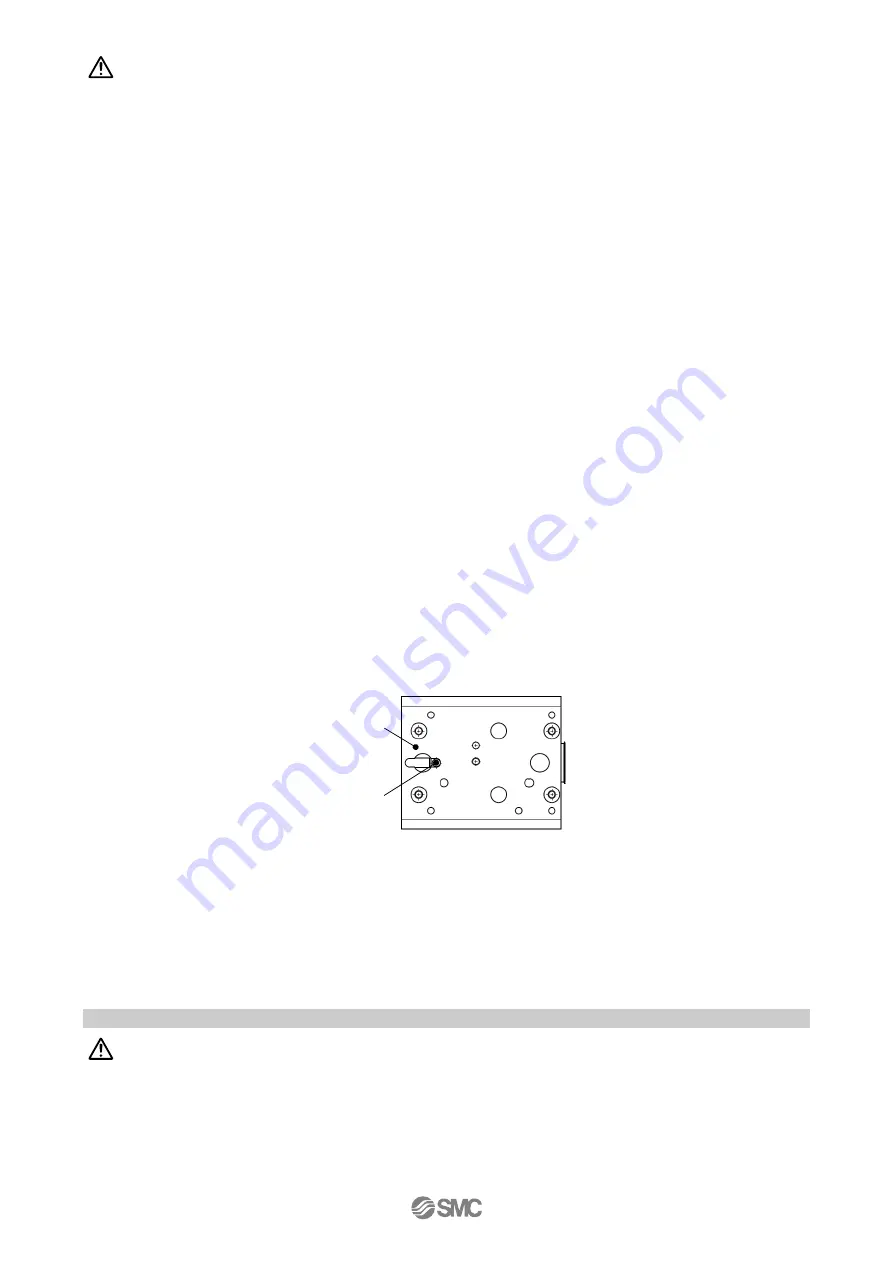
- 49 -
(1) Operate within the limits of the maximum usable stroke.
The stopper will be damaged if the Card Motor is used with a stroke outside the maximum stroke
limits. Refer to the Card Motor specifications for maximum strokes.
(2) Do not apply a load outside the specifications.
The Card Motor should be fitted for the application based on the maximum workload and allowable
moments. If the product is used outside the specifications, the excess load applied to the guide will
lead to play in the guide, decrease in accuracy and the life span of the product will be shortened.
(3) When the product is repeatedly cycled with short strokes, operate it at a full stroke at least
once every 10 strokes.
Otherwise, the parts of guides where it is being used may run out of lubrication.
(4) In pushing operation use thrust force setting values within the allowable limits based on the
used duty ratio.
If thrust force setting values outside the allowable limits are used, it may cause overheating of the
Card Motor, the work piece or the mounting surface.
(5) Strong magnet
The Card Motor contains a strong rare-earth magnet, whose magnetic field may affect the work
piece. Mount the work piece away from the Card Motor far enough to prevent the magnetic field
from affecting the work piece.
(6) Do not use the product in applications where impact or excessive external force is applied to it.
The Card Motor is equipped with a stopper to prevent the table from coming off and to be resistant to
the light impacts generated when returning to Origin position and when transferring work pieces
within the spevcified limits. Excessive external force or impact may damage the Card Motor, so
install a separate external stopper if the operating conditions require.
(7) It is not possible to perform [Return to Origin Position] during another operation.
It is not possible to perform [Return to Origin position] during positioning and pushing operation.
(8) The flatness of the mounting surface of the table and rail must be 0.02 mm or less.
Insufficient flatness of the mounting base for the Card Motor, or of a work piece mounted to it can
cause play in the guide and an increase in the sliding friction.
5. 2 Handling Precautions
(1) Do not touch the product when it is energized or for some time after it has been de-energized.
The surface temperature of the Card Motor can increase up to approximately 70
o
C depending on
the operating conditions. Energizing alone may also cause the temperature to rise. Do not touch the
Card Motor during operation or when energized to prevent burns or other injuries.
Caution
Warning
Card Motor rail
(bottom)
Stopper