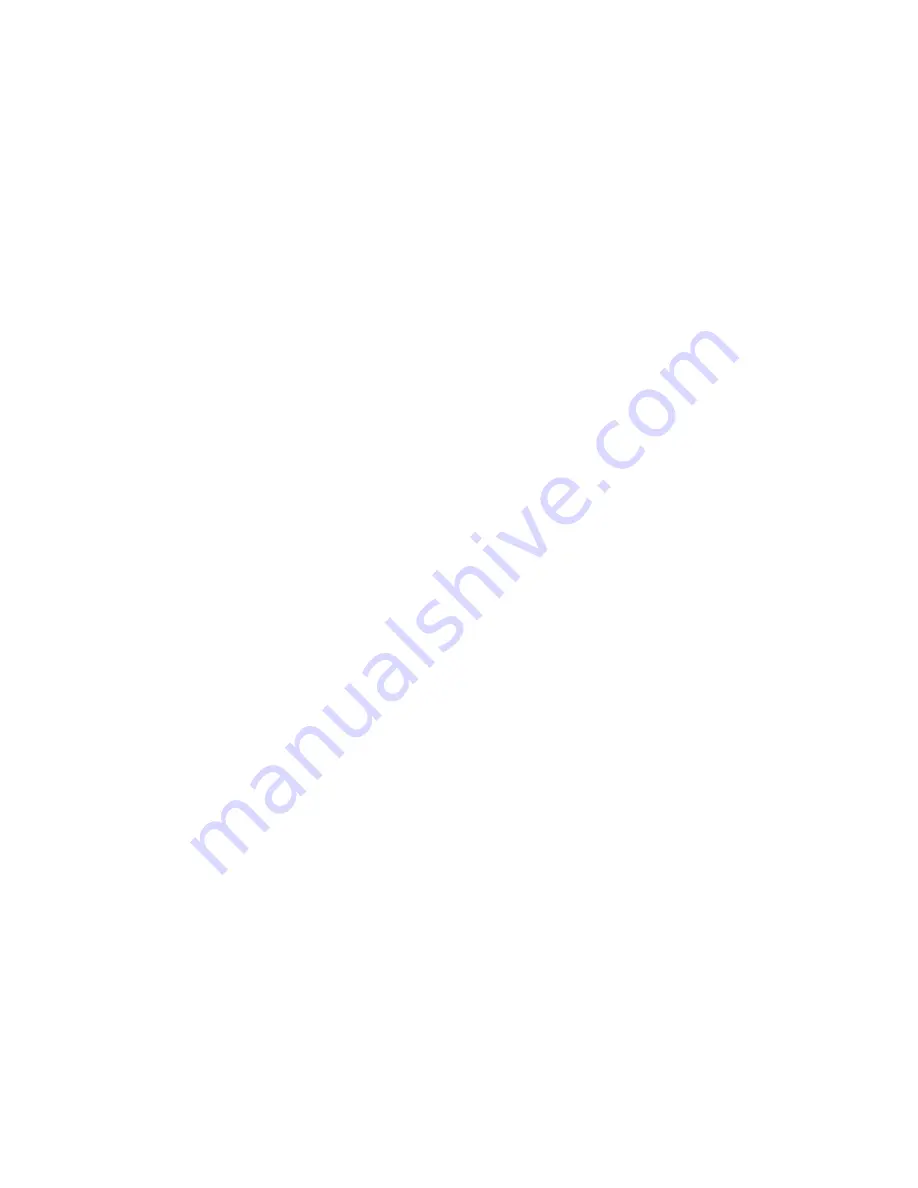
NOTE
In order to accommodate clearer type, larger charts and graphs, and more
detailed illustrations, this edition of the IO-320 Series Operator’s Manual,
Lycoming Part Number 60297-31 is presented in an 8-1/2 x 11 inch
format. This edition is a complete manual, current as of the date of issue.
The manual incorporates all previously issued revisions.
This manual will be kept current by revisions available from Lycoming
distributors or from the factory. All revisions will be accompanied by an
Operator’s Manual Revision page which will identify the revision level, the
date of the revision, and the pages revised, added or deleted. All revisions
will be supplied in the 8-1/2 x 11 inch format.
Содержание AIO-320
Страница 9: ...LYCOMING OPERATOR S MANUAL vi ...
Страница 11: ...This Page Intentionally Left Blank ...
Страница 15: ...This Page Intentionally Left Blank ...
Страница 17: ...This Page Intentionally Left Blank ...
Страница 23: ...This Page Intentionally Left Blank ...
Страница 32: ...LYCOMING OPERATOR S MANUAL SECTION 3 IO 320 SERIES OPERATING INSTRUCTIONS IO 320 A E Series 3 9 ...
Страница 33: ...SECTION 3 LYCOMING OPERATOR S MANUAL OPERATING INSTRUCTIONS IO 320 SERIES IO 320 A Series 3 10 ...
Страница 34: ...LYCOMING OPERATOR S MANUAL SECTION 3 IO 320 SERIES OPERATING INSTRUCTIONS IO 320 E Series 3 11 ...
Страница 36: ...LYCOMING OPERATOR S MANUAL SECTION 3 IO 320 SERIES OPERATING INSTRUCTIONS IO 320 B D AIO 320 LIO 320 3 13 ...
Страница 37: ...SECTION 3 LYCOMING OPERATOR S MANUAL OPERATING INSTRUCTIONS IO 320 SERIES IO 320 C Series LIO 320 C 3 14 ...
Страница 38: ...LYCOMING OPERATOR S MANUAL SECTION 3 IO 320 SERIES OPERATING INSTRUCTIONS IO 320 C Series LIO 320 C 3 15 ...
Страница 39: ...This Page Intentionally Left Blank ...
Страница 41: ...This Page Intentionally Left Blank ...
Страница 47: ...This Page Intentionally Left Blank ...
Страница 59: ...This Page Intentionally Left Blank ...
Страница 65: ...This Page Intentionally Left Blank ...
Страница 70: ...LYCOMING OPERATOR S MANUAL SECTION 7 IO 320 SERIES INSTALLATION AND STORAGE Figure 7 2 Fuel Injector 7 5 ...
Страница 71: ...SECTION 7 LYCOMING OPERATOR S MANUAL INSTALLATION AND STORAGE IO 320 SERIES Figure 7 3 Magneto Connections 7 6 ...
Страница 74: ...LYCOMING OPERATOR S MANUAL SECTION 7 IO 320 SERIES INSTALLATION AND STORAGE 7 9 ...
Страница 75: ...SECTION 7 LYCOMING OPERATOR S MANUAL INSTALLATION AND STORAGE IO 320 SERIES 7 10 ...
Страница 77: ...This Page Intentionally Left Blank ...
Страница 79: ...SECTION 8 LYCOMING OPERATOR S MANUAL TABLES IO 320 SERIES 8 2 ...
Страница 80: ...LYCOMING OPERATOR S MANUAL SECTION 8 IO 320 SERIES TABLES 8 3 ...